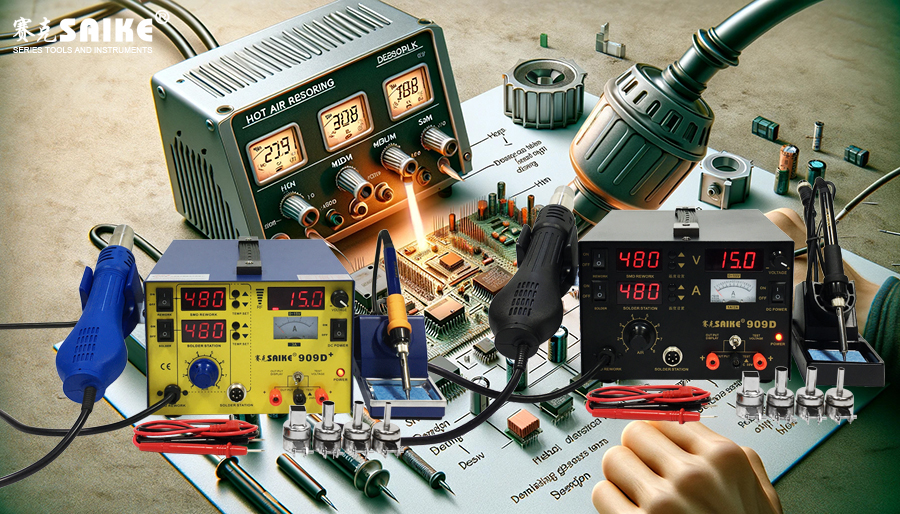
SK-YJ000RFSHY-KP 100009
The hot air rework station is an indispensable tool in electronic repair and manufacturing, where the regulation of temperature and airflow speed is crucial for effective desoldering. Different settings of temperature and airflow speed significantly impact desoldering results, and proper settings can enhance work efficiency while minimizing damage to components and circuit boards. This article delves into the methods of adjusting temperature and airflow speed on a hot air rework station and their effects on desoldering.
I. Temperature Regulation
Temperature is a vital parameter for a hot air rework station, and different temperature settings directly affect the melting speed of solder and the safety of components.
1.High Temperature Setting
– Advantages: Rapid solder melting, reducing desoldering time.
– Disadvantages: Excessively high temperatures can damage sensitive components and circuit boards, potentially causing solder pad detachment or internal component damage.
– Application Scenarios: Suitable for large solder joints and high solder volumes, such as large electrolytic capacitors or high-power components.
2.Medium Temperature Setting
– Advantages: Balances melting speed and safety, reducing the risk of damage.
– Disadvantages: Melting speed is slightly slower compared to high-temperature settings.
– Application Scenarios: Ideal for desoldering general electronic components like IC chips, diodes, resistors, etc.
3.Low Temperature Setting
– Advantages: Maximizes protection for components and circuit boards, suitable for temperature-sensitive components.
– Disadvantages: Slower solder melting, potentially requiring longer heating times.
– Application Scenarios: Appropriate for small SMD components and highly sensitive components, such as special material chips and sensors.
II. Airflow Speed Regulation
Airflow speed is another crucial factor influencing hot air distribution and solder melting. Proper airflow speed settings ensure uniform heat distribution while minimizing impact on surrounding components.
1.High Airflow Speed Setting
– Advantages: Fast heating and wide hot air coverage.
– Disadvantages: May displace or damage small components due to strong airflow, significantly affecting surrounding components.
– Application Scenarios: Suitable for desoldering large solder joints or situations requiring rapid heating.
2.Medium Airflow Speed Setting
– Advantages: Even heating with minimal impact on surrounding components.
– Disadvantages: Moderate heating speed and coverage, suitable for most applications.
– Application Scenarios: Ideal for routine soldering and desoldering operations, such as IC chips and connectors.
3.Low Airflow Speed Setting
– Advantages: Precise heating, minimizing impact on surrounding components.
– Disadvantages: Slower heating speed, suitable for situations requiring limited hot air coverage.
– Application Scenarios: Appropriate for dense circuit boards and small SMD components desoldering, such as small resistors and capacitors.
III. Combined Temperature and Airflow Speed Adjustment
To achieve optimal desoldering results, it is often necessary to adjust both temperature and airflow speed based on specific components and solder joints.
1.High Temperature and High Airflow Speed
– Effects: Rapid desoldering, suitable for large solder joints and heat-resistant components.
– Precautions: Care should be taken to avoid thermal damage to surrounding components.
2.High Temperature and Low Airflow Speed
– Effects: Concentrated heating, minimizing impact on surrounding components.
– Precautions: Suitable for small components, but heating time should be controlled to prevent overheating.
3.Low Temperature and High Airflow Speed
– Effects: Even heating but slower, suitable for large circuit board desoldering.
– Precautions: Avoid prolonged heating to prevent excessive heat accumulation in components.
4.Low Temperature and Low Airflow Speed
– Effects: The gentlest heating method, suitable for extremely sensitive components.
– Precautions: Requires patient operation due to longer heating times.
IV. Adjustment Examples
1.Desoldering SMD ICs
– Recommended Settings: Temperature at 350℃, medium airflow speed.
– Effects: Rapid solder melting while minimizing impact on surrounding small components.
2.Desoldering Large Electrolytic Capacitors
– Recommended Settings: Temperature at 400℃, high airflow speed.
– Effects: Quick melting of large solder volumes, reducing desoldering time.
3.Desoldering Small Resistors
– Recommended Settings: Temperature at 300℃, low airflow speed.
– Effects: Precise heating, avoiding displacement of small components.
V. Conclusion
The adjustment of temperature and wind speed of the hot air soldering station has a direct impact on the soldering effect. The correct setting can improve the soldering efficiency and reduce the damage to components and circuit boards. By flexibly adjusting the temperature and wind speed according to the specific components and solder joints, the best soldering effect can be achieved. Operators need to be familiar with the performance and parameters of the equipment and make reasonable adjustments according to actual needs to ensure the smooth progress of soldering work.