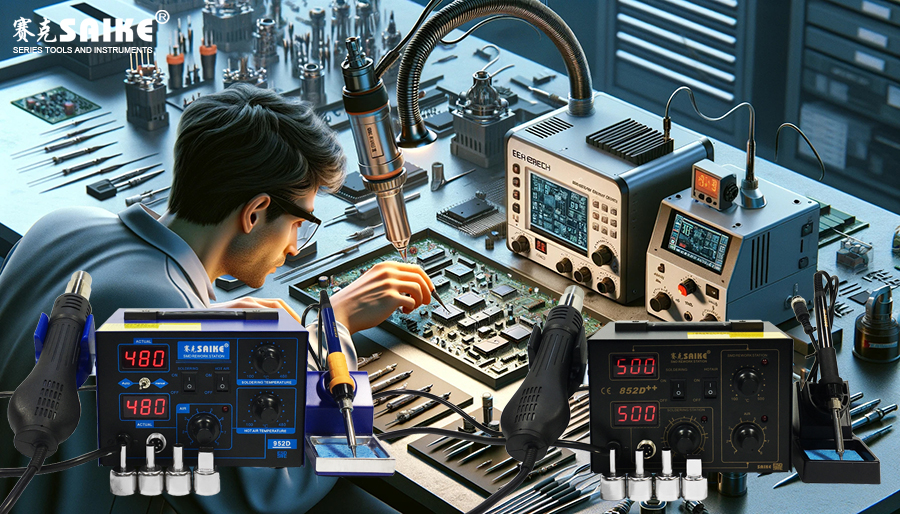
SK-YJ000RFCHT-KP 100018
The hot air rework station is a crucial tool in electronic manufacturing and repair, especially when dealing with special electronic components and complex soldering situations. This article explores how to handle sensitive and complex electronic components using a hot air rework station and provides effective soldering and desoldering strategies.
I. Strategies for Handling Special Electronic Components
1.Handling High-Precision and Micro Components:
– Temperature Control: For micro or high-precision components, precise temperature control is essential. The temperature should be set slightly above the melting point of the solder to avoid thermal damage.
– Airflow Adjustment: Use a lower airflow speed and a small nozzle to prevent strong air currents from displacing or damaging the components.
2.Handling Sensitive Components:
– Preheating Strategy: To reduce thermal shock, the board can be preheated, allowing the substrate and components to gradually adapt to the required operating temperature.
– Multi-Point Heating: Avoid continuous heating at a single point by adopting multi-point heating and evenly distributing heat to reduce thermal stress on a single point.
3.Handling Sensitive Packaged ICs:
– Indirect Heating: For packages that are easily damaged by heat, such as BGA, indirect heating can be used by first heating the surrounding area and then gradually approaching the core area.
– Using Specialized Tools: For specific types of ICs, use specially designed nozzles to accommodate their unique sizes and shapes.
II. Strategies for Complex Soldering Situations
1.Multi-Layer Circuit Board Soldering:
– Layered Heating: For multi-layer circuit boards, use a layered heating technique from the outside in, gradually increasing the temperature layer by layer to avoid damage to internal layers due to excessive temperature.
– Temperature Monitoring: Use thermal imaging cameras or other temperature monitoring tools to monitor the soldering process in real-time, ensuring uniform temperature across all layers.
2.Large Area Metal Plate Soldering:
– High-Temperature Rapid Operation: Due to the high thermal conductivity of metal, higher temperatures and rapid operations may be required to maintain the appropriate temperature in the soldering area.
– Local Shielding: Use thermal shielding materials to protect surrounding sensitive components and prevent accidental damage caused by heat diffusion.
3.Desoldering of Complex Connection Points:
– Sequential Desoldering: For complex soldering points, such as multi-pin components, adopt a sequential desoldering method to address each soldering point step by step, preventing pad damage caused by uneven heating.
– Cooling Management: Immediately after desoldering, use appropriate cooling techniques, such as air blowing or special coolants, to rapidly reduce the temperature of the soldering points and prevent damage caused by residual heat.
III. Conclusion
Using a hot air rework station to handle special electronic components and complex soldering situations requires precise technology and meticulous operation. By adjusting temperature and airflow speed, selecting the appropriate nozzle, adopting preheating and multi-point heating strategies, the safety and efficiency of soldering and desoldering can be effectively improved. Each special situation requires the operator to have a deep understanding of the equipment and rich operational experience to ensure the best operational results. These strategies not only help protect valuable electronic components but also ensure high-quality completion of the entire soldering work.