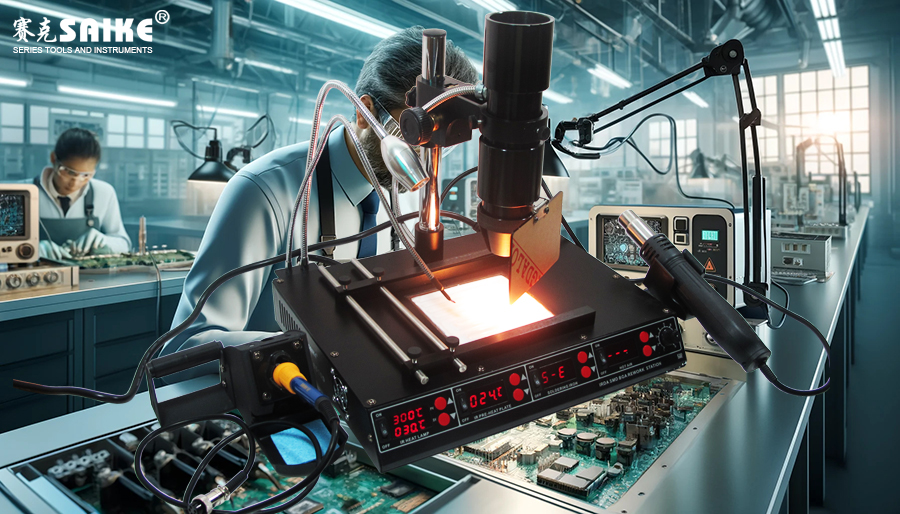
SK-YJ000HWXCHT-KP 100022
The infrared rework station serves as a precise and uniform heating tool for electronic soldering and desoldering, exhibiting unique advantages in the maintenance of high-density and complex packaged electronic components. However, in practical applications, the integration of the infrared rework station with other soldering technologies can produce synergistic effects, enhancing overall soldering quality and efficiency. This article delves into the integration strategies and synergistic effects of combining the infrared rework station with various soldering techniques.
I. Infrared Rework Station and Hot Air Desoldering Technology
1.Hot Air Desoldering Technology:
– Hot air desoldering melts solder by blowing high-temperature air directly onto solder joints or circuit boards using a hot air gun or blower.
2.Integration and Synergistic Effects:
– Uniform Preheating and Heating: The infrared rework station can uniformly preheat the circuit board, reducing thermal shock and solder joint delamination caused by direct hot air heating. Subsequent local heating with hot air ensures the complete melting of solder around the components.
– High-Density Solder Joint Processing: Infrared is suitable for heating larger areas, while hot air allows flexible adjustment of nozzle size, focusing on high-density solder joints.
II. Infrared Rework Station and Laser Soldering Technology
1.Laser Soldering Technology:
– Laser soldering utilizes a focused laser beam for high-energy, non-contact heating of solder joints, achieving extremely high soldering precision.
2.Integration and Synergistic Effects:
– Preheating and Precise Heating: The infrared rework station preheats the circuit board, reducing thermal shock from direct laser heating. The laser beam then precisely heats specific solder joints, ensuring component and solder joint integrity.
– Composite Material Soldering: Infrared is ideal for uniform preheating of composite materials, while the laser melts the solder joints, facilitating stable soldering between complex materials.
III. Infrared Rework Station and Resistance Soldering Technology
1.Resistance Soldering Technology:
– Resistance soldering generates heat by passing current directly through the solder joints or components, commonly used for connecting metal parts.
2.Integration and Synergistic Effects:
– Preheating and Rapid Heating: The infrared rework station uniformly preheats the circuit board or components, preventing current surges during soldering. Resistance soldering then rapidly heats the solder joints, achieving stable and secure connections.
– Multi-layer Circuit Boards: Infrared is suitable for uniform heating of multi-layer boards, while resistance soldering facilitates quick connections between different conductive layers.
IV. Infrared Rework Station and Wave Soldering Technology
1.Wave Soldering Technology:
– Wave soldering involves passing a circuit board over a wave of molten solder, ensuring adequate contact between the solder joints and the solder for proper soldering.
2.Integration and Synergistic Effects:
– Preheating and Melting Soldering: The infrared rework station preheats the circuit board to an optimal temperature range for wave soldering, reducing warping and delamination due to temperature differences.
– Solder Joint Integrity: Wave soldering is ideal for soldering large areas with multiple solder joints, while infrared can be used for post-soldering repairs and quality inspections.
V. Conclusion
By integrating the infrared rework station with other soldering technologies, their respective strengths can be fully utilized, achieving synergistic effects during the soldering and desoldering processes. The uniform preheating and precise heating capabilities of infrared complement hot air, laser, resistance, and wave soldering techniques, enhancing soldering quality and efficiency. Technicians should strategically combine these soldering technologies based on the structural characteristics of different electronic components and circuit boards to achieve diverse synergistic applications.