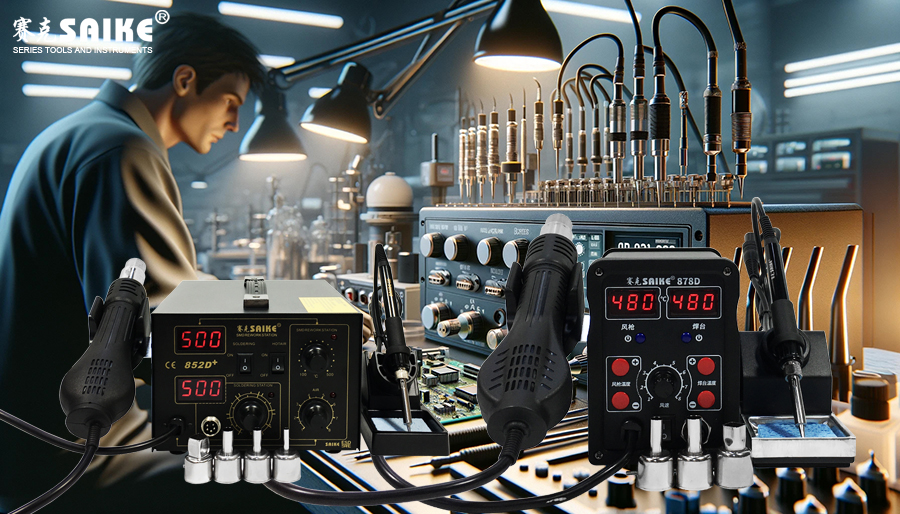
SK-YJ000RFCHT-KP 100014
The hot air rework station is a widely used tool in electronic repair and manufacturing, achieving efficient and precise soldering and desoldering through the accurate control of temperature and airflow speed. Correctly setting these two parameters is crucial to ensure the effectiveness of the operation and prevent component damage. This article will detail how to precisely set the temperature and airflow speed on a hot air rework station and how these settings affect soldering quality and safety.
I. The Importance of Temperature Settings
1.Appropriate Temperature Range:
– The temperature setting should be based on the melting point of the solder being used. Most lead-tin solders have a melting point between 183°C and 227°C, while lead-free solders typically require higher temperatures, ranging from 217°C to 250°C. The temperature should be set slightly above the melting point of the solder to ensure complete melting.
2.Preventing Overheating:
– Setting the temperature too high can damage the circuit board, especially for multilayer boards and small surface-mount devices (SMDs). Overheating can also cause solder joints to flow too quickly and excessively, affecting soldering quality.
3.Considering Environmental Factors:
– The temperature and humidity of the working environment can also affect the actual effect of hot air. When working in a cold environment, it may be necessary to slightly increase the set temperature.
II. Adjusting Airflow Speed
1.Choosing the Right Airflow Speed:
– Airflow speed is crucial for controlling the coverage and heating rate of the hot air. An excessively high airflow speed may cause solder splashing or uneven heating, while a too-low speed may result in slow heating, affecting work efficiency.
2.Adjusting Airflow Speed Based on Component Size:
– For large components or thicker circuit boards, the airflow speed can be appropriately increased to ensure uniform heat distribution. For small or sensitive components, the airflow speed should be reduced to prevent the components from being blown off the solder pads.
3.Direction and Distance of the Airflow:
– During operation, the nozzle should maintain a certain distance from the work surface, typically recommended to be between 2 and 5 centimeters. The angle and distance of the nozzle directly affect the effectiveness of the hot air and the quality of the solder joints.
III. Precise Control and Feedback Adjustment
1.Real-time Monitoring of Temperature and Airflow:
– Using equipment with temperature sensors can help monitor the temperature in real-time, ensuring stability throughout the process.
– Many high-end devices come with flow meters, allowing users to precisely adjust and monitor airflow speed.
2.Experience and Adjustment:
– The actual situation of soldering and desoldering may vary depending on component types and board differences. Operators should adjust settings based on experience to meet specific needs.
3.Using the Right Nozzle:
– The choice of nozzle also affects the effectiveness of temperature and airflow. Different shapes and sizes of nozzles are suitable for various applications, and selecting the right nozzle is another crucial factor in achieving precise control.
IV. Conclusion
Correctly setting and adjusting the temperature and airflow speed on a hot air rework station is fundamental to successful soldering operations. Precise settings not only affect the soldering results but also directly relate to operational safety and component protection. Through continuous practice, monitoring, and adjustment, operators can finely tune these settings to optimize the soldering and desoldering processes.