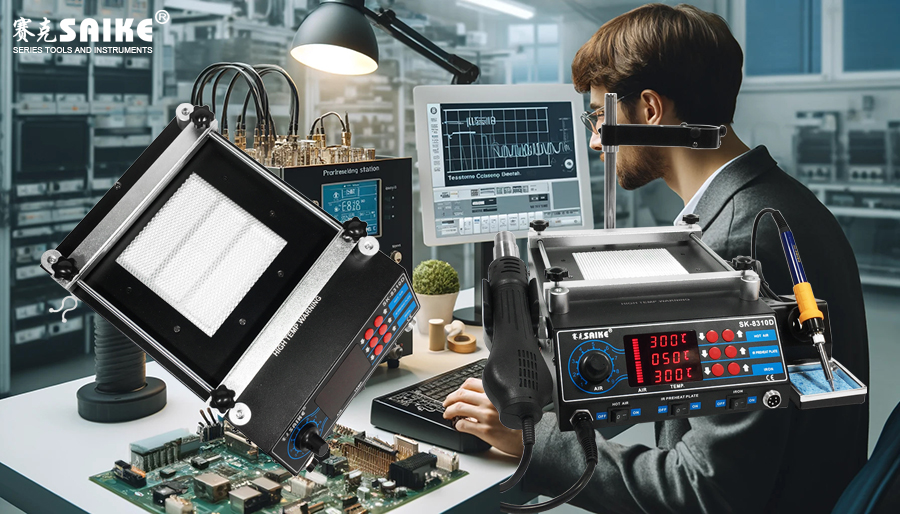
SK-YJ000YRT-KP 100005
In the field of electronic manufacturing and repair, the preheating station serves as a crucial tool for preheating circuit boards or other components in advance, optimizing the soldering process and preventing damage caused by thermal stress. The control system and temperature settings constitute the core functionalities of the preheating station, ensuring precise and effective operation. This article delves into the significance and implementation methods of the control system and temperature settings for the preheating station.
I. The Importance of the Preheating Station Control System
The control system is the brain of the preheating station. It’s responsible for receiving user input commands, controlling the heating elements, and ensuring stable operation according to set parameters. An efficient control system offers several key advantages:
1.Precise Temperature Control: Ensures the preheating station can reach and maintain the set temperature, crucial for sensitive electronic components as both excessively high and low temperatures can cause damage.
2.User-Friendly Interface: An intuitive control interface simplifies operations, allowing users to easily set and adjust temperatures, timers, and other related parameters.
3.Flexible Program Settings: Advanced control systems support multiple preset programs tailored to different work needs, enhancing the versatility and flexibility of the equipment.
4.Fault Diagnosis and Safety Features: Modern control systems monitor equipment status, detect and report faults promptly, and implement safety measures like automatic power-off to prevent accidents.
II. Temperature Settings for the Preheating Station
Proper temperature settings are essential for achieving high-quality preheating results. Here are key factors to consider when setting the temperature:
1.Material Properties of Components: Different circuit board materials and components have varying sensitivities to heat. For instance, thick multilayer boards might require higher preheating temperatures, while thin single-layer boards or boards with sensitive components need lower temperatures.
2.Melting Point of Solder: The preheating temperature should be set according to the type of solder used, typically lower than the solder’s melting point to avoid premature melting. It’s usually set between 50% to 70% of the solder’s melting point.
3.Heating Rate: The heating rate should be moderate. Rapid heating may cause thermal unevenness, while slow heating reduces efficiency. The control system should adjust the heating speed based on different needs.
4.Temperature Uniformity: Ensuring temperature uniformity across the entire preheating area is crucial, especially for large or complex circuit boards. Multiple temperature sensors might be needed for monitoring and adjustment.
III. Implementation Methods
1.Setting Temperature Parameters: Before starting work, set appropriate temperatures and heating times based on the circuit board material, component types, and solder specifications.
2.Using Temperature Curves: For complex heating requirements, programmable temperature curves can be set. The preheating station adjusts the temperature step by step according to the preset curve, achieving optimal heating effects.
3.Real-Time Temperature Monitoring: Use temperature sensors to monitor the preheating process in real-time, ensuring the set temperature is accurately applied and making timely adjustments for any deviations.
IV. Conclusion
The control system and temperature settings of the preheating station are crucial for ensuring the quality and efficiency of soldering work. By utilizing advanced control technology and precise temperature management, the performance of the preheating station can be significantly improved, guaranteeing efficient and safe electronic manufacturing and repair work. Proper configuration and operation of the preheating station can not only extend the lifespan of electronic components but also enhance the overall production line efficiency.