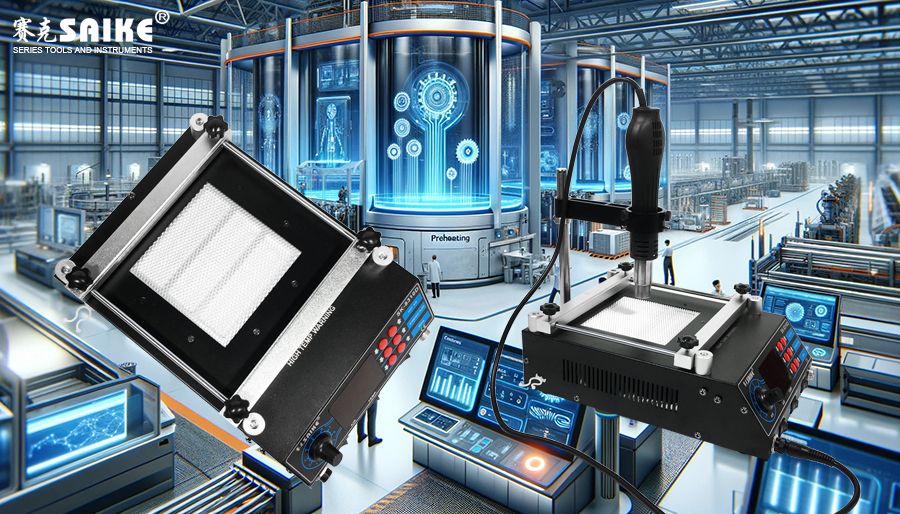
SK-YJ000YRT-KP 100026
Preheating stations play a crucial role in electronic manufacturing and repair, improving soldering quality, reducing material losses, and enhancing product reliability. With the continuous advancement of technology, preheating station technology is constantly evolving and improving to meet more efficient and environmentally friendly production demands. This article explores the future trends and possible development directions of preheating station technology.
I. Intelligence and Automation
1.Integrated Smart Control Systems:
– Future preheating stations will become more intelligent, equipped with advanced sensors and microprocessors that can monitor and adjust the heating process in real-time. These systems will optimize heating parameters through machine learning algorithms, automatically adjusting heating speed and temperature to adapt to different production conditions and material characteristics.
2.Integration with Manufacturing Execution Systems (MES):
– Preheating station operations will become more automated and seamlessly integrated with the factory’s MES system, enabling instant data transmission and analysis. This will help production managers better monitor the production process, predict maintenance needs, and reduce human error.
II. Energy Efficiency and Environmental Protection
1.Energy-saving Design:
– With rising energy costs and increasing environmental requirements, future preheating stations will adopt more efficient heating technologies and energy-saving materials. For example, using more efficient thermal insulation materials and low-power heating elements can reduce energy consumption and operating costs.
2.Environmentally Friendly Materials and Processes:
– The materials and processes used to produce preheating stations will become more environmentally friendly. Manufacturers will adopt recyclable materials and reduce the use of harmful chemicals, such as using non-toxic materials that comply with RoHS and REACH standards.
III. Technological Innovation and Material Compatibility
1.Application of Nanotechnology and New Materials:
– Utilizing nanotechnology to improve the performance of heating elements, such as using materials with better thermal conductivity like carbon nanotubes or graphene, can provide faster and more uniform heating effects.
2.Adapting to Multiple Material Needs:
– As the use of new materials and composites increases in the electronics industry, preheating stations will need to adapt to a wider range of material types. Future preheating stations will be able to adjust to specific heating needs for traditional plastics, new high-performance polymers, and various metal alloys.
IV. Enhanced User Interface and Experience
1.Interactive User Interface:
– Preheating stations will be equipped with more intuitive and user-friendly interfaces, such as touch screens and graphical user interfaces (GUI), making operation simpler and reducing the need for operational training.
2.Remote Monitoring and Diagnostics:
– Utilizing Internet of Things (IoT) technology, preheating stations will enable remote monitoring and diagnostics. Users can remotely check equipment status, receive maintenance and fault warnings, and even perform remote troubleshooting through smart devices.
V. Summary
With the continuous development of technology, preheating stations will become more intelligent, efficient, and environmentally friendly. These advancements will not only improve manufacturing efficiency and product quality but also help reduce production costs and environmental impact. The future development of preheating station technology will continue to support innovation and growth in the electronics manufacturing industry, bringing more operational convenience and production flexibility.