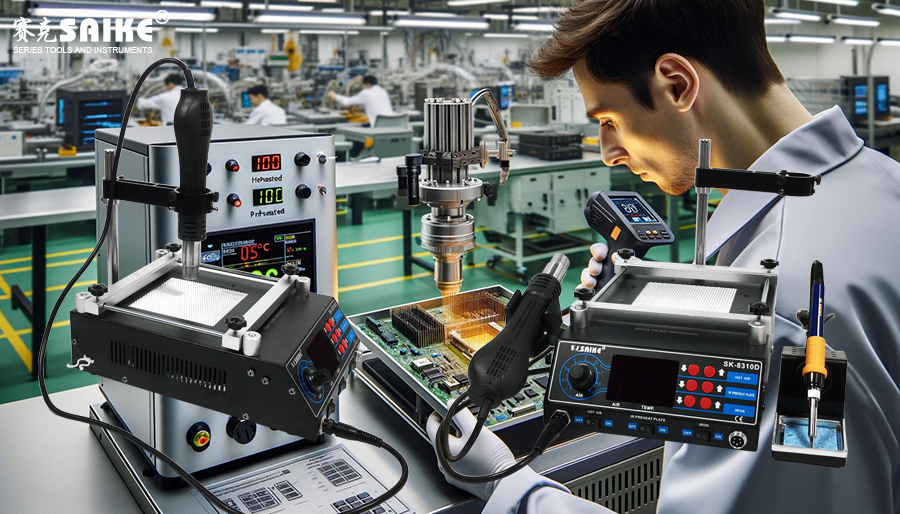
SK-YJ000YRT-KP 100019
In modern electronic manufacturing and maintenance, the preheating station has become a crucial piece of equipment to ensure soldering quality and component safety when dealing with high-density and complex circuit boards. These types of circuit boards often feature multilayer layouts and numerous miniature components, requiring precise control over heat distribution during the soldering process. This article explores how to effectively handle high-density and complex circuit boards using a preheating station to optimize the soldering process and reduce failure rates.
I. Challenges of High-Density and Complex Circuit Boards
1.Uneven heat distribution:
– High-density circuit boards, with their compact component layouts, can easily lead to uneven heat distribution. This may cause some areas to overheat while others fail to reach the appropriate soldering temperature during the soldering process.
2.Thermal stress issues:
– Complex circuit boards often contain various materials with different coefficients of thermal expansion, which can easily generate thermal stress during the heating process, resulting in warping or interlayer separation of the circuit board.
3.Protection of sensitive components:
– Micro and sensitive electronic components (such as BGAs, microprocessors, etc.) cannot withstand high temperatures, and overheating may damage these components.
II. Optimal Use Strategies for Preheating Stations
1.Precise control of preheating temperature:
– Set the preheating temperature according to the specific materials and component types of the circuit board, usually between 100°C and 150°C, to ensure no thermal damage to any components.
– Use a preheating station with temperature control capabilities to achieve precise temperature regulation and stability.
2.Application of uniform heating technology:
– Choose a preheating station capable of providing uniform heating, such as using multi-zone heating technology or infrared heating, to ensure even heating of all parts of the circuit board.
– Consider using localized heating technology for gentle heating of specific sensitive areas.
3.Step-by-step heating program:
– Set the preheating station for gradual heating to avoid thermal shock. Programmatically control the temperature to gradually increase, allowing the circuit board to slowly preheat to the target temperature.
III. Preheating Operation Steps
1.Preparation before preheating:
– Clean the circuit board to remove dust or impurities that may affect heat conduction.
– Check the preheating station settings to ensure the temperature sensor is correctly positioned and the temperature settings meet the requirements.
2.Monitoring the preheating process:
– Use a thermal imaging camera or temperature sensor to monitor the temperature distribution of the circuit board in real-time, ensuring uniform heating and no overheated areas.
3.Post-processing and evaluation:
– Allow the circuit board to cool naturally after preheating to avoid thermal stress caused by rapid cooling.
– Inspect the circuit board’s readiness for soldering, ensuring no warping or other visible damage.
IV. Summary
Handling high-density and complex circuit boards with a preheating station poses a technical challenge that requires precise control over the heating process to protect sensitive components and ensure soldering quality. By implementing the aforementioned strategies and steps, the processing quality of the circuit board can be significantly improved, reducing defects during the soldering process and enhancing the reliability and performance of the final product. Proper use of the preheating station not only improves production efficiency but also ensures that high standards and quality requirements are met in the electronic manufacturing process.