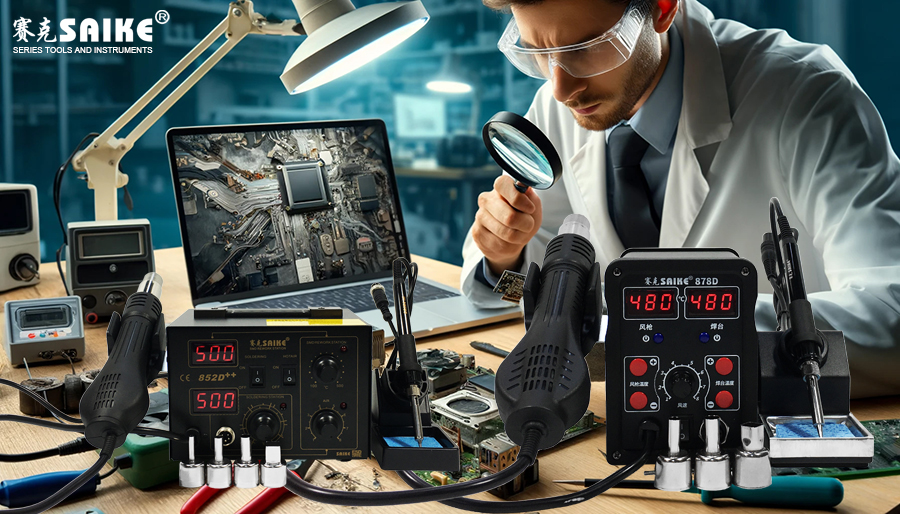
SK-YJ000RFCHT-KP 100034
The hot air rework station is a crucial tool in electronic repair, used for precise desoldering and soldering of complex electronic components. Mastering its use is essential, as improper operation can lead to severe equipment damage. By analyzing successful and failed cases, technicians can learn how to optimize operational processes and improve the success rate of desoldering. This article explores successful and failed cases of hot air rework stations in desoldering tasks, analyzes their causes, and summarizes relevant lessons.
I. Successful Case Analysis
Case Background: During a mobile phone repair, technicians successfully replaced a damaged micro USB charging port using a hot air rework station.
Operational Details:
1.Preparation: The technician first identified the damaged component on the phone’s motherboard and carefully cleaned the work area before operation.
2.Temperature and Air Speed Settings: The temperature of the hot air rework station was set to 280°C, and the air speed was set to medium to ensure adequate heating without damaging adjacent sensitive components.
3.Precise Operation: A small-diameter nozzle was used to precisely target the damaged USB port. The hot air evenly heated the solder joints around the port, causing the solder to melt quickly.
4.Component Removal and Replacement: The damaged port was gently removed using tweezers, and residual solder was cleaned. The new port was placed and re-soldered using the hot air rework station.
Success Factors:
– Precise temperature control avoided overheating.
– Using a suitable nozzle and appropriate air speed ensured even heating of the solder joints.
– A clean work environment and standardized operational procedures reduced the risk of static electricity and contamination.
II. Failed Case Analysis
Case Background: While attempting to repair a laptop motherboard, a technician accidentally damaged a BGA chip using a hot air rework station.
Operational Details:
1.Improper Temperature Setting: The technician set the temperature of the hot air rework station too high (over 350°C), attempting to complete the desoldering work quickly.
2.Operational Process: The excessively high temperature caused excessive heating of the circuit board around the BGA chip, and the circuit board under the solder balls began to deform.
3.Solder Joint Damage: High temperatures also caused some solder balls to break, rendering the chip unusable.
Failure Reasons:
– Improper temperature control, well above the heat resistance limit of the chip and circuit board.
– Lack of understanding of the BGA chip desoldering process and failure to take necessary precautions such as gradual heating or using low-temperature solder.
III. Lessons and Improvements
1.Strict Control of Operating Parameters: Always set the temperature and air speed according to the specifications of the component and the manufacturer’s recommendations.
2.Enhanced Professional Training: Regular training on the use of hot air rework stations should be conducted to educate technicians on correct operational procedures, precautions, and how to handle common problems and unexpected situations.
3.Strengthened Quality Awareness: Foster a focus on detail and quality among technicians, avoiding hasty actions or sacrificing quality for speed.
4.Continuous Improvement and Reflection: Regularly review successful and failed cases, summarize lessons learned, and continuously optimize operational processes and technical proficiency.
IV. Conclusion
Through the analysis of successful and failed cases, technicians can gain a deeper understanding of the working principles and operational skills of hot air rework stations, avoid common mistakes, and continuously improve their skill levels in practice. With strict operational guidelines and continuous training, the success rate of desoldering tasks can be maximized, ensuring the maintenance quality and reliability of electronic equipment.