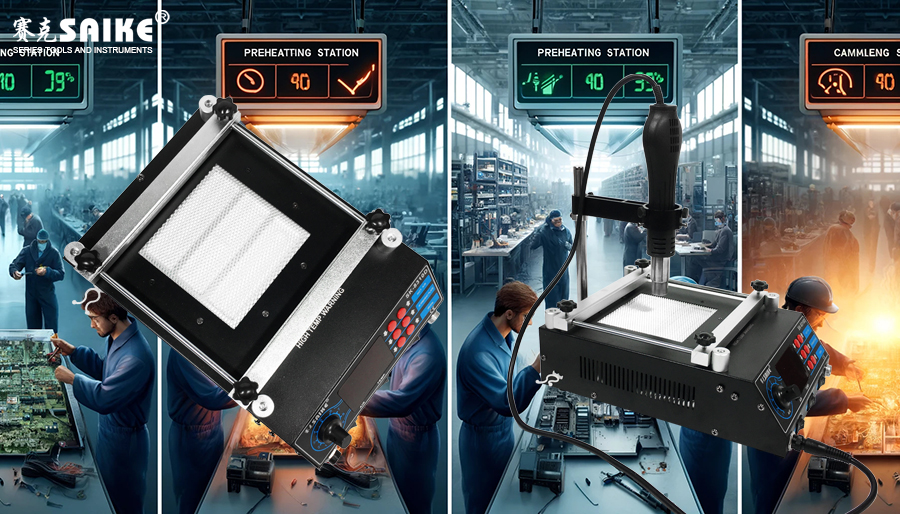
SK-YJ000YRT-KP 100022
The preheating station, as a crucial piece of equipment in the field of electronic manufacturing and maintenance, plays a vital role in improving soldering quality and reducing production defects. This article analyzes the impact of preheating station usage on the soldering process of circuit boards through two practical cases – one successful and one unsuccessful – thereby providing insights into optimizing the use of preheating stations.
I. Success Case: Improvement in the Soldering of Automotive Electronic Control Units
1.Background: In a company specializing in automotive electronics production, the production department faced a high failure rate during the soldering process of Electronic Control Units (ECU). Initial analysis indicated that the failures were primarily due to cold solder joints and thermal stress-induced warping of the circuit board.
2.Challenge: The ECU boards are complex, containing multilayered, high-density wiring and sensitive microelectronic components. The traditional soldering process, which involved direct exposure to high temperatures in a reflow oven without preheating, caused severe thermal shock to the boards and components.
3.Solution: Introduction of a preheating station as part of the soldering process. The preheating station was set to gradually heat the circuit board to 150°C through a temperature profile lasting approximately 10 minutes before entering the reflow oven.
4.Result: The preheating process significantly reduced thermal stress during soldering, drastically decreasing board warpage and poor solder joints. The first-pass yield increased from 75% to over 95%, significantly improving production efficiency and product quality.
II. Failure Case: Soldering Mistakes in Communication Equipment
1.Background: A communication equipment manufacturer decided to adopt a preheating station to improve soldering quality when introducing a new high-frequency communication module production line.
2.Challenge: Due to improper operation and setting errors, the temperature of the preheating station was set too high, reaching 200°C, far exceeding the heat resistance limit of the circuit board and components.
3.Incorrect Operations:
– The temperature controller was set incorrectly, not adjusted according to the heat resistance of the components.
– Operators lacked sufficient understanding of the temperature impact of the preheating station and did not perform appropriate temperature monitoring.
4.Result: The excessively high preheating temperature damaged sensitive components, especially some delicate BGA chips, which developed severe soldering defects. This led to the scrapping of a large number of produced modules due to functional failures, resulting in high costs and time losses.
III. Summary and Insights
Insights from the Success Case:
– The appropriate use of a preheating station can significantly improve soldering quality and production efficiency.
– Precise control of preheating conditions is necessary, adjusting the preheating temperature and time based on the specific characteristics of the circuit board and components.
Insights from the Failure Case:
– Although beneficial, the temperature and time control of the preheating station must be strict to avoid damage to the circuit board and sensitive components.
– Operators need to undergo adequate training to understand the correct operation of the equipment and the thermal sensitivity of the components.
Through the analysis of these cases, it is evident that the correct use of the preheating station is crucial to ensuring the quality of the soldering process. At the same time, attention should be paid to the proper setup of the equipment and operator training to avoid production losses due to operational errors.