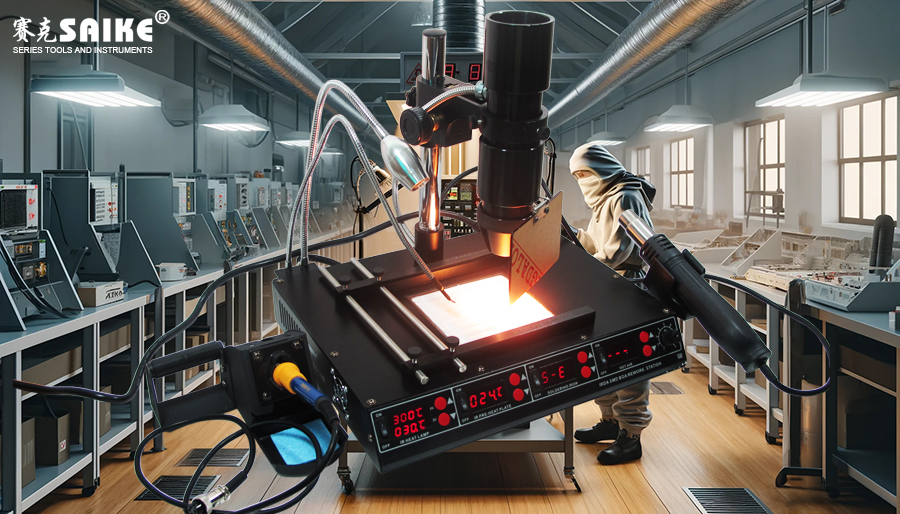
SK-YJ000HWXCHT-KP 100010
In the field of electronic repair and manufacturing, the infrared desoldering station has become a crucial tool for desoldering high-density electronic components due to its precise heating capability. However, to maximize its functionality, it is essential to set up and configure the desoldering station in a suitable working environment. This article will introduce how to establish and configure the optimal working environment for the infrared desoldering station, ensuring efficient and safe operation of the equipment.
I. Environment Selection and Setup
1.Location Selection:
– The workspace should be located in a well-ventilated, clean, and dust-free area to ensure that smoke and harmful gases generated during soldering and desoldering processes can be quickly expelled.
– Avoid working in areas with direct sunlight, high humidity, or extreme temperatures to maintain equipment stability and durability.
2.Lighting and Visibility:
– Ensure adequate lighting in the workspace, especially around the infrared desoldering station’s control panel and work surface, to facilitate technicians’ precise component positioning and temperature monitoring.
– Install auxiliary lighting to eliminate shadows that may obstruct the work view.
3.Safe Space:
– Maintain sufficient operational space around the equipment, allowing technicians to easily access and move around during operations.
– Keep flammable items away from the equipment to avoid potential fire hazards.
II. Equipment Configuration and Installation
1.Workbench and Support:
– Choose a stable workbench for the infrared desoldering station to prevent vibration and slippage during operation.
– Use a heat-resistant and anti-static work surface to ensure component stability in a high-temperature environment.
2.Exhaust System:
– Install an exhaust system to remove smoke and harmful gases generated during soldering and desoldering processes from the workspace.
– Keep the exhaust duct unobstructed and regularly clean the filters.
3.Electrical Connections:
– Ensure that the power cord and plug of the infrared desoldering station are intact, avoiding damaged or exposed wires.
– Use power sockets with overload and leakage protection to prevent electrical faults.
III. Equipment Calibration and Inspection
1.Temperature Control System Calibration:
– Before each work session, check and calibrate the temperature control system, including the infrared temperature sensor and controller, to ensure precise and stable heating.
2.Heating Element Inspection:
– Inspect the condition of infrared bulbs or other heating elements to ensure they are not damaged or aged.
– Clean dust and impurities from the bulbs and reflectors to maintain emission efficiency.
3.Control Panel and Display:
– Ensure that the control panel and display are functioning properly, and the temperature and parameter readings are clear and accurate.
4.Emergency Stop Device:
– Check the functionality of the emergency stop button or device to ensure power can be quickly cut off in an emergency.
IV. Personal Protective Equipment and Safety Tips
1.Personal Protective Equipment:
– Operators should wear protective glasses or masks, gloves, and clothing to prevent harm from infrared radiation, splashes, and harmful gases.
2.Safety Tips:
– Post prominent safety warning signs in the workspace to remind operators to stay away from high temperatures and hazardous areas.
– Keep emergency exits clear and have emergency equipment like fire extinguishers ready.
V. Conclusion
Setting up and configuring the working environment for the infrared desoldering station is crucial to ensure its efficient and safe operation. Choosing a suitable workspace, configuring a stable workbench, providing a good exhaust system and electrical protection, calibrating the equipment, and inspecting heating elements and control panels can significantly improve the efficiency and accuracy of the desoldering station. Ensuring that technicians wear personal protective equipment and follow safety tips can further enhance the safety of the work process.