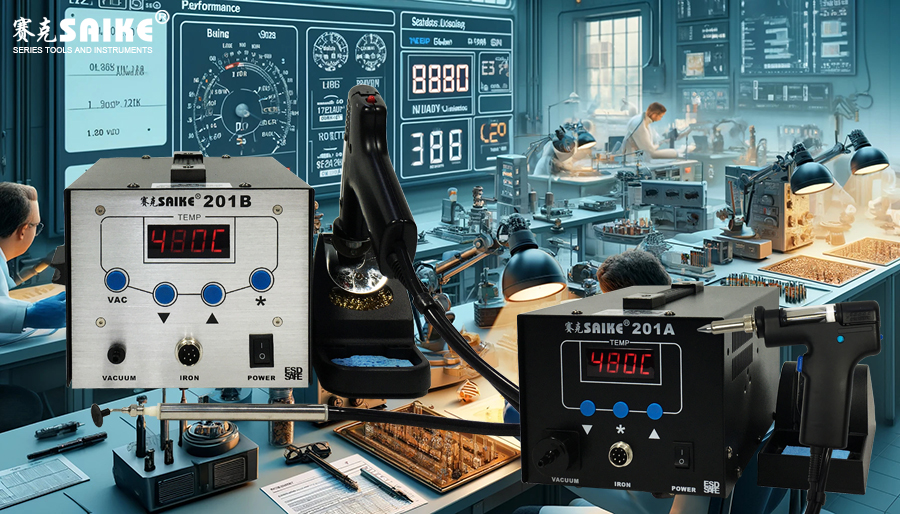
SK-YJ000DDXXQ-KP 100020
The electric solder sucker is an important tool in the electronic manufacturing and maintenance industry, and its performance directly affects the work efficiency. Reasonable test methods and standards are the key to ensuring that its performance meets industrial needs. The following are the performance test methods and related standards for electric solder suckers.
I. Performance Test Methods
1.Heating Time Test
– Set the solder sucker to a specific temperature, and use a thermocouple or infrared thermometer to time from power-on to reaching the set temperature. Record multiple test results and calculate the average to evaluate heating efficiency.
2.Temperature Stability Test
– After continuous work for a certain period of time (such as 30 minutes), monitor whether the working temperature of the solder sucker remains within ±5°C of the set temperature. Use a high-precision temperature sensor to record temperature fluctuations.
3.Solder Sucking Capability Test
– For standard solder joints (such as 1.5mm diameter solder balls), test the time it takes for the solder sucker to remove the solder and the cleanliness of the solder joints after removal. Use a microscope to evaluate and record the residual solder.
4.Energy Consumption Efficiency Test
– Measure the power consumption of the solder sucker under standard operating conditions. Record the total energy consumption within a certain period of time through an electricity meter, and calculate its energy consumption efficiency.
5.Service Life and Reliability Test
– Continuous work test to simulate a long-term working environment, record the time when the solder sucker malfunctions or its performance degrades. Check the durability and failure rate of the solder sucker.
6.Maintenance Convenience Evaluation
– Evaluate the ease of maintenance work such as nozzle replacement and internal cleaning. Record the time and tools required for replacement and cleaning through actual operation tests.
II. Performance Test Standards
1.International Standards
– Refer to the standards of relevant electronic tools of IEC (International Electrotechnical Commission). For example, IEC 60335-2-45 specifically stipulates the safety of electronic tools, including solder suckers.
2.National Standards
– Countries may have specific national standards for electronic manufacturing tools, such as China’s GB standards and the United States’ ANSI standards. Testing should be conducted in accordance with the standards of the corresponding region.
3.Industry Standards
– Electronic industry organizations or large electronic manufacturing companies may have their own standards, which are usually stricter than general standards and specifically target the specific requirements of their products.
4.Quality Certification
– Quality management system certifications such as ISO 9001 can provide a management and technical framework for the performance testing of solder suckers.
III. Summary
The performance test of the electric solder sucker is an important part of ensuring that it can achieve the expected effect in practical applications. Through standardized test methods and strict testing based on international and national standards, the performance and reliability of the solder sucker can be effectively evaluated. Developing a detailed test plan and executing these tests is the foundation for improving product quality and meeting customer needs. Correct test methods and standards are of great significance to guide the design, manufacturing, and maintenance of electric solder suckers.