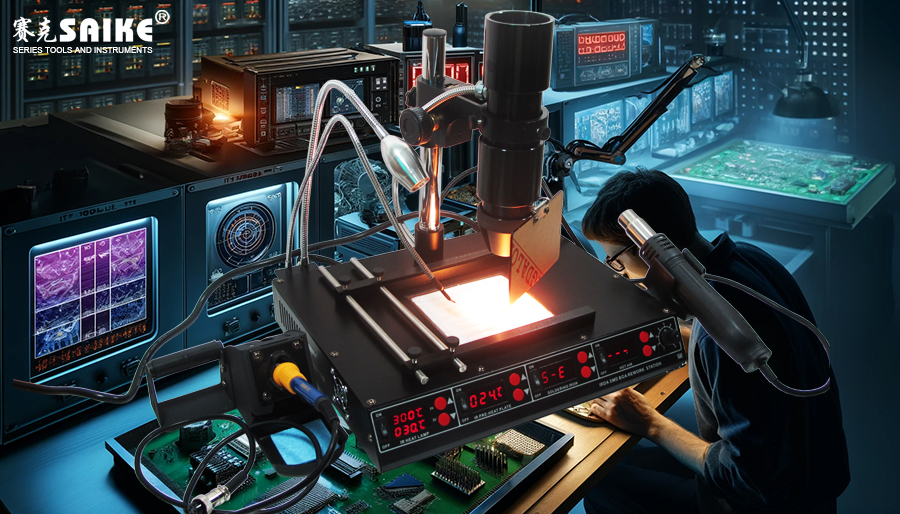
SK-YJ000HWXCHT-KP 100014
In electronic manufacturing and repair, high-density integrated circuits (ICs) and multilayer circuit boards represent technically challenging components. High-density integrated circuits often feature complex designs and micro-packaging, while multilayer boards consist of multiple conductive and insulating layers. An infrared rework station, with its precise temperature control and uniform heating methods, serves as an ideal tool for handling such components. This article delves into the strategies employed by an infrared rework station to process high-density integrated circuits and multilayer boards, ensuring accurate, safe, and efficient soldering and desoldering procedures.
I. Understanding the Challenges of High-Density ICs and Multilayer Boards
1.High-Density Integrated Circuits (ICs):
– Typically packaged in BGA, QFN, or CSP formats, featuring tight spacing between components and sensitivity to heat.
– Precise temperature control and heating range are crucial for successful soldering and desoldering operations.
2.Multilayer Boards:
– Comprise multiple conductive and insulating layers, with increasing layers leading to poorer thermal conductivity.
– Prone to thermal stress and delamination during heating, necessitating longer preheating times and precise temperature control.
II. Heating Strategies of the Infrared Rework Station
1.Multi-Zone Temperature Control:
– Leveraging the multi-zone heating capability of the infrared rework station, temperatures can be independently controlled in target areas, minimizing thermal stress and component damage due to overall heating.
– When heating multilayer boards, controlling the temperature of each layer separately ensures uniform heating.
2.Preset Temperature Profiles:
– Specialized temperature profiles are tailored for different high-density IC packages and multilayer boards, ensuring smooth and uniform transitions during preheating, heating, and cooling
phases.
– Adequate preheating time is essential to uniformly heat the layers of a multilayer board and reduce thermal stress.
3.Preheating and Soldering Temperatures:
– Preheating temperatures typically range from 100°C to 150°C, depending on the heat resistance of the board and components.
– Soldering and desoldering temperatures should slightly exceed the melting point of the solder to prevent damage to solder joints and components due to rapid or excessive heating.
III. Practical Operation Techniques
1.Precise Positioning:
– Accurately locate the high-density ICs and solder joints to be soldered or desoldered, using the optical system of the infrared emitter for precise targeting.
– For large multilayer boards, ensure stable placement of the target component on the work surface to prevent board movement or warping.
2.Temperature Monitoring and Adjustment:
– Utilize precise infrared sensors or thermocouples for real-time monitoring of solder joint and board temperatures, adjusting heating power based on feedback.
– Maintain a stable implementation of the preset temperature profile, avoiding temperature fluctuations and sudden spikes during the heating process.
3.Localized Shielding:
– Employ reflective hoods or insulating materials to locally shield non-target areas, preventing heat damage to adjacent sensitive components.
4.Solder Joint Cleaning and Testing:
– Thoroughly clean solder joints after desoldering and use soldering test equipment to ensure joint integrity and freedom from residues.
– For multilayer boards, verify that all conductive layers are properly connected, avoiding delamination and short circuits caused by heating or soldering.
IV. Conclusion
The infrared rework station effectively handles high-density integrated circuits and multilayer boards through techniques such as multi-zone temperature control, preset temperature profiles, and precise positioning. Precise control and real-time monitoring during preheating, heating, and cooling phases are crucial to ensuring solder joint integrity and component safety. By leveraging the advanced features of the infrared rework station, the failure rate during soldering and desoldering processes can be significantly reduced, guaranteeing the quality of high-density electronic components and multilayer circuit boards.