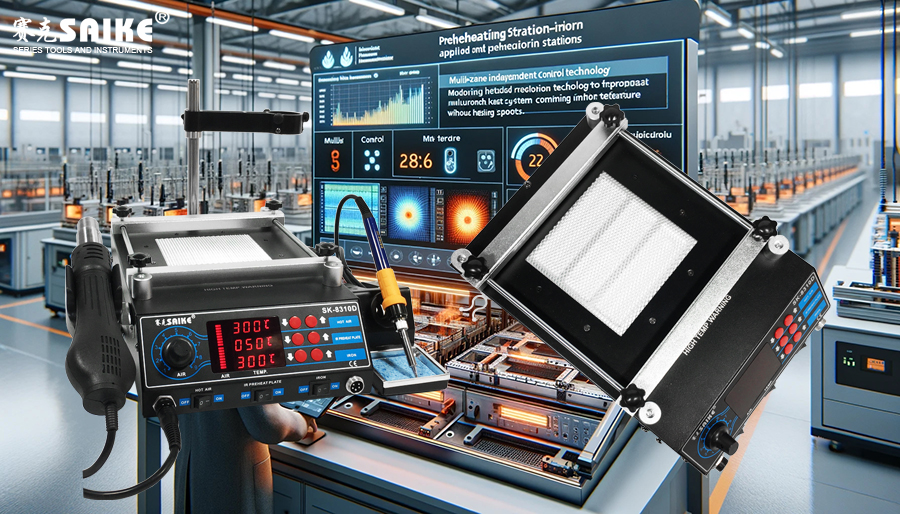
SK-YJ000YRT-KP 100020
Preheating stations play a crucial role in the field of electronic manufacturing and repair, ensuring that circuit boards are uniformly heated before soldering, thereby improving soldering quality and efficiency. With technological advancements, the design and functionality of preheating stations are continuously innovating to meet higher production efficiency and environmental requirements. This article explores how the latest technological innovations are being applied in preheating stations and how these innovations are changing the current state of the electronics manufacturing industry.
I. Technological Innovations in Preheating Stations
1.Multi-Zone Independent Control Technology:
– Modern preheating stations employ multi-zone independent control technology, allowing individual control and adjustment of different areas on the circuit board. This technology enables different zones to be set at varying temperatures and heating rates, particularly suitable for complex or multilayer circuit board preheating needs.
2.Optimization of Infrared Heating Technology:
– Infrared heating technology is widely used in preheating stations due to its speed and energy efficiency. The latest infrared heating systems adopt a modular design for more precise heat distribution control, reducing hot and cold spots and ensuring a more uniform heating effect.
3.Integrated Temperature Feedback System:
– Advanced preheating stations now integrate real-time temperature feedback systems, such as thermal imaging technology, allowing operators to monitor the temperature distribution of the circuit board in real-time. This technology automatically adjusts heating parameters to ensure uniformity and precision in the heating process.
4.Intelligent Control and Interfaces:
– Preheating stations’ intelligent control systems include touchscreen interfaces and programmable logic controllers (PLCs), supporting user-defined programs and greatly improving operational convenience and flexibility. Additionally, some preheating stations can seamlessly integrate with other production equipment or computer systems through network interfaces, enabling automated production lines.
5.Energy-Saving and Environmental Technologies:
– New preheating stations utilize energy-saving technologies like automatic standby modes and low-power heating elements to reduce energy consumption and operating costs. Materials and manufacturing processes also trend towards environmental friendliness, complying with RoHS and REACH regulations.
II. Impact of Technological Innovations
1.Increased Production Efficiency:
– With advanced temperature control and feedback systems, preheating stations achieve desired temperatures faster and maintain temperature stability, reducing soldering defects and rework rates.
2.Reduced Production Costs:
– Energy-saving technologies and improved heating efficiency decrease energy consumption, while efficient heating reduces production cycle times, further lowering production costs.
3.Enhanced Product Quality:
– Precise temperature control and uniform heating improve soldering quality, reduce circuit board damage due to thermal stress, and ultimately enhance product reliability and lifespan.
4.Environmental Impact:
– Eco-friendly design and manufacturing processes minimize environmental impacts, helping manufacturing companies comply with increasingly stringent environmental regulations.
III. Conclusion
Technological innovations in preheating stations not only enhance equipment performance and efficiency but also propel the entire electronics manufacturing industry towards a more efficient and environmentally friendly direction. The introduction of these technologies has made preheating stations an indispensable part of modern electronics production lines, helping businesses stay ahead in a competitive market. As technology continues to evolve, the applications and functionalities of preheating stations will expand, bringing more possibilities and opportunities to the electronics manufacturing industry.