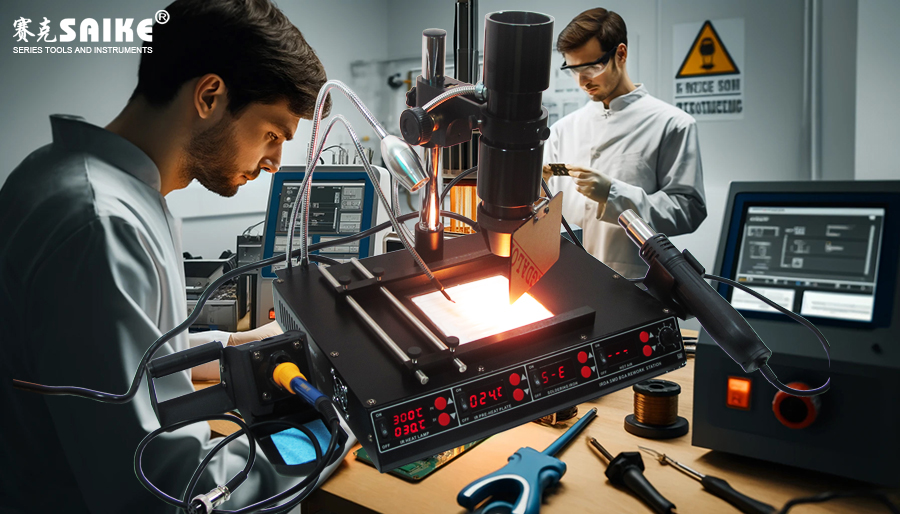
SK-YJ000HWXCHT-KP 100012
The infrared desoldering station is a crucial tool in the field of electronic repair and manufacturing, especially suitable for desoldering and soldering operations of high-density packaging and complex circuit boards. To ensure efficiency and avoid problems caused by incorrect operations, it is essential to master the operating skills of the infrared desoldering station and know the solutions to common problems. This article will introduce operating skills in detail and provide troubleshooting methods for common issues.
I. Operating Skills of Infrared Desoldering Station
1.Preset Temperature and Time:
– Set appropriate temperature and heating time based on the type of component to be desoldered and the material of the circuit board to avoid overheating or insufficient heating.
– Generally, the preheating temperature should be set between 100°C and 150°C, and the soldering and desoldering temperature should be higher than the melting point of the solder but appropriately lower than the heat resistance limit of the component.
2.Programming and Application of Temperature Profiles:
– Set suitable temperature profiles for complex components and multilayer circuit boards to ensure stability and consistency during preheating, heating, and cooling processes.
– Use system-provided or user-defined temperature profile programs to maintain gradual temperature changes and avoid thermal shock.
3.Positioning the Heating Area:
– Determine the specific location of components and solder joints, and use optical systems or other marking methods to accurately locate the heating area to ensure that heating does not deviate from the target.
– For large components or circuit boards, ensure that the infrared radiation evenly covers the target area.
4.Temperature Monitoring and Feedback:
– Use infrared sensors or thermocouple sensors to monitor the temperature of solder joints and components in real-time, and adjust the heating power based on feedback.
– Ensure that the temperature remains within the preset range to avoid temperature fluctuations or overheating.
5.Appropriate Cooling and Post-processing:
– Allow the circuit board to cool naturally after the heating process to avoid thermal stress caused by rapid cooling.
– Check the integrity of solder joints and circuit boards, and perform secondary soldering or repair soldering if necessary.
II. Solutions to Common Problems
1.Uneven Heating:
– Causes: Damaged heating elements, deviation of the infrared emitter position, or failure of the temperature sensor.
– Solutions:
– Check and replace aging or damaged heating elements.
– Calibrate the angle and position of the infrared emitter to ensure even coverage of the solder joint area.
– Test the accuracy of the temperature sensor and calibrate or replace it.
2.Overheating or Insufficient Heating:
– Causes: Inaccurate temperature control system, improper sensor placement, or incorrect temperature profile settings.
– Solutions:
– Calibrate the temperature control system to ensure accurate feedback data.
– Adjust the position of the temperature sensor to obtain reliable real-time temperature data.
– Check and reset the temperature profile parameters.
3.Damage to Solder Joints or Component Falling Off:
– Causes: Excessively high temperature settings, too fast heating speed, or poor component quality.
– Solutions:
– Lower the temperature setting and gradually increase the temperature to reduce thermal shock.
– Ensure a reasonable temperature profile to avoid sudden temperature increases.
– Check the quality and soldering strength of components and replace them if necessary.
4.Temperature Display Does Not Match Reality:
– Causes: Damaged temperature sensor, malfunctioning control panel, or data transmission issues.
– Solutions:
– Test and calibrate the temperature sensor to ensure accurate readings.
– Check the hardware and software of the control panel to ensure stable data transmission.
– Update the control system software or firmware.
III. Summary
Mastering the operating skills and solutions to common problems of the infrared desoldering station is crucial for improving soldering quality and production efficiency. By reasonably presetting temperature and time, programming temperature profiles, locating heating areas, and real-time monitoring and feedback, the accuracy and safety of the infrared desoldering station in electronic repair and manufacturing can be ensured. Meanwhile, troubleshooting methods for common problems also help maintain efficient equipment operation and avoid production losses due to equipment failures or operational errors.