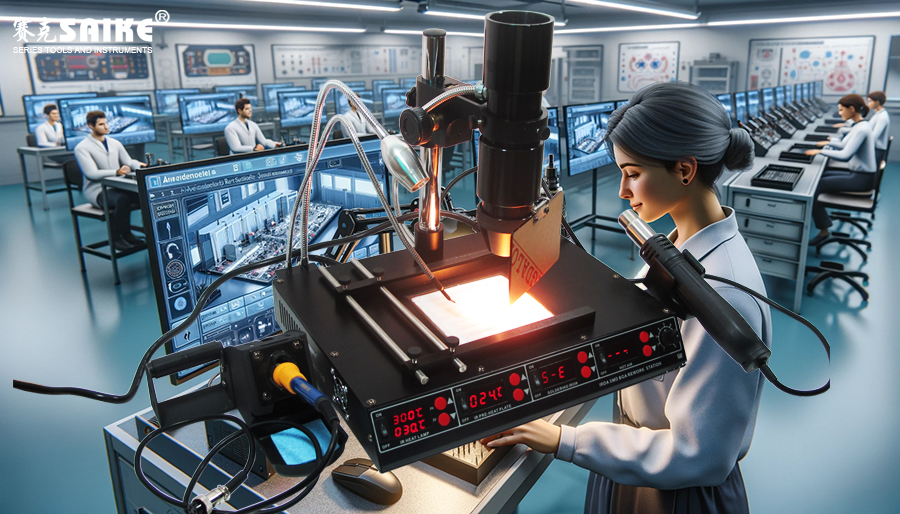
SK-YJ000HWXCHT-KP 100024
The infrared desoldering station holds irreplaceable importance in the maintenance and production of high-density electronic components and multilayer circuit boards. However, to ensure optimal results in practical operations, technicians should undergo thorough operational practice in a simulated environment. Simulated operations provide a non-destructive, low-risk setting that aids technicians in mastering the use of infrared desoldering stations and understanding their characteristics. This article delves into the strategies and significance of practicing infrared desoldering station operations in a simulated environment.
I. The Importance of Simulated Operational Practice
1.Familiarity with Equipment Characteristics:
– Through simulated practice, operators can understand the temperature control, heating area, optical positioning system, and other features of the infrared desoldering station, ensuring operational accuracy in practical use.
2.Optimal Temperature Control:
– By setting different temperature profiles during simulated operations, operators can observe heating rates and solder joint temperatures, determining the best parameters for preheating, soldering, and cooling.
3.Enhanced Operational Skills:
– Repeated practice in precise positioning, heating power adjustment, and temperature monitoring can improve the operator’s reaction speed and technical skills.
4.Risk Reduction:
– Simulated operations allow for the identification and correction of potential operational errors, thereby reducing the risk of soldering failures and component damage in actual production.
II. Operational Strategies in a Simulated Environment
1.Preheating and Heating Area Practice:
– Objective: Accurately locate the heating area to ensure the infrared emitter’s heating range aligns with the target solder joints.
– Practice Content: Utilize the optical positioning system to locate and mark target solder joints; adjust the angle of the infrared emitter and reflector position for uniform radiation coverage of the target area.
2.Temperature Profile Adjustment Practice:
– Objective: Program and fine-tune temperature profiles for different solder joints and circuit boards, ensuring stable temperatures during soldering and desoldering.
– Practice Content: Set temperature and time parameters for preheating, soldering, and cooling phases; simulate temperature profiles for various components and solders; monitor solder joint temperature changes.
3.Solder Joint Monitoring and Feedback Practice:
– Objective: Master real-time monitoring of solder joint temperatures and heating power adjustments to maintain stable temperature profiles.
– Practice Content: Use infrared or thermocouple sensors to monitor simulated solder joint temperatures in real-time; adjust heating power promptly and record temperature data.
4.Thermal Insulation and Shielding Measures Practice:
– Objective: Utilize thermal insulation materials or shields to protect sensitive components and non-target areas, ensuring heating is focused on target solder joints.
– Practice Content: Apply thermal insulation to adjacent solder joints or components in the simulated environment; use shields or reflectors to concentrate heating on the target area, preventing damage to other components.
5.Solder Joint Cleanup and Quality Inspection:
– Objective: Practice cleaning solder joints after desoldering and inspecting their integrity and connection quality.
– Practice Content: Simulate desoldering, clean solder residue from solder joints, and use inspection tools like microscopes to check the solder joint surface and connection integrity.
III. Conclusion
Operational practice of the infrared desoldering station in a simulated environment is crucial for operators to master equipment characteristics and operational techniques. Through preheating and heating area practice, temperature profile adjustment, solder joint monitoring and feedback, thermal insulation and shielding measures, and solder joint cleanup and quality inspection, technicians can repeatedly practice in a risk-free environment. This enhances their operational skills, optimizes temperature control, and improves thermal insulation measures, thereby reducing failure rates in actual production and ensuring soldering and desoldering quality.