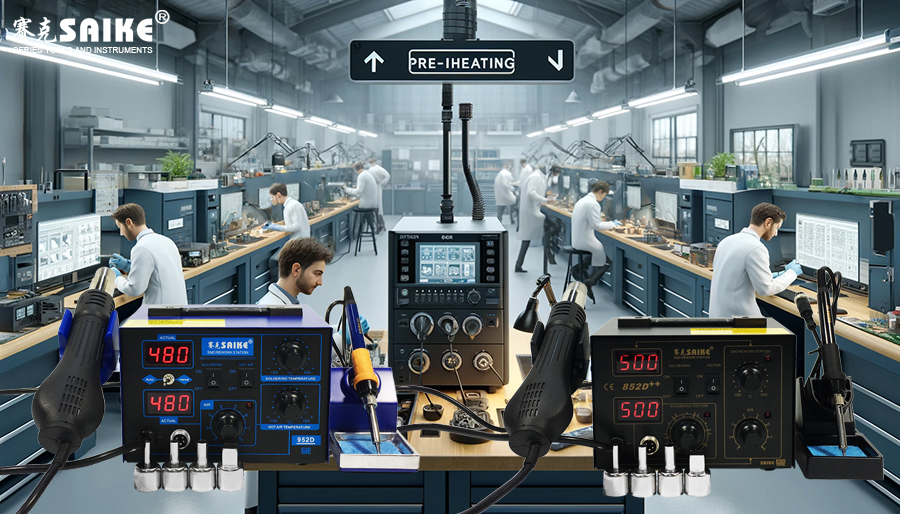
SK-YJ000RFCHT-KP 100030
The hot air desoldering station is an indispensable tool in electronic repair work, demonstrating unique efficiency and precision especially when dealing with complex desoldering tasks. However, regardless of how efficient the equipment is, the correct operational strategies and workflow optimization are crucial to enhancing work efficiency and quality. This article will introduce in detail how to improve the desoldering efficiency of the hot air desoldering station through strategic adjustments and workflow optimization.
I. Strategies for Efficiency Improvement
1.Proper Equipment Settings
– Optimization of Temperature and Air Speed: Ensure that the temperature and air speed settings of the hot air desoldering station are suitable for the current work task. Using excessively high or low temperatures can affect desoldering efficiency. An excessively high air speed may cause heat to disperse too widely, while a too-low air speed may result in excessively long heating times.
– Nozzle Selection: Choose the appropriate nozzle based on the size and shape of the component being desoldered. Different nozzles can provide different shapes and sizes of hot air flows, adapting to various levels of complexity in desoldering needs.
2.Application of Preheating Technology
– Utilizing the low-temperature preheating function of a preheating station or hot air desoldering station to preheat the entire circuit board can reduce thermal stress during local heating, preventing circuit board warping and damage to sensitive components.
3.Precise Time Management
– Precisely control the heating time to avoid overheating. Overheating not only wastes time but may also damage the circuit board or components.
II. Workflow Optimization
1.Organization of the Work Area
– Reasonable Layout: The work area should be clearly organized, with commonly used tools and materials arranged in an orderly manner for easy access. This reduces the time spent searching for tools and materials, improving work efficiency.
– Cleaning and Maintenance: Keep the work area clean and tidy, regularly cleaning the hot air desoldering station and related equipment to maintain their optimal performance.
2.Establishment of Standard Operating Procedures (SOP)
– Develop and implement standard operating procedures, providing detailed step-by-step guides and parameter settings for common desoldering tasks. This helps reduce operational errors and ensures that every desoldering process is carried out with maximum efficiency.
3.Skill Training and Practice
– Regularly train technicians, especially when introducing new equipment or technologies. Encourage technicians to practice and familiarize themselves with the best practices and techniques for various desoldering tasks.
III. Case Application
– Desoldering of Multi-layer Circuit Boards: Preheating technology is particularly important when desoldering multi-layer circuit boards. First, use a preheating station to preheat the board to a temperature close to the desoldering temperature, and then quickly complete the desoldering work using a hot air desoldering station. This method not only improves desoldering speed but also significantly reduces board damage caused by uneven heating.
IV. Summary
Effective desoldering efficiency relies not only on high-quality equipment but also on thoughtful operational strategies and workflow optimization. By following the aforementioned strategies and optimization steps, the operational efficiency of the hot air desoldering station can be significantly improved, enhancing the overall quality of repair work. Providing technicians with proper training and resources is key to ensuring they can maximize the use of the hot air desoldering station.