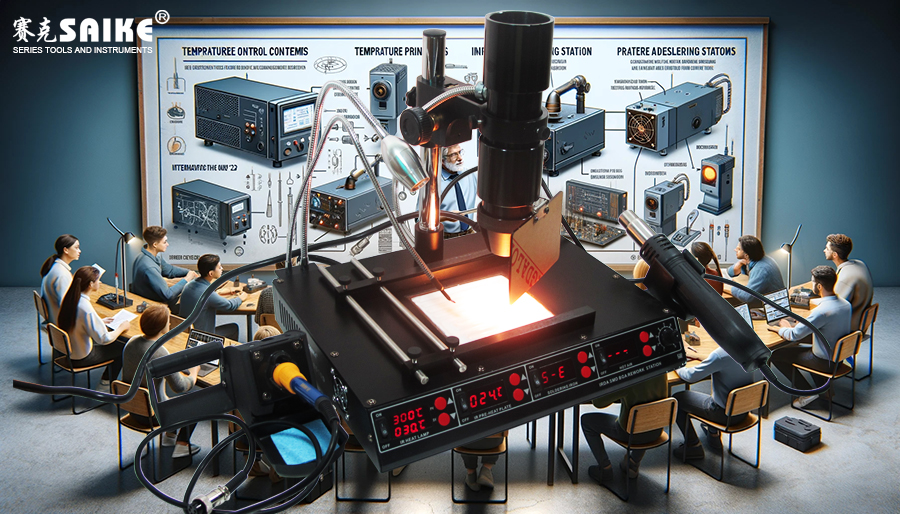
SK-YJ000HWXCHT-KP 100026
The infrared desoldering station, an essential tool in electronic repair and manufacturing, is widely used due to its precise heating control and non-contact operation. In learning and mastering the infrared desoldering station, it is crucial to understand its working principle, operational skills, temperature control, and practical application scenarios to ensure efficient and safe operation. This article summarizes the course content of the infrared desoldering station and highlights key knowledge points.
I. Basic Principles and Structure of Infrared Desoldering Station
1.Working Principle:
– The infrared desoldering station generates infrared radiation through an infrared emitter, directly transferring heat to the circuit board or solder joints, melting the solder and enabling component soldering or desoldering.
2.Main Structure:
– Infrared Emitter: Emits infrared rays to heat the target area, typically using halogen lamps or ceramic lamp tubes as heating elements.
– Optical System: Ensures infrared focusing and accurate positioning of target solder joints.
– Temperature Control System: Real-time monitoring and adjustment of heating temperature through temperature sensors and PID controllers.
– Operation Panel: Used to set parameters such as temperature, time, and heating power.
II. Operational Skills of Infrared Desoldering Station
1.Temperature Setting and Temperature Curve:
– Set preheating, soldering, and cooling temperature curves based on solder type and circuit board material to ensure sufficient solder melting and strong connections.
– Adjust heating power in a timely manner to maintain a stable temperature curve through multi-zone temperature control and real-time monitoring technology.
2.Optical Positioning and Thermal Insulation Measures:
– Use the optical system to accurately position the heating area of the infrared emitter, ensuring the target solder joint is completely covered within the heating range.
– Provide thermal insulation protection to adjacent sensitive components or non-target solder joints to avoid heat damage.
3.Solder Joint Cleaning and Quality Inspection:
– Clean solder residue after desoldering to ensure the solder joint surface is free of oxides or solder slag.
– Use inspection tools such as microscopes to check the surface and connection quality of solder joints, ensuring no problems such as cold solder joints or false soldering.
III. Practical Application Scenarios and Technical Challenges
1.High-Density Integrated Circuits:
– The complex solder joint structure of high-density integrated circuits is prone to heat damage. The multi-zone heating and real-time monitoring technology of the infrared desoldering station ensure uniform solder joint temperature.
2.Multi-Layer Circuit Boards:
– Multi-layer circuit boards are prone to thermal stress during soldering and desoldering, leading to delamination or warping. Reasonable preheating and soldering temperature settings can reduce temperature differences.
3.Micro and Flexible Components:
– Micro and flexible components have fragile structures and small solder joints. The infrared desoldering station ensures soldering quality through precise temperature control and heating area positioning.
4.Technical Challenges and Solutions:
– Precise Temperature Control: Utilize multi-zone heating and temperature curve programming to ensure the heating temperature matches the solder characteristics.
– Thermal Insulation and Shielding: Use thermal insulation materials or shields for non-target areas to concentrate heating on target solder joints.
IV. Regular Maintenance and Equipment Upgrades
1.Regular Maintenance:
– Regularly clean the reflector, lamp tube, and lens of the infrared emitter to ensure normal operation.
– Calibrate temperature sensors and control systems to ensure accurate temperature data.
2.Equipment Upgrades:
– Replace high-efficiency infrared lamp tubes, upgrade control system software and firmware to ensure the infrared desoldering station meets the temperature control requirements of new-generation components.
V. Summary
The infrared desoldering station course covers equipment working principles, operational skills, practical application scenarios, and technical challenges. Mastering key knowledge points such as temperature setting, optical positioning, thermal insulation measures, and solder joint cleaning ensures precise and efficient soldering and desoldering in the repair of high-density, multi-layer, and complex packaged electronic components. Regular maintenance and equipment upgrades further enhance the stability and performance of the infrared desoldering station, ensuring its continued efficiency in practical applications.