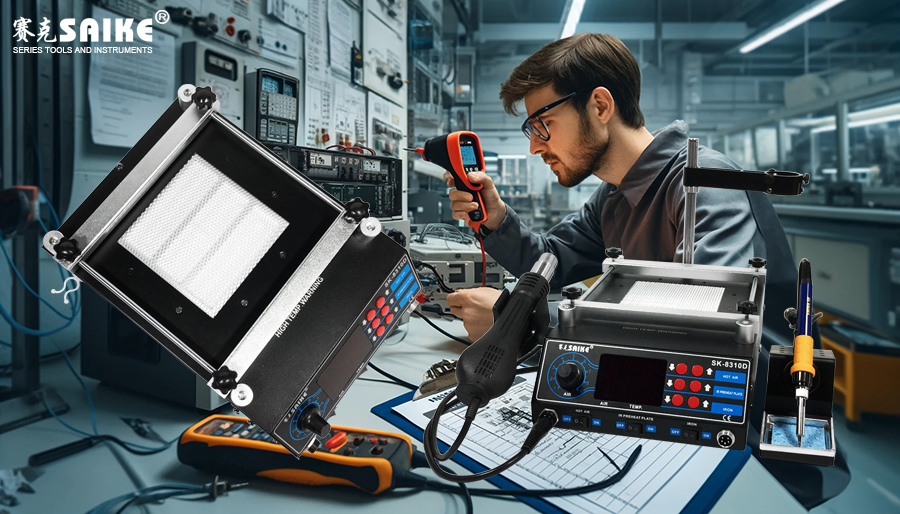
SK-YJ000YRT-KP 100014
Preheating stations are crucial equipment in electronic manufacturing and repair, used to preheat circuit boards and other components to optimize the soldering process. However, like all mechanical equipment, preheating stations can encounter technical faults. Understanding how to identify and address these common issues can not only reduce equipment downtime but also extend the equipment’s lifespan. This article explores the common faults and solutions for preheating stations.
I. Common Faults and Diagnostics
1.Preheating Station Not Heating
– Cause: Potential reasons include power issues, damaged heating elements, faulty temperature controllers, or internal connection problems.
– Diagnostic: Check if the power cord is properly connected and the socket is live; use a multimeter to check if the resistance of the heating element and temperature sensor falls within the normal range; inspect if the control panel display is functioning normally.
2.Inaccurate Temperature Control
– Cause: Faulty temperature sensor, incorrect controller settings, or calibration deviations.
– Diagnostic: Verify if the controller settings are correct; use a calibrated thermal imaging camera or external thermometer to check the actual working temperature; inspect if the temperature sensor is fixed in the correct position.
3.Preheating Station Overheating
– Cause: Failure of temperature control, incorrect sensor placement, or software malfunction.
– Diagnostic: Examine the temperature control system settings and functions; confirm that the sensor is installed correctly and not damaged; check if there are any errors in the software settings or if an update is required.
4.Power Issues
– Cause: Damaged power cord, tripped circuit protector, or faulty internal power components.
– Diagnostic: Inspect the power cord and plug for visible damage; reset the protector and check if the circuit is overloaded; examine internal power components like transformers or capacitors.
II. Solutions
1.Replace Damaged Heating Elements
– After confirming damage to the heating element, replace it with a new one according to the manufacturer’s instructions. Ensure to perform this operation after disconnecting the power to prevent electric shock.
2.Recalibrate the Temperature Sensor
– If temperature readings are inaccurate, recalibration of the temperature sensor may be necessary. Follow the equipment manual for calibration or seek professional service.
3.Repair or Replace the Power Cord
– If the power cord or plug is damaged, replace it immediately, avoiding temporary fixes like using tape.
4.Update or Reset Software
– For software-related issues, try resetting or updating to the latest version. This may require manufacturer support or downloading the latest software from their website.
5.Professional Repair
– For complex internal power issues or controller failures, consider seeking professional repair services if simple troubleshooting doesn’t solve the problem.
III. Preventive Measures
1.Regular Maintenance
– Follow the manufacturer’s recommended schedule for regular inspection and maintenance of the preheating station, including cleaning, checking wires and connections, and testing functionality.
2.Operational Training
– Ensure all operators receive proper training on the correct operation of the equipment and safety precautions.
3.Create Maintenance Records
– Maintenance records help track the equipment’s maintenance history and regular inspections, facilitating timely identification and resolution of potential issues.
IV. Conclusion
Proper maintenance and timely troubleshooting of preheating stations are crucial for ensuring continuity and quality in electronic manufacturing and repair. By following the aforementioned diagnostics and solutions, common faults in preheating stations can be effectively addressed, ensuring stable equipment operation. Additionally, establishing comprehensive maintenance and operational training programs is key to preventing faults and extending the equipment’s lifespan.