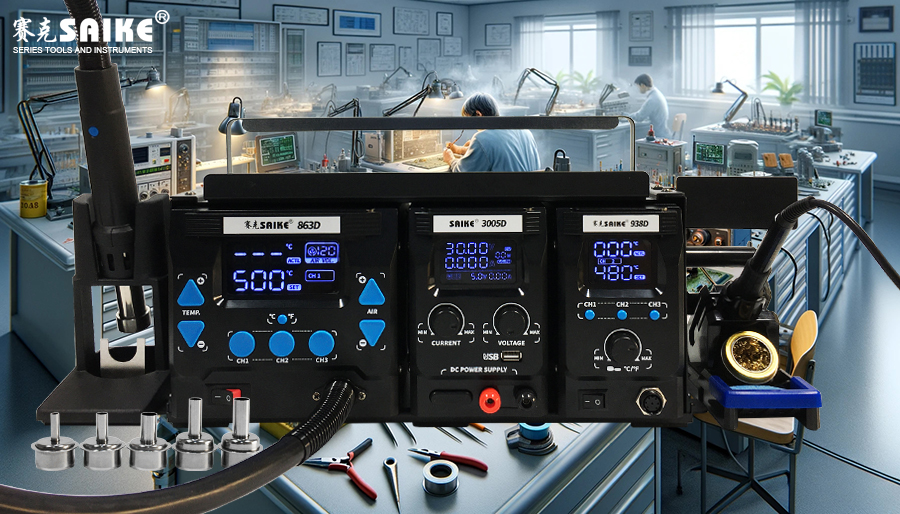
SK-YJ000RFSHY-KP 100048
Conducting a practical test that combines the use of a hot air desoldering station, soldering station, and DC stabilized power supply can effectively assess the skill level and practical application ability of operators. This article will simulate actual maintenance situations and design a series of test steps to help operators proficiently master the use of these tools.
I. Test Preparation
1.Tools and Equipment Preparation
– Hot Air Desoldering Station: Used for dismantling and installing electronic components.
– Soldering Station: Used for soldering electronic components.
– DC Stabilized Power Supply: Used for circuit power supply and testing.
– Auxiliary Tools: Tweezers, soldering tin, soldering wire, soldering paste, solder sucker, flux, cleaning tools (such as alcohol and brushes).
– Test Circuit Board: Prepare a circuit board with faulty components to simulate actual maintenance situations.
2.Safety Measures
– Anti-static Measures: Wear anti-static bracelets, and lay anti-static mats on the workbench.
– Ventilation Measures: Operate in a well-ventilated environment or use exhaust equipment to remove smoke generated during soldering.
– Personal Protection: Wear goggles and masks to prevent splashes and harmful fumes during soldering.
II. Test Items
1.Dismantling Damaged Components
Steps:
a.Identify faulty components: Use a multimeter to detect the circuit board and find damaged components, such as a resistor or integrated circuit (IC).
b.Hot air dismantling:
– Set the temperature of the hot air desoldering station to 300-350℃ and the wind speed to medium.
– Use a hot air gun to heat the solder joints of the faulty component uniformly until the solder melts.
– Carefully remove the damaged component with tweezers.
Assessment Points:
– Whether the temperature and wind speed settings are reasonable.
– Whether the heating is uniform and whether the circuit board is damaged.
– Whether the component dismantling is smooth and whether the soldering pad is intact.
2.Clean the Soldering Pad
Steps:
a.Use a solder sucker: Use a soldering station and solder sucker to clean the residual solder on the soldering pad.
b.Clean the soldering pad: Use alcohol and a brush to clean the soldering pad to remove residues and oxides.
Assessment Points:
– Whether the solder cleaning is thorough and whether the soldering pad is clean.
– Whether the operation of cleaning the soldering pad is standardized and whether the soldering pad is damaged.
3.Install New Components
Steps:
a.Prepare new components: Select suitable replacement components.
b.Solder new components:
– Set the temperature of the soldering station to 350-400℃.
– Place the new component on the soldering pad and solder each pin with soldering wire and an iron.
– Ensure that the solder joints are full, smooth, and free of cold soldering or pores.
Assessment Points:
– Whether the temperature setting is reasonable.
– Whether the soldering is firm and whether the solder joint quality meets the standard.
– Whether the component pins and soldering pads have good contact.
4.Circuit Function Test
Steps:
a.Connect the DC stabilized power supply:
– Set the output voltage and current limit of the DC stabilized power supply within the circuit demand range.
– Use alligator clips or probes to connect the stabilized power supply to the power input of the circuit board.
b.Test circuit function:
– Gradually increase the voltage to the rated value and observe the operation of the circuit board.
– Use a multimeter to measure the voltage at key points to ensure that the circuit function is normal.
Assessment Points:
– Whether the voltage and current settings are accurate.
– Whether the circuit board is operating normally, and whether the voltage at each key point is within the normal range.
5.Troubleshooting and Repair
Steps:
a.Simulate faults: Artificially create a new fault, such as a short circuit or open circuit.
b.Troubleshooting:
– Use a multimeter to detect the circuit and find the fault point.
– Use a hot air desoldering station and soldering station for repair according to the fault type.
Assessment Points:
– Whether the troubleshooting is accurate and whether the operation is quick.
– Whether the repair operation is standardized and whether the fault is completely resolved.
III. Practical Assessment Example
1.Case Background
An IC on a certain circuit board is damaged and needs to be dismantled and replaced, while ensuring that the circuit functions normally after replacement.
2.Operating Steps
a.Dismantling the Damaged IC:
– Set the temperature of the hot air rework station to 320℃ and adjust the airspeed to medium.
– Use a hot air gun to evenly heat the solder joints of the IC. After the solder melts, remove the IC with tweezers.
b.Cleaning the Solder Pads:
– Use a soldering station and a solder sucker to clean the residual solder on the solder pads.
– Clean the solder pads with alcohol and a brush to ensure there are no residues.
c.Soldering the New IC:
– Set the temperature of the soldering station to 370℃.
– Place the new IC on the solder pads and solder each pin of the IC with soldering wire and soldering iron, ensuring that the solder joints are full and smooth.
d.Testing Circuit Functionality:
– Set the output voltage of the DC stabilized power supply to 5V and current limit to 1A.
– Connect the circuit board and gradually increase the voltage to 5V, observing the operation of the circuit.
– Use a multimeter to measure the voltage at key pins of the IC to ensure normal operation.
e.Troubleshooting and Repair:
– Create a new fault by soldering a certain resistance pin open.
– Use a multimeter to detect and locate the open circuit fault.
– Re-solder the resistance pin using a soldering station to fix the open circuit issue.
3.Results Evaluation
– The IC dismantling operation was standardized, and the solder pads were intact.
– The solder pads were thoroughly cleaned, leaving no residues.
– The new IC was securely soldered, and the solder joint quality met the requirements.
– The circuit board functioned normally, and the voltage at key points was correct.
– Troubleshooting was accurate, and repair operations were quick and thorough.
IV. Summary
Through practical tests that simulate actual maintenance situations, operators’ mastery of hot air rework stations, soldering stations, and DC stabilized power supplies can be comprehensively assessed. Operators need to be familiar with the specific operations and precautions of each step and flexibly apply these skills and experiences in practical operations. Through repeated practice and summation, operators can continuously improve their operational skills and maintenance quality.