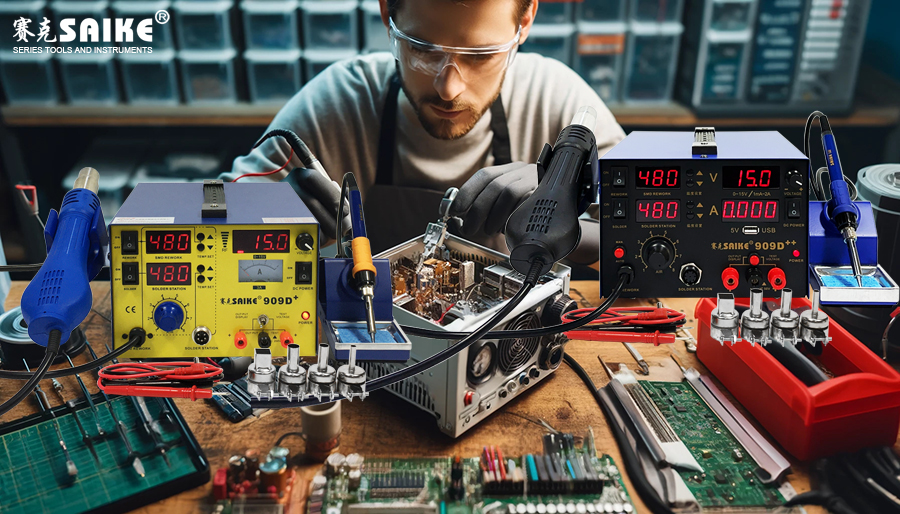
SK-YJ000RFSHY-KP 100018
The hot air rework station plays a crucial role in electronic repair and manufacturing. To ensure its efficient and stable operation over the long term, regular inspection and maintenance of its internal components are essential. This article provides a detailed introduction to the inspection and maintenance methods of the internal components of a hot air rework station.
I. Introduction to Major Internal Components
The primary internal components of a hot air rework station include:
1.Heating Element: Converts electrical energy into heat energy to heat the air.
2.Fan: Provides airflow to blow the heated air towards the work area.
3.Temperature Controller: Regulates and monitors the output temperature to ensure precise heating.
4.Power Module: Supplies the electrical energy required for the equipment’s operation.
5.Sensor: Detects parameters such as temperature and airflow, and feeds them back to the controller for adjustment.
II. Inspection and Maintenance Steps
1.Safety Preparations
– Power Off: Ensure that the hot air rework station is powered off and the power plug is disconnected before inspection and maintenance.
– Equipment Cooling: Wait for the equipment to cool completely to avoid burns.
2.Exterior Inspection
– Shell Inspection: Check the equipment shell for cracks, damage, or other obvious issues.
– Surface Cleaning: Clean the shell surface with a dry or lint-free cloth to remove dust and dirt.
3.Internal Component Inspection
– Heating Element Inspection
– Visual Inspection: Disassemble the equipment shell and check the heating element’s surface for obvious damage such as burning or breakage.
– Resistance Measurement: Use a multimeter to measure the resistance value of the heating element, ensuring it falls within the normal range. Replace it promptly if abnormal.
– Fan Inspection
– Fan Cleaning: Use a small brush to clean the fan blades and airways, removing dust and debris.
– Operation Test: Test the fan’s operation with power on, ensuring smooth and noise-free operation. Check the bearing lubrication or replace the fan if there is stuttering or noise.
– Temperature Controller Inspection
– Connection Check: Inspect the connecting wires between the temperature controller, heating element, and sensor for firmness, looseness, or breaks.
– Calibration Test: Use a thermometer to test the accuracy of the temperature controller’s readings and calibrate if necessary.
– Power Module Inspection
– Voltage Measurement: Use a multimeter to measure the output voltage of the power module, ensuring it stabilizes within the equipment’s required range.
– Connection Check: Inspect the connecting wires between the power module and other components for looseness, corrosion, or other issues.
– Sensor Inspection
– Visual Inspection: Check the sensor’s appearance for obvious damage or looseness.
– Functional Test: After powering on, check if the sensor’s feedback data is accurate and stable. Replace or repair if abnormal.
4.Regular Maintenance
– Cleaning and Maintenance
– Regular Cleaning: Perform monthly cleaning of the equipment shell and internals to ensure no dust or debris accumulation.
– Fan Lubrication: Apply lubricating oil to the fan bearings every 3 to 6 months to maintain smooth fan operation.
– Replacement of Wear Parts
– Regular Replacement: Replace wear parts such as heating elements and sensors every 6 to 12 months based on usage frequency and environment, ensuring stable equipment operation.
Equipment Calibration: Perform comprehensive equipment calibration, including the temperature controller and sensors, every 6 months to ensure measurement and control accuracy.
5.Records and Feedback
– Maintenance Records: Keep detailed records of each inspection and maintenance activity, identified issues, and their resolutions for future tracking and improvement.
– Feedback and Improvement: Provide timely feedback to equipment manufacturers or technical support based on issues identified during inspection and maintenance, seeking professional advice and improvement measures.
III. Conclusion
Regular inspection and maintenance of the internal components of a hot air rework station are crucial to ensuring its efficient and stable long-term operation. Through detailed exterior inspection, internal component inspection, and regular maintenance, equipment failures can be effectively prevented, work efficiency can be improved, and equipment lifespan can be extended. It is hoped that the methods provided in this article will assist electronic repair personnel in better maintaining and using hot air rework stations, ensuring safe and reliable completion of various tasks.