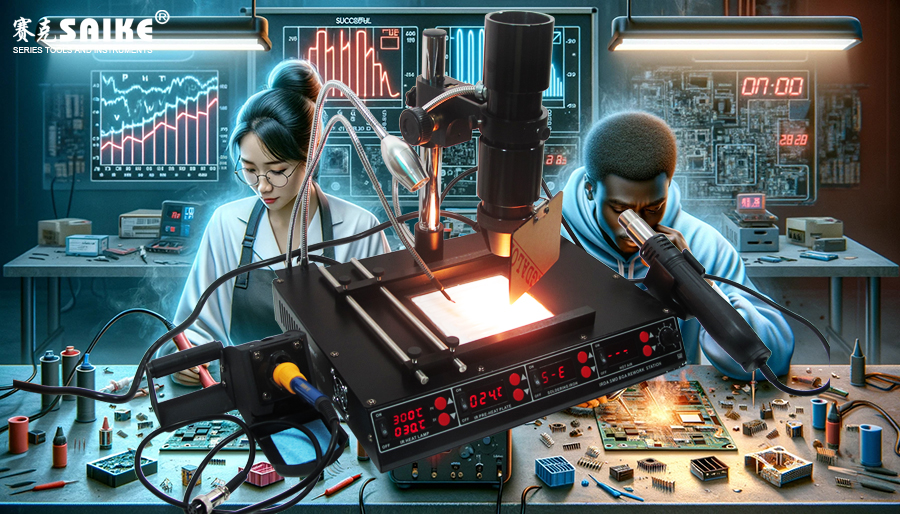
SK-YJ000HWXCHT-KP 100023
Infrared desoldering technology is widely used in the maintenance and production of high-density electronic components and complex circuit boards due to its precise heating control, non-contact operation, and multi-zone heating advantages. However, the desoldering process is affected by multiple factors such as temperature control, heating uniformity, and operational skills, which can lead to different outcomes of success or failure. In this article, we will analyze successful and failed infrared desoldering cases, summarize key experiences and lessons, and help technicians improve their operational skills to ensure soldering quality.
I. Successful Infrared Desoldering Cases
1.Case 1: Desoldering of High-Density BGA Packaged Components
Background: On a multi-layer circuit board with high-density BGA packaging, the solder joints are hidden underneath the components. The heating process needs to ensure uniform melting of the solder without damaging adjacent components.
Operational Steps:
– Temperature Setting: Set the preheating and soldering temperatures based on the melting point of the solder in the BGA package and the heat resistance of the circuit board. The preheating stage is set at 120°C, and the soldering temperature is maintained at 230°C for 5 minutes.
– Multi-Zone Heating: Use the multi-zone heating function of the infrared desoldering station to heat the BGA area in different zones, ensuring uniform heating.
– Real-Time Monitoring and Adjustment: Utilize an infrared sensor to monitor the temperature of the solder joints in real-time and adjust the heating power to maintain a stable temperature curve.
Results and Summary:
– The solder joints melted uniformly, and the BGA component was successfully desoldered without damaging the circuit board or adjacent components.
– Experience Summary: Multi-zone heating and real-time temperature monitoring are crucial for successful desoldering of high-density BGA packaged components.
2.Case 2: Desoldering of Multi-Layer Circuit Boards
Background: Multi-layer circuit boards are prone to delamination due to thermal stress during the soldering process. Infrared desoldering needs to avoid damage to different conductive layers.
Operational Steps:
– Temperature Curve Setting: Program a reasonable temperature curve, with the preheating temperature controlled at 100°C and gradually increasing to the soldering temperature of 240°C.
– Optical Positioning: Utilize an optical positioning system to accurately locate the solder joints and adjust the angle and position of the infrared emitter.
– Preheating and Heating: First, uniformly preheat the entire circuit board, then gradually heat the target solder joints, maintaining a stable temperature for 5 minutes.
Results and Summary:
– The target component was successfully desoldered, and the circuit board showed no warping or delamination issues with intact solder joints.
– Experience Summary: Temperature control during the preheating stage and optical positioning ensure precise heating of the solder joints, avoiding thermal stress damage to the multi-layer circuit board.
II. Failed Infrared Desoldering Cases
1.Case 1: Damaged QFN Packaged Components
Background: QFN packages have pins arranged around the perimeter of the component, making them prone to thermal stress and warping during the heating process.
Operational Steps:
– Incorrect Temperature Curve Setting: The preheating temperature was set too low, and the temperature rose too quickly during the heating stage, resulting in uneven heating of the solder joints and pins.
– Lack of Monitoring: There was no real-time temperature monitoring, and the solder joint temperature was too high without timely adjustment of the heating power.
– Inaccurate Optical Positioning: The infrared emitter was inaccurately positioned, causing the heating area to deviate from the target solder joints.
Results and Summary:
– The QFN packaged component experienced uneven heating, resulting in cold solder joints and leading to pin detachment and local warping of the circuit board.
– Lesson Summary: The heating stage should be slow and steady, with real-time monitoring of solder joint temperatures to adjust the power timely. Additionally, ensure accurate optical positioning.
2.Case 2: Damaged Flexible Circuit Boards
Background: Flexible circuit boards are prone to deformation due to thermal stress during the soldering process, requiring precise temperature control and heating time.
Operational Steps:
– Incorrect Temperature Setting: The preheating and soldering temperatures were set too high, exceeding the heat resistance limit of the circuit board.
– Insufficient Shielding: Lack of heat insulation measures resulted in heat damage to areas outside the heating zone on the circuit board.
Results and Summary:
– The flexible circuit board exhibited warping, uneven heating of solder joints, and solder residue, indicating a failed desoldering process.
– Lesson Summary: The set temperature should be controlled within the heat resistance range of the circuit board, with appropriate shielding of adjacent areas and stable fixation of the circuit board.
III. Summary
By analyzing successful and failed infrared desoldering cases, it becomes evident that multi-zone heating, temperature curve setting, and real-time monitoring are crucial for ensuring solder joint integrity and avoiding component damage. The failed cases demonstrate that incorrect temperature control, inaccurate optical positioning, and lack of protective measures are the main reasons for desoldering failures. In practical operations, technicians should reasonably adjust the temperature curve, monitor solder joint temperatures, and adopt precise positioning and heat insulation measures according to different components and circuit board types to improve the success rate of infrared desoldering.