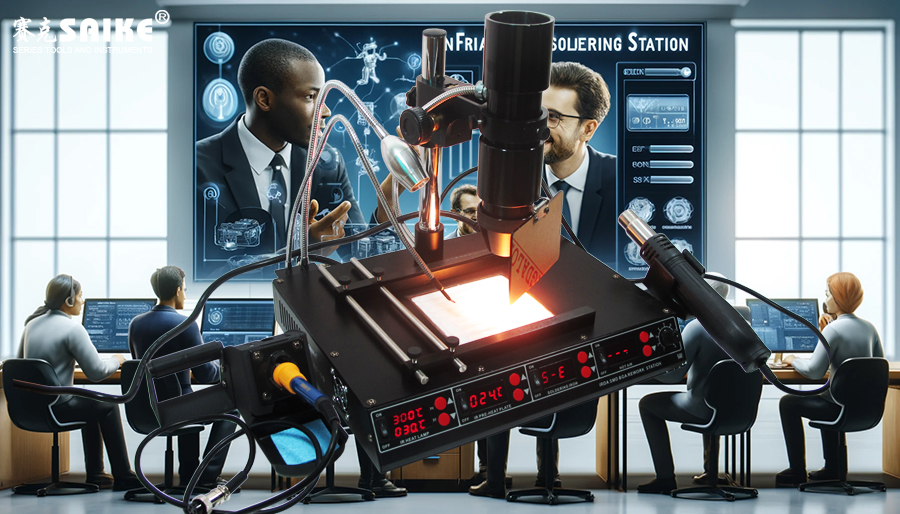
SK-YJ000HWXCHT-KP 100025
The infrared desoldering station is an efficient and precise tool for soldering and desoldering, especially suitable for high-density, multilayer, and complex packaged electronic components. However, due to its advanced technical characteristics and operational requirements, users may encounter a series of operational questions and technical challenges. This article provides insights for users by answering common questions and analyzing key technical challenges, helping them better master the use of infrared desoldering stations.
I. Frequently Asked Questions About Infrared Desoldering Stations
1.Q: How to choose a suitable temperature profile?
– Solder type: The melting point of the solder determines the temperature setting during soldering and desoldering. The melting point of tin-lead alloy is about 183°C, while lead-free solder is about 217°C.
– Solder joint structure: For high-density solder joints, the temperature profile should have a smooth transition to avoid rapid temperature increases.
– Circuit board material: Multilayer or flexible circuit boards require a longer preheating time and moderate soldering temperature.
2.Q: How to locate and maintain precise heating areas?
– Use the optical system or laser locator provided by the infrared desoldering station to determine the exact location of the solder joints.
– Adjust the angle and focal length of the infrared emitter to ensure that the target area is completely covered within the heating range.
3.Q: How to avoid damaging other components during heating?
– Use heat-insulating materials or shields to isolate adjacent sensitive components to prevent accidental heating.
– Select the multi-zone heating function to ensure that the temperature outside the target area does not exceed the heat resistance range of the components.
4.Q: How to determine if the temperature profile of the solder joint is correct?
– Use infrared or thermocouple sensors to monitor the solder joint temperature in real time, ensuring that the actual temperature matches the preset curve.
– Check the surface and connection of the solder joints through a microscope or soldering test tool to confirm whether the solder is completely melted and firmly connected to the circuit board.
II. Technical Challenges of Infrared Desoldering Station
1.Precise temperature control:
– Challenge: Different components and circuit boards have different heat resistance, requiring precise setting of temperature profiles for preheating, heating, and cooling stages.
– Solution: Program a reasonable temperature profile, utilize multi-zone heating and real-time temperature monitoring technology, and adjust heating power in a timely manner to maintain stable solder joint temperature.
2.Heating of multilayer and high-density circuit boards:
– Challenge: Multilayer and high-density circuit boards have poor thermal conductivity, and thermal stress may cause circuit board delamination or component damage.
– Solution: Perform uniform preheating first to reduce thermal stress; simultaneously control the heating temperature in different areas to ensure uniform heating of each layer.
3.Protection of sensitive components:
– Challenge: Adjacent sensitive components are easily affected by heating, resulting in warping, soldering, or damage.
– Solution: Use heat-insulating materials or reflectors to protect sensitive areas; adjust the angle and focal length of the infrared emitter to focus heating on the target solder joints.
4.Cold soldering and insufficient soldering:
– Challenge: Incomplete melting of solder or rapid temperature increase may lead to cold soldering or insufficient soldering of solder joints, affecting the connection quality.
– Solution: Set a reasonable soldering temperature profile according to the type of solder to ensure that the solder melts sufficiently and is firmly connected to the components and circuit board.
III. Summary
By answering common questions and analyzing technical challenges related to infrared desoldering stations, it can be seen that temperature control, precise positioning, and sensitive component protection are the keys to ensuring soldering and desoldering quality. In practical operations, reasonable selection of temperature profiles, optimization of multilayer board heating strategies, and adoption of heat insulation and shielding measures can effectively address these technical challenges, improving the operational efficiency and soldering quality of infrared desoldering stations.