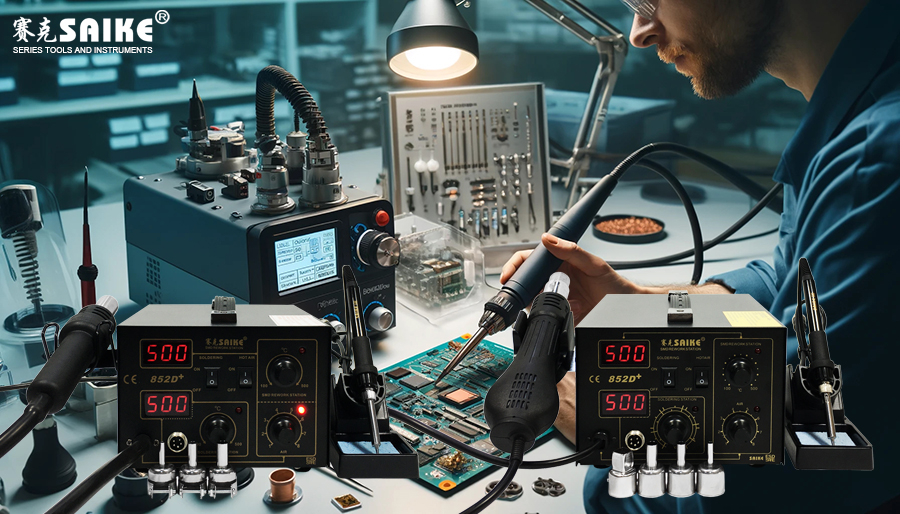
SK-YJ000RFCHT-KP 100017
The hot air rework station plays a crucial role in electronic repair and assembly work, and properly handling soldering joints of different materials is an essential part of achieving efficient and high-quality soldering. This article will detail how to use a hot air rework station for desoldering joints of different materials.
I. Understanding Solder Types
1.Lead-free solder:
– Lead-free solder typically requires higher temperatures to melt. The temperature setting on the hot air rework station should be higher than that for leaded solder, usually between 217°C and 249°C.
– Lead-free solder has a higher surface tension, so more precise temperature control and delicate operation are needed during desoldering to avoid damaging the solder joints.
2.Leaded solder:
– Leaded solder has a lower melting point, generally between 183°C and 190°C. Therefore, the temperature should be set slightly lower to reduce thermal damage to the circuit board.
– Leaded solder flows better when heated, making it relatively easier to handle.
II. Handling Strategies for Different Substrate Materials
1.Rigid substrates:
– For rigid FR-4 substrates, hot air desoldering should moderately control heating time and temperature to avoid overheating, which can cause substrate layer separation or pad lifting.
– Use a medium airflow speed to ensure uniform heat distribution without mechanically damaging the substrate.
2.Flexible substrates:
– Flexible substrates are more sensitive and fragile, so lower temperatures and more precise temperature control are required during desoldering.
– Use a lower airflow speed and a finer nozzle to reduce thermal stress on the thin film material.
III. Handling Special Material Solder Joints
1.Multilayer ceramic substrates:
– These substrates are very sensitive to thermal cycling, so precise temperature control is crucial to avoid cracks caused by thermal shock.
– Use gradual heating techniques, increasing the temperature step by step while monitoring temperature changes at each step.
2.High heat capacity metal substrates:
– Metal substrates conduct heat quickly, so a higher initial temperature may be required to reach the solder’s melting point.
– Continuously monitor the substrate temperature during heating to avoid local overheating.
IV. Handling Special Shaped Solder Joints
1.Large area solder joints:
– Large area solder joints require more uniform heat distribution. Use a larger nozzle to cover a wider area, which may require a longer heating time.
– Control the direction of hot air flow to ensure even heating of each section.
2.High-density assembly desoldering:
– For high-density assembled circuit boards, use a small nozzle to precisely control the direction of the hot air to avoid heating adjacent components.
– Precise temperature and airflow control are critical, and lower airflow speeds and temperatures may be required to prevent additional damage caused by thermal drift.
V. Conclusion
Correctly using a hot air rework station to handle soldering joints of different materials is crucial to ensure soldering quality and equipment safety. By precisely controlling temperature and airflow speed, selecting the appropriate nozzle, and considering the characteristics of the substrate and solder, the soldering and desoldering processes can be effectively optimized. Understanding and implementing the above strategies will help technicians improve operational efficiency, reduce failure rates, and extend equipment lifespan.