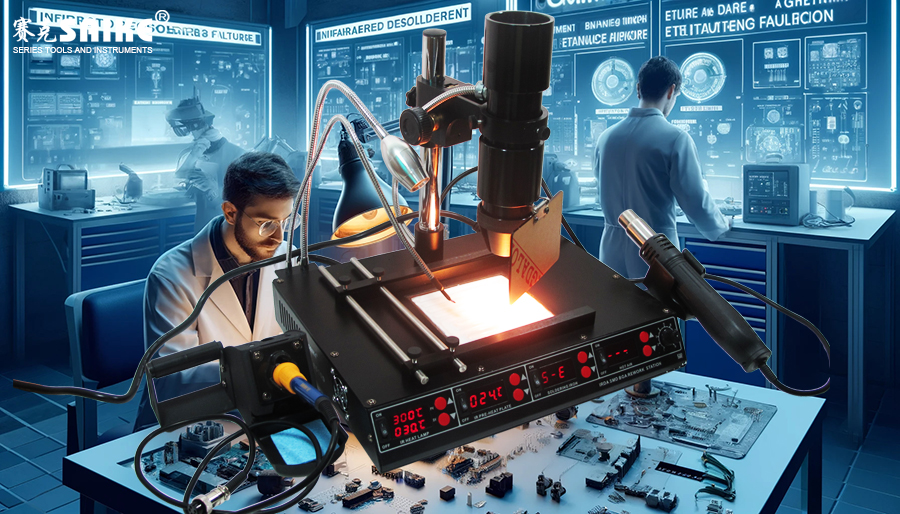
SK-YJ000HWXCHT-KP 100016
Infrared desoldering stations are crucial tools in electronic manufacturing and repair, efficiently handling high-density and complex electronic components. However, improper operation or equipment malfunctions can lead to suboptimal soldering quality and even damage electronic components. This article will delve into the common operating errors and equipment failures of infrared desoldering stations, aiding technicians in timely identifying and rectifying issues.
I. Common Operating Errors
1.Incorrect Temperature Settings:
– Too High: Excessively high temperatures can cause component damage, board warping, or delamination.
– Too Low: Insufficient temperatures prevent solder from fully melting or result in weak solder joints, leading to cold or dry joints.
– Solution: Reasonably set preheating, soldering, and cooling temperatures based on the melting point of the solder and the heat resistance of the components.
2.Faulty Temperature Profiles:
– Rapid Heating: Quick temperature rises can cause thermal shock to components or weak solder joints.
– Rapid Cooling: Fast cooling can create thermal stress, leading to cracked solder joints or damaged components.
– Solution: Program a reasonable temperature profile, ensuring smooth transitions during preheating, soldering, and cooling phases.
3.Imprecise Heating Area Targeting:
– Missing the Target: If the heating area doesn’t accurately cover the solder joints, it can lead to soldering or desoldering failures, potentially damaging adjacent components.
– Excessive Heat Spread: A large heating area can harm nearby sensitive components.
– Solution: Use an optical system for precise targeting and adjust the focal length and angle of the infrared emitter.
4.Inappropriate Workbench Setup:
– Unstable Board Fixation: If the circuit board isn’t securely fixed, it may move or warp during operation.
– Unsuitable Fixturing: Using the wrong material for fixtures can cause static electricity or lack of heat resistance.
– Solution: Choose appropriate fixtures and a heat-resistant workbench to ensure board stability throughout the process.
II. Equipment Failures and Troubleshooting Methods
1.Infrared Emitter Malfunctions:
– Lamp Aging or Damage: Infrared lamps have a limited lifespan and may show signs of aging, breakage, or damage.
– Reduced Output Power: Issues with the lamp or power supply can lead to decreased emitter power, hindering effective solder joint heating.
– Troubleshooting:
– Inspect the physical condition of the infrared lamp for breaks or burn marks.
– Measure the lamp’s resistance to ensure it’s within normal range.
– Replace damaged lamps or adjust the power supply output.
2.Temperature Control System Failures:
– Sensor Malfunction: Temperature sensor calibration errors or damage can lead to incorrect data in the temperature control system.
– Control Panel Issues: Faulty buttons, displays, or software on the control panel can prevent proper system operation.
– Troubleshooting:
– Check the sensor’s physical condition and electrical connections for data transmission integrity.
– Test the control panel’s buttons and display for responsiveness.
– Restart or upgrade the control panel’s firmware.
3.Electrical Faults:
– Power Supply Issues: Damaged power cords or plugs can prevent proper device powering or cause power interruptions.
– Internal Circuit Problems: Issues within internal wiring or circuit boards can lead to abnormal device startup or limited functionality.
– Troubleshooting:
– Inspect the physical condition of power cords and plugs for breaks or corrosion.
– Open the device and examine internal circuit boards and wiring for visible damage.
– Test the resistance and voltage of key circuits to ensure stable electrical connections.
III. Conclusion
Recognizing common operating errors and equipment failures of infrared desoldering stations significantly improves the efficiency and quality of electronic repairs and manufacturing. By properly setting temperatures and temperature profiles, precisely targeting heating areas, and maintaining a stable workbench, operational errors can be avoided. Regular inspections of the infrared emitter, temperature control system, and electrical circuitry can help timely detect and resolve equipment failures, ensuring the desoldering station remains in optimal condition.