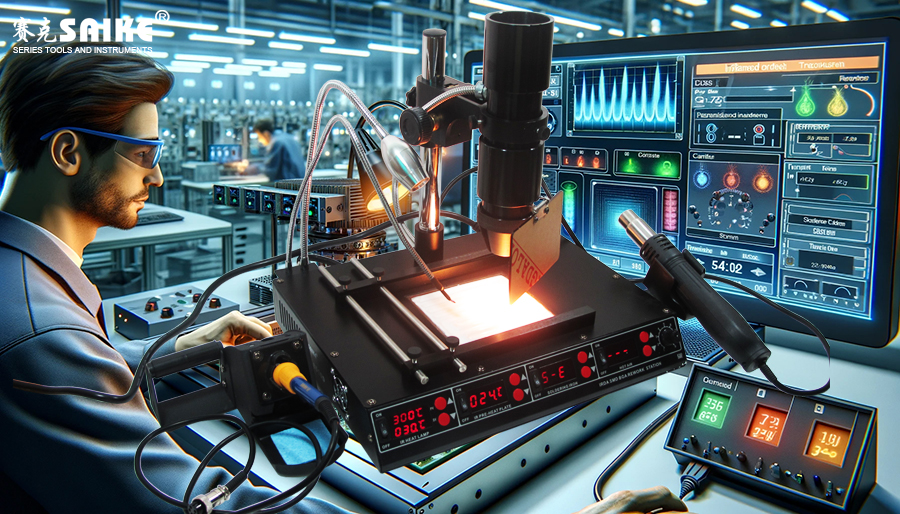
SK-YJ000HWXCHT-KP 100011 Precise Control of Infrared Heating Process
Infrared heating technology is widely used in precision desoldering and soldering operations in electronic manufacturing and repair. It provides fast and uniform heating, suitable for complex, multi-layer circuit boards and sensitive electronic components. To ensure the effectiveness and safety of the heating process, precise control is crucial. This article will introduce the methods and techniques for precise control during the infrared heating process.
I. The Importance of Precise Control
1.Reducing Thermal Stress:
– Precise control of infrared heating can avoid problems caused by temperature changes, such as circuit board warping, interlayer separation, and component damage.
2.Ensuring Uniform Heating:
– For high-density electronic components, precise control ensures uniform heating, prevents local overheating or cold spots at solder joints, and guarantees soldering quality.
3.Energy Conservation:
– Through reasonable temperature control strategies, heating time and power consumption can be effectively reduced, saving energy and production costs.
II. Methods of Precise Control
1.Temperature Sensing and Monitoring:
– Infrared Sensor: The infrared sensor can non-contactly measure the temperature of the target area, reflecting the actual temperature of solder joints and components in real-time.
– Thermocouple Sensor: The thermocouple sensor converts temperature differences into electrical signals. It has the advantages of fast response and high sensitivity, suitable for high-precision temperature monitoring.
2.PID Temperature Control System:
– The PID (Proportional-Integral-Derivative) control system automatically adjusts the output power of the infrared emitter by calculating the difference between the current temperature and the target temperature to maintain a stable heating temperature.
– By adjusting the PID parameters, the temperature response speed can be optimized, reducing temperature fluctuations and overshoot phenomena.
3.Multi-zone Heating Control:
– The multi-zone control system divides the entire work area into multiple independent heating zones. The temperature of each zone is independently adjusted based on sensor data.
– This strategy is suitable for complex circuit boards and high-density components, ensuring uniform heating in each zone.
4.Preset and Programming of Temperature Profiles:
– Different soldering and desoldering tasks require specific temperature profiles, including preheating, constant temperature, and cooling stages.
– Advanced infrared heating systems can preset multiple temperature profiles, and users can also achieve customized temperature control through programming.
III. Adjustment Techniques for Precise Control
1.Initial Temperature Setting:
– Set a reasonable initial temperature based on the material properties of the electronic components and circuit boards to avoid component damage due to excessively high or low temperatures during the initial heating stage.
2.Adjustment of Heating Rate:
– Adjust the heating rate to adapt to the heat resistance of different components and circuit boards, preventing thermal stress caused by rapid heating.
3.Real-time Monitoring and Feedback:
– Use temperature sensors to monitor temperature changes in real-time and provide timely feedback to the control system to prevent overshoot and temperature fluctuations.
4.Regular Calibration and Maintenance:
– Regularly calibrate temperature sensors and control systems to ensure their accuracy, and timely maintain and replace damaged components.
IV. Summary
Precise control of the infrared heating process is crucial to ensure the quality of soldering and desoldering of electronic components. Through the rational use of temperature sensing technology, PID control systems, multi-zone heating strategies, and temperature profile programming, precise management of the heating process can be achieved. Operators should adjust the temperature and heating rate according to specific tasks, monitor and provide feedback on temperature data in real-time to ensure a stable and efficient heating process. Regular calibration and maintenance of equipment are also essential to maintain precise control.