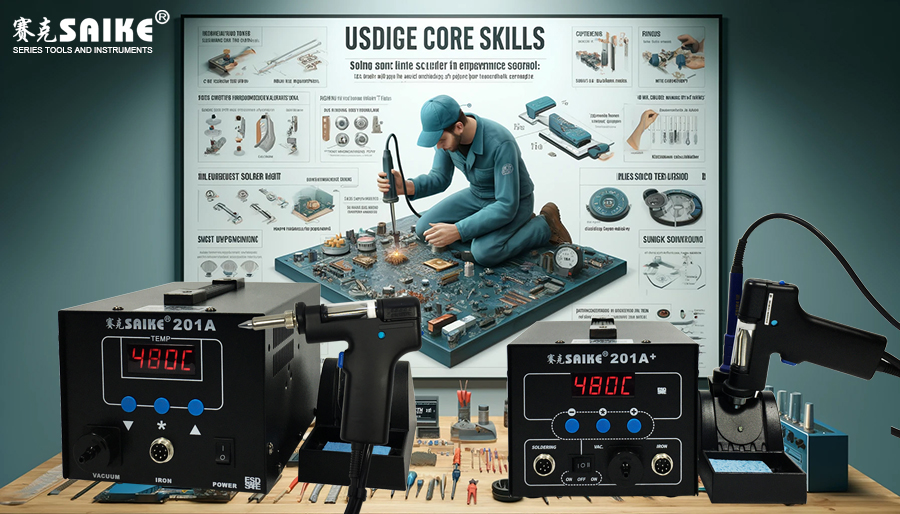
SK-YJ000ZLWYDY-KP 100027
The PCB (Printed Circuit Board) design of a DC stabilized voltage supply has a significant impact on the performance and stability of the power supply. Reasonable wiring and layout can effectively reduce interference and improve power efficiency and reliability. This article will explore the key considerations and routing techniques for PCB design of DC stabilized voltage supplies.
I. Preparation before PCB Design
1.Design Software Selection
– Commonly used PCB design software includes Altium Designer, Cadence OrCAD, Eagle, etc. Choose the right tool for your project and budget.
2.Determination of Design Specifications
– Determine the size, number of layers, and necessary electrical and thermal management requirements of the PCB.
3.Schematic Review
– Thoroughly review the schematic diagram before proceeding with the PCB layout to ensure that all connections are correct.
II. Layout and Routing Principles
1.Component Layout
– Priority to key components: Place key components such as switching controllers, inductors, capacitors, etc. first.
– Thermal management: High-power components should be kept away from sensitive signals and microprocessors. Consider space for heat sinks or fans if necessary.
2.Power and Ground Layer Design
– Use separate power and ground layers to reduce power noise and provide a low-impedance path.
3.Signal Path Optimization
– Short path: Minimize high-frequency signals and power paths to reduce EMI and signal loss.
– Avoid crossings: Prevent high-frequency signal lines from crossing analog signal lines to avoid mutual interference.
III. Specific Routing Techniques
1.Ground Wire Routing
– Design an adequate ground wire network, especially using multiple ground points near critical signals and power loops.
2.Power Line Routing
– Use thicker power lines to reduce resistance and voltage drop, especially on paths connected to inductors and switching tubes.
3.Signal Integrity
– Use impedance-controlled routing for high-speed signal lines to ensure signal integrity.
4.Decoupling Capacitor Layout
– Place decoupling capacitors as close as possible to the power pins to reduce impedance between pins.
5.Thermal Management Routing
– Design multiple vias under high-power components to help transfer heat from one side to the other or connect to a dedicated heat dissipation layer.
IV. PCB Debugging and Testing
1.Test Point Settings
– Reserve enough test points during the design phase to facilitate debugging and subsequent functional testing.
2.Preliminary Electrical Testing
– After completing the PCB assembly, perform a simple electrical test first to check for any short circuits or open circuits.
3.Functional Verification
– Use functional tests to verify that the circuit board works as intended, including voltage, current, and power output.
V. Summary
The PCB design of a DC stabilized voltage supply requires comprehensive consideration of electrical performance, signal integrity, thermal management, and practical operational feasibility. Through reasonable layout and routing, the overall performance and stability of the power supply can be significantly improved. Good practices in PCB design also include regularly reviewing and optimizing existing designs to adapt to changing technical requirements and application environments. In practical applications, it is essential to conduct adequate testing to ensure that the design meets all technical and safety standards.