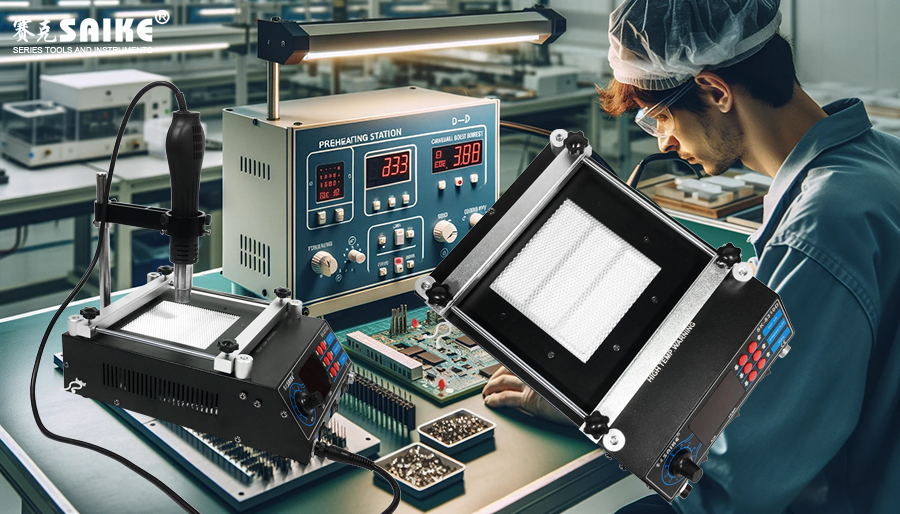
SK-YJ000YRT-KP 100016
Surface Mount Technology (SMT) is one of the most commonly used assembly methods in modern electronic manufacturing, involving the direct mounting of small Surface-Mount Devices (SMDs) onto the circuit board. In this process, the preheating station plays a crucial role, optimizing the soldering process by preheating the circuit board, thereby improving production efficiency and product quality. This article delves into the significance and importance of the preheating station in SMD assembly.
I. Functions and Roles of the Preheating Station
The primary function of the preheating station is to heat the circuit board before soldering, aiming to:
1.Reduce Thermal Stress:
– During the SMD soldering process, the circuit board is suddenly exposed to high temperatures. Preheating allows the board to gradually reach a higher temperature, minimizing thermal stress on the material and preventing warping or delamination.
2.Enhance Soldering Quality:
– Preheating helps the solder reach its melting point more quickly during the soldering process, facilitating the flow and spreading of solder on the pads, thus reducing the occurrence of cold solders or poor solder joints.
3.Increase Component Reliability:
– Even heating ensures that all solder joints are completed at optimal temperatures, enhancing the mechanical strength of the solder joints and boosting the reliability of the final product.
II. Application of Preheating Station in SMD Assembly
In the SMD assembly process, the preheating station is typically located in the preparation stage before soldering:
1.Preheating Process:
– Before entering the soldering line, the circuit board is first placed on the preheating station. The preheating station gradually heats the board according to a preset temperature curve, usually between 100°C and 150°C, depending on the board material and solder characteristics.
2.Soldering Process:
– The preheated board then proceeds to the soldering stage, whether it’s wave soldering or reflow soldering, and preheating ensures uniformity and efficiency during the soldering process.
3.Quality Control:
– Boards that have undergone preheating treatment typically have a lower defect rate in SMD assembly, resulting in faster quality checks afterward.
III. Optimization Strategies for the Preheating Station
To maximize the benefits of the preheating station in SMD assembly, the following optimization strategies can be adopted:
1.Temperature Monitoring and Control:
– Use high-precision temperature sensors and PID controllers to monitor and adjust the temperature of the preheating station, ensuring stability and repeatability during the heating process.
2.Adaptation to Different Boards and Components:
– Adjust preheating temperatures and times based on different circuit board materials and component sizes, especially for multilayer boards or boards with large components.
3.Maintenance and Calibration:
– Regularly maintain and calibrate the preheating station to ensure equipment accuracy and reliability.
IV. Conclusion
The role of the preheating station in SMD assembly cannot be overlooked. Through preheating, the soldering process is optimized, manufacturing defects are reduced, and production efficiency and overall product reliability are improved. Proper configuration and use of the preheating station are crucial investments for any enterprise pursuing high-quality electronic manufacturing.