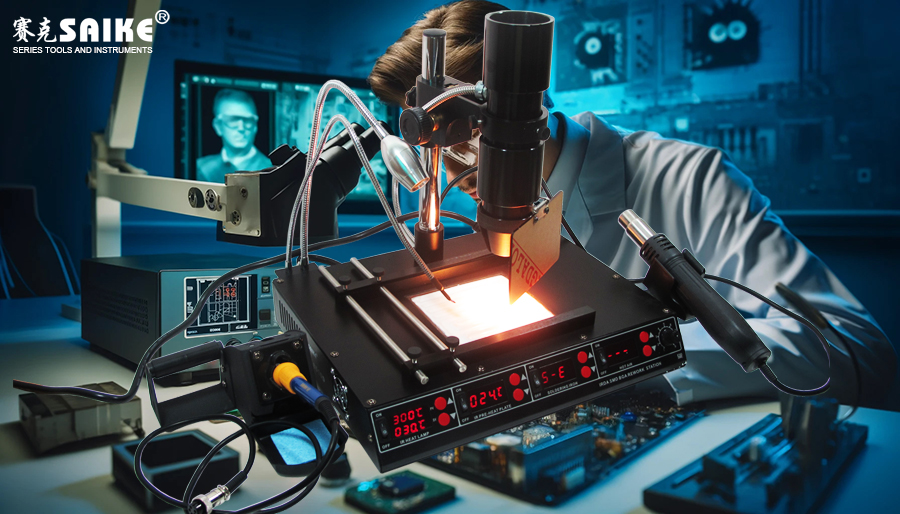
SK-YJ000HWXCHT-KP 100021
As a precision electronic maintenance tool, the infrared desoldering station is widely used in the maintenance and manufacturing of complex electronic equipment due to its precise heating capability and temperature control. It can efficiently handle electronic components with high density, multilayer, and complex packaging, providing unique advantages in maintenance across various industrial fields. This article will explore the innovative applications of infrared desoldering stations in complex equipment maintenance and elaborate on how this technology ensures efficient and high-quality maintenance.
I. Technical Advantages of Infrared Desoldering Station
1.Non-contact heating:
– Infrared directly transfers heat through non-contact heating, avoiding mechanical stress and errors and reducing damage to sensitive electronic components.
2.Multi-zone temperature control:
– The infrared desoldering station enables independent heating control for multiple zones, allowing precise heating of each area on a high-density circuit board.
3.Preset temperature profiles:
– By programming preset temperature profiles for preheating, heating, and cooling, the heating process can be optimized to ensure the soldering or desoldering quality of components.
4.Real-time temperature monitoring:
– The infrared desoldering station is equipped with temperature sensors and a feedback system that can monitor the temperature of solder joints and circuit boards in real time, adjusting heating power to maintain temperature stability.
II. Innovative Applications in Complex Equipment Maintenance
1.High-density multilayer circuit boards:
– High-density multilayer circuit boards are widely used in computers, communication equipment, and consumer electronics. Due to poor thermal conductivity and thermal stress easily leading to delamination, the multi-zone heating and precise temperature control of the infrared desoldering station ensure uniform heating of each layer, preventing thermal damage.
2.Precision micro-components:
– In micro-devices such as mobile phones, tablets, and camera modules, the solder joints of components are very small and easily damaged. The infrared desoldering station, through real-time monitoring by infrared sensors and an optical positioning system, can accurately locate solder joints and maintain an appropriate temperature profile to ensure the assembly and disassembly of micro-components.
3.High-power electronic components:
– High-power electronic components, such as power management ICs and processor chips, usually require high-temperature and durable soldering quality. During the preheating and desoldering processes of these components, the infrared desoldering station can customize temperature profiles based on the characteristics of the solder joints and the melting point of the solder to ensure soldering quality and durability.
4.BGA and QFN packages:
– The solder joints of high-density packages such as BGA and QFN are hidden under the components and require uniform heating for lossless assembly and disassembly. The infrared desoldering station can achieve zoned heating, ensuring uniform heating and melting of solder joints for successful assembly and disassembly of BGA and QFN packages.
5.Maintenance of large electronic equipment:
– In large equipment such as servers, data centers, and industrial control systems, the circuit board size is larger and the structure is more complex. The infrared desoldering station can provide a wide heating area and flexible fixtures to accommodate circuit boards and solder joints of different sizes.
III. Operation Suggestions and Maintenance
1.Temperature profile adjustment:
– In different types of complex equipment maintenance, the temperature profile should be adjusted based on the number of circuit board layers, component types, and solder melting points.
2.Optical positioning and shielding:
– Use an optical positioning system to ensure accurate heating areas and provide thermal insulation or shielding for adjacent sensitive components.
3.Real-time monitoring and feedback:
– Use temperature sensors to monitor solder joint temperatures in real time and adjust heating power to maintain a stable temperature profile.
4.Maintenance and calibration:
– Regularly clean the infrared emitter and reflection system, and calibrate the temperature control system and sensors to ensure efficient and stable operation of the infrared desoldering station.
IV. Summary
The infrared desoldering station, with its technical advantages such as non-contact heating, multi-zone temperature control, and real-time monitoring, has unique strengths in the maintenance of complex equipment such as high-density multilayer boards, precision micro-components, and high-power electronic components. By optimizing temperature profiles, accurately positioning heating areas, and real-time monitoring of solder joint temperatures, efficient and high-quality complex equipment maintenance can be ensured. Regular maintenance and calibration of the equipment can further improve the performance and stability of the infrared desoldering station.