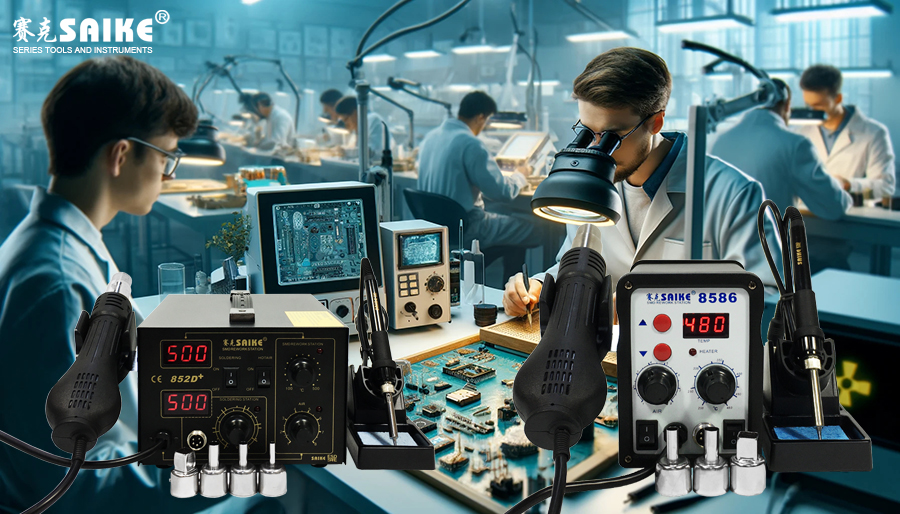
SK-YJ000RFCHT-KP 100032
As a critical equipment in electronic manufacturing and maintenance, the soldering quality of hot air rework station directly affects the performance and reliability of products. High-quality soldering not only ensures the normal operation of electronic devices but also extends the service life of products. Therefore, evaluating soldering quality and analyzing its reliability is an essential part of ensuring the reliability of electronic devices. This article will introduce the soldering quality assessment methods and reliability analysis skills of hot air rework stations in detail.
I. Soldering Quality Assessment Methods
1.Visual Inspection:
– Appearance Assessment: Observe the shape, size, and solder distribution of solder joints through a magnifying glass or microscope. Good solder joints should present a smooth, flawless cone shape, and the solder should evenly cover the pads and pins.
– Color and Luster: Check whether the color of the solder joints is uniform. The solder should exhibit a uniform metallic luster without signs of charring or graying.
2.Mechanical Testing:
– Tensile Test: Test the mechanical strength of solder joints using specialized tensile testing equipment to ensure they can withstand certain forces without falling off.
– Shear Test: Use shear testing instruments to measure the shear strength of solder joints to evaluate the mechanical stability of soldering.
3.Electrical Testing:
– Connectivity Test: Use a multimeter to detect the connectivity of solder joints, ensuring there is no cold soldering or false soldering.
– Insulation Test: Conduct a high-voltage insulation test on the soldered parts to check for short circuits or leakage.
4.X-ray Inspection:
– For solder joints that cannot be directly observed, such as BGA, use X-ray detection technology to evaluate the solder ball distribution and connectivity under the solder joints, promptly identifying issues such as voids or bridges.
II. Reliability Analysis Skills
1.Environmental Stress Testing:
– Temperature Cycling Test: Subject the soldered circuit board to alternating high and low temperature cycles to observe the performance of solder joints under temperature changes, assessing their long-term reliability.
– Vibration Test: Simulate vibration environments during transportation or use to check whether solder joints crack or fall off during vibration.
2.Accelerated Life Testing:
– Evaluate the aging speed and failure modes of soldered parts under accelerated environmental conditions (such as high temperature, high humidity, and chemically corrosive environments), thereby inferring the service life under normal conditions.
3.Statistical Analysis:
– Conduct statistical analysis on soldering failure rates to assess the overall reliability of the soldering process. By analyzing soldering failure data, optimize soldering parameters and processes to improve soldering quality.
4.Failure Mode and Effects Analysis (FMEA):
– Analyze possible failure modes during the soldering process and their impact on product functionality. Use systematic analysis methods to prevent potential soldering problems.
III. Summary
In conclusion, hot air rework stations play a crucial role in the manufacturing and maintenance of electronic products, and the soldering quality directly affects the overall reliability of the product. Through the aforementioned assessment methods and reliability analysis skills, technicians can more effectively control soldering quality, prevent soldering defects, and ensure the high performance and long life of electronic products. Continuous optimization of the soldering process and the application of advanced detection and analysis techniques are the keys to improving the efficiency and soldering quality of hot air rework stations.