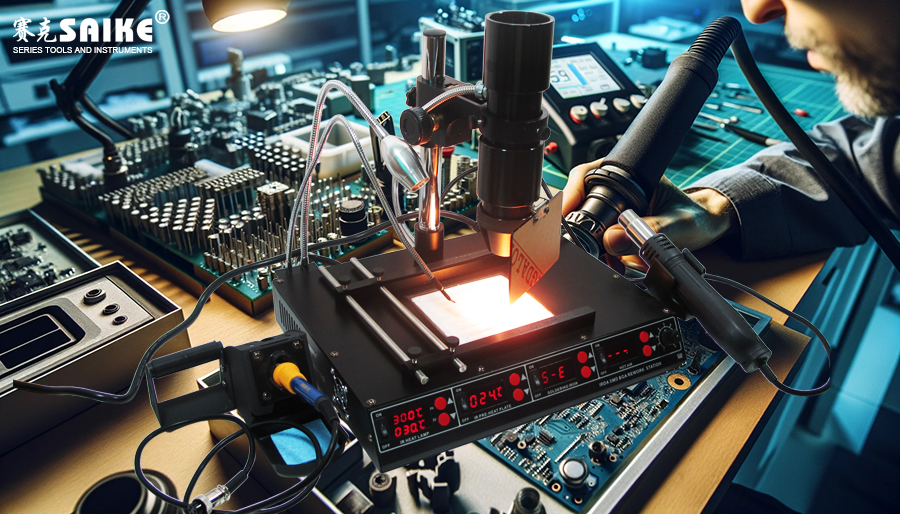
SK-YJ000HWXCHT-KP 100003
Infrared desoldering stations exhibit distinct advantages in the field of electronic manufacturing and repair, especially in the soldering and desoldering of high-density and sensitive electronic components. However, every technology has its limitations. Understanding the strengths and weaknesses of infrared desoldering stations helps technicians make informed decisions in various electronic repair tasks.
Advantages of Infrared Desoldering Stations
1.Precise Heating:
– Infrared desoldering stations utilize infrared radiation to focus heat on the target solder joint or component. The precise targeting of infrared energy minimizes interference with surrounding components.
2.Uniform Heating:
– The even distribution of infrared energy ensures that the target solder joints and components are heated uniformly, avoiding issues like localized overheating or uneven solder flow.
3.Temperature Control:
– These stations are equipped with advanced temperature control systems, utilizing infrared sensors or thermocouples for real-time temperature monitoring. This ensures temperature accuracy and stability, following a preset profile.
4.Reduced Thermal Stress:
– Precise and uniform heating minimizes thermal stress during soldering and desoldering, protecting multi-layer circuit boards from issues like warping or delamination.
5.Versatility:
– Infrared desoldering stations are suitable for components of various sizes and types, particularly high-density surface mount devices like BGA, QFN, and CSP.
6.Non-contact Operation:
– Infrared heating offers a non-contact method, reducing mechanical errors and risks.
Limitations of Infrared Desoldering Stations
1.Limited Radiation Range:
– Infrared heating has a restricted effective radiation range, making it unsuitable for heating large circuit boards uniformly. It’s more appropriate for localized or precise heating tasks.
2.Material Absorptivity:
– Different materials absorb infrared differently. Some component surfaces may reflect infrared energy, reducing heating efficiency or creating hot spots.
3.Temperature Calibration:
– Infrared temperature sensors require precise calibration for accurate temperature control. Miscalibration can lead to temperature deviations.
4.Higher Cost:
– Compared to hot air desoldering equipment, infrared stations tend to be more expensive, potentially exceeding the budget of smaller repair businesses.
5.Technical Expertise Required:
– Operating an infrared desoldering station demands a higher level of technical skill. Operators need to master temperature settings and heating durations to avoid thermal damage.
6.Complex Packaging Challenges:
– For components with intricate packaging, achieving uniform infrared detection and heating can be challenging, adding complexity to the operation.
Conclusion
Infrared desoldering stations offer significant advantages in desoldering high-density and sensitive components, providing precise and uniform heating with minimal component damage. However, factors like cost, technical expertise required, and material absorptivity need to be considered when selecting and operating these stations. Overall, they are well-suited for high-precision repairs and quality production tasks, provided the operators possess the necessary skills.