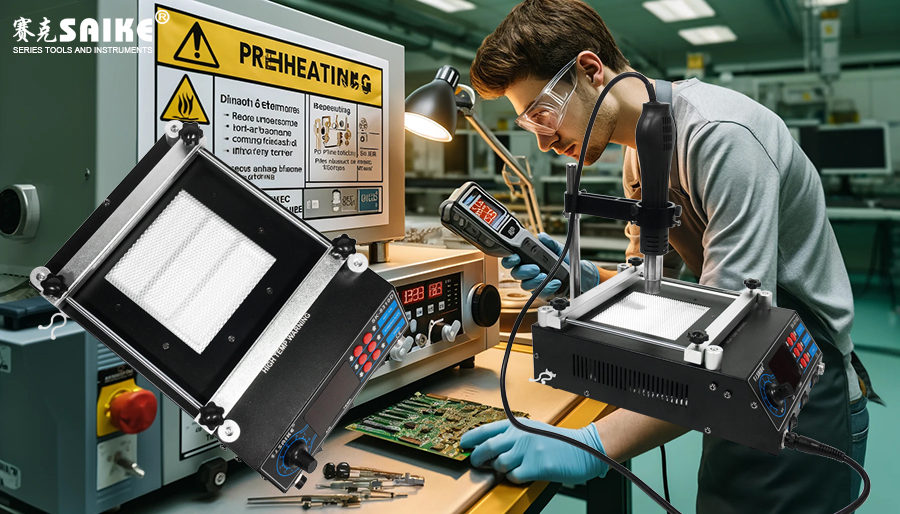
SK-YJ000YRT-KP 100012
Preheating stations are commonly used in electronic manufacturing and repair to preheat circuit boards, reducing thermal stress and optimizing the soldering process. However, incorrect operation can lead to equipment damage, decreased product quality, and even safety accidents. This article explores common mistakes in preheating station operation and provides corresponding preventive measures to help technicians improve efficiency and safety.
I. Common Operational Mistakes
1.Incorrect Temperature Settings:
– Setting the temperature too high can cause the circuit board to overheat, damaging sensitive electronic components or causing board warping.
– Setting the temperature too low may result in insufficient solder melting, affecting the quality of soldering joints.
2.Uneven Heating:
– If the temperature distribution of the preheating station is uneven, it may cause local overheating or inadequate heating of the board, thus affecting the overall soldering quality.
3.Ignoring Preheating Time:
– Ignoring the preheating time of the equipment and starting the soldering operation directly may result in poor soldering due to insufficient temperature.
4.Neglecting Equipment Maintenance and Cleaning:
– If the preheating station is not regularly maintained and cleaned, accumulated dust and dirt may affect its performance and even cause equipment failure.
II. Preventive Measures
1.Setting the Correct Temperature:
– Carefully read the operation manual before using the equipment to understand the temperature requirements for different materials and components.
– Use temperature testing instruments (such as infrared thermometers) to regularly verify the actual working temperature of the preheating station to ensure accuracy.
2.Ensuring Even Heating:
– Regularly check if the heating elements are working properly to ensure even heat distribution.
– For large or irregularly shaped circuit boards, adjust the board position or use multi-point temperature monitoring to ensure even heating.
3.Following Preheating Time Regulations:
– Set a reasonable preheating time based on the manufacturer’s guidance and practical experience to ensure that the board reaches a suitable temperature for soldering.
– Use a timer to control the preheating time to prevent overheating or inadequate heating.
4.Regular Maintenance and Cleaning:
– Establish a maintenance schedule for regular inspection and cleaning of the preheating station.
– Check and clean the dust and dirt around the heating elements to ensure a smooth ventilation system.
III. Operational Training and Safety Awareness
1.Operator Training:
– Regularly train operators to update their knowledge about equipment operation, safety regulations, and troubleshooting.
– Reinforce the importance of temperature control and time management during the preheating process.
2.Enhancing Safety Awareness:
– Post operation guides and safety warnings in prominent positions in the work area.
– Cultivate the habit of taking immediate action when encountering abnormalities, such as stopping the machine for inspection or requesting technical support.
IV. Summary
Preheating stations are essential tools for improving soldering quality, but correct operation is crucial. By following the best practices mentioned above, common operational mistakes can be effectively avoided, extending equipment lifespan, improving product quality, and ensuring operator safety. Regular maintenance, accurate temperature control, and reasonable operational training are the keys to ensuring efficient and safe operation of the preheating station.