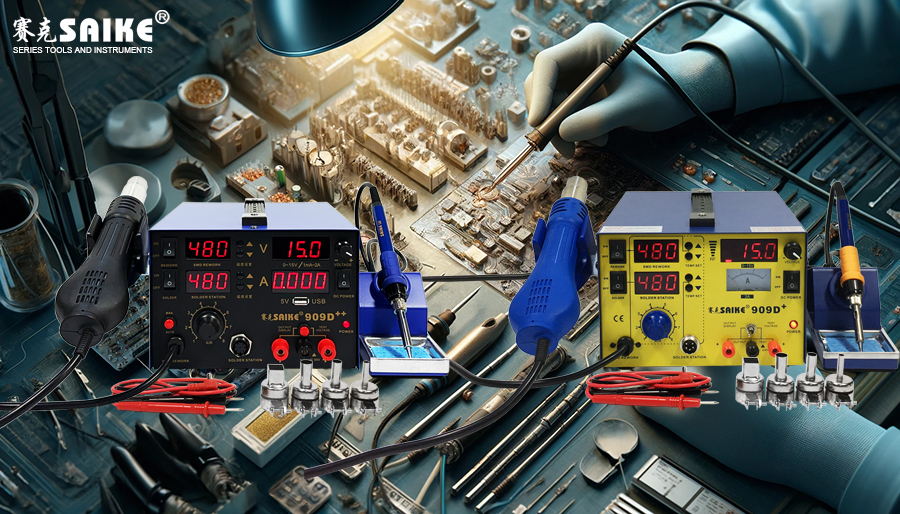
SK-YJ000RFSHY-KP 100022
Solder is an essential material in the electronic soldering process. Choosing the right solder and mastering the correct usage skills are crucial for soldering quality and work efficiency. This article will introduce the selection criteria and usage skills of solder in detail, helping electronic repair personnel improve soldering effects.
I. Selection of Solder
1.Composition of Solder
Solder is mainly composed of tin (Sn) and lead (Pb) or other metals (such as silver and copper). Common types of solder include leaded and lead-free solder:
– Leaded Solder: The common proportion is 60/40 (Sn60Pb40), with a melting point of about 183℃. It has good fluidity and wettability.
– Lead-free Solder: The common composition is tin-silver-copper (SAC), such as Sn96.5Ag3Cu0.5, with a melting point of about 217℃. It is environmentally friendly, meets the RoHS standard, but requires a higher operating temperature.
2.Selection Criteria of Solder
– Selection Based on the Soldering Object
– Small components and precision soldering: Choose fine-diameter solder wire (below 0.5mm) for fine control of the solder amount.
– Large components and thick solder joints: Choose a thicker diameter solder wire (0.8mm or more) to improve soldering efficiency.
– Selection Based on Environmental Requirements
– Strict environmental requirements: Choose lead-free solder that meets the RoHS standard and reduces the use of harmful substances.
– General applications: Choose traditional leaded solder with good fluidity and low operating temperature.
– Selection Based on Operating Temperature
– Low-temperature soldering: Choose solder with a lower melting point (such as Sn42Bi58), suitable for heat-sensitive components.
– High-temperature soldering: Choose solder with a higher melting point (such as Sn96.5Ag3Cu0.5), suitable for high-temperature operating environments.
– Selection of Solder Forms
– Solder wire: The most common, suitable for manual soldering.
– Solder paste: Suitable for surface mount technology (SMT) and reflow soldering.
– Solder bar: Suitable for wave soldering and mass soldering operations.
II. Usage Skills of Solder
1.Preparation
– Clean the solder joints: Use flux (soldering flux) or cleaner to clean the soldering site, removing oxides and dirt to ensure a clean solder joint surface.
– Preheat the soldering station: Set the appropriate temperature and preheat the soldering station to ensure temperature stability.
2.Soldering Skills
a.Usage of Solder Wire
– Soldering Method:
– Heat the solder joint: Place the soldering iron tip on the solder joint and heat it for a few seconds to fully preheat the solder joint.
– Add solder: Bring the solder wire close to the junction of the soldering iron tip and the solder joint, and wait for the solder to melt and flow to cover the solder joint.
– Remove the solder wire: When the solder amount is appropriate, remove the solder wire, continue heating for a moment to ensure that the solder is completely melted and attached.
– Remove the soldering iron: Finally, remove the soldering iron tip, keep the solder joint stationary, and wait for the solder to cool and solidify.
– Precautions:
– Maintain an appropriate distance between the solder wire and the soldering iron tip to avoid excessive contact, which may cause solder splashes.
– Control the solder amount to ensure that the solder joints are full but not excessive, to avoid short circuits and cold solder joints.
b.Usage of Solder Paste
– Soldering Method:
– Apply solder paste: Use a special tool to apply a suitable amount of solder paste to the soldering pad.
– Place components: Accurately place the components to be soldered on the soldering pad coated with solder paste.
– Heat and reflow: Use a hot air gun or reflow soldering equipment to heat, and the solder paste melts and connects the components and soldering pads.
– Precautions:
– The solder paste needs to be fully stirred before use to ensure uniformity.
– When applying solder paste, it should be even and moderate to avoid excess, which may cause short circuits.
c.Soldering Quality Inspection
– Appearance inspection: Check the solder joint surface for smoothness, cracks, and voids.
– Strength test: Gently shake the soldered components to ensure that the solder joints are firm.
– Electrical performance test: Use a multimeter to detect the conductivity and resistance value of the solder joints to ensure good electrical connection.
d.Handling welding problems
– Cold solder joint: If the solder joint is not secure or the contact is poor, the solder joint needs to be reheated and additional solder should be added.
– Short circuit: Excessive solder can cause adjacent solder joints to connect. It is necessary to use a solder sucker or solder wick to remove excess solder.
– Solder joint oxidation: If the surface of the solder joint is blackened or not smooth, flux should be used to clean the solder joint and then resolder it.
e.Safe operation
– Wear protective equipment: Wear protective glasses and gloves during operation to prevent solder splashes from causing injury.
– Good ventilation: Ensure good ventilation in the operating environment to avoid inhaling solder fumes.
– Proper solder storage: Solder should be stored in a dry, cool environment to avoid moisture and deterioration.
III. Conclusion
The selection and use of solder have a significant impact on soldering quality and efficiency. By choosing suitable solder materials and mastering correct methods and techniques, the quality of solder joints can be ensured, work efficiency can be improved, and soldering failures can be reduced. Meanwhile, attention should be paid to safe operations during the soldering process to ensure the health and safety of operators. I hope the suggestions and techniques provided in this article can help electronic maintenance personnel better perform soldering work.