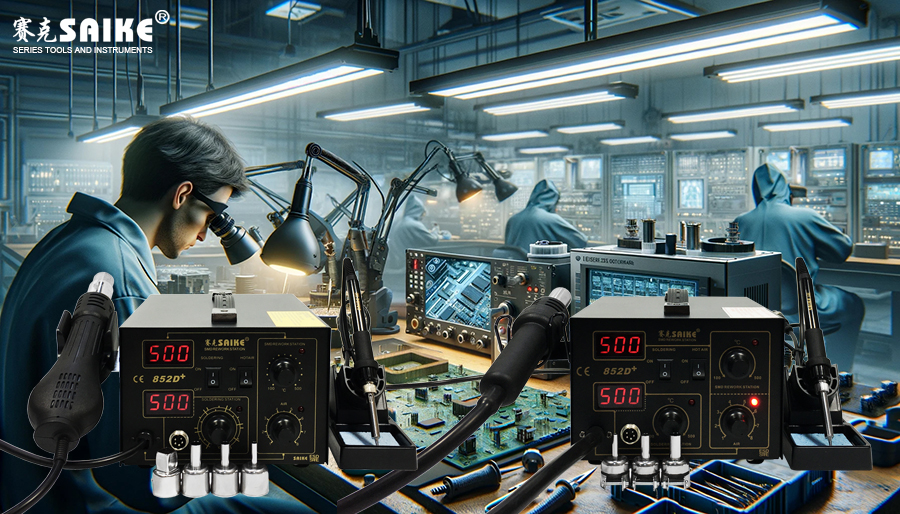
SK-YJ000RFCHT-KP 100029
In the modern electronics repair and manufacturing industry, the hot air rework station has become an indispensable tool, demonstrating high efficiency and accuracy in precision soldering and desoldering tasks. However, using the hot air rework station alone may not always meet all soldering needs, especially when dealing with complex or diverse electronic components. Combining it with other soldering techniques can improve work efficiency, quality, and applicability. This article explores the combined use of hot air rework stations and other soldering techniques, providing practical application scenarios and operational suggestions.
I. Combined Soldering Techniques
1.Traditional Soldering Iron
– Application Scenario: Suitable for most conventional soldering tasks, especially single solder joint processing and simple circuit board repairs.
– Combined Advantages: Before using the hot air rework station for large-area processing, using a soldering iron to treat individual or difficult-to-reach solder joints with hot air can avoid overheating and damaging adjacent components.
2.Infrared Soldering Technology
– Application Scenario: Suitable for large or complex PCB boards that require uniform heating, such as full-board rework.
– Combined Advantages: Using infrared soldering technology to preheat the entire board and then using a hot air rework station to precisely process specific areas can improve heating efficiency and reduce thermal stress.
3.BGA Rework Station
– Application Scenario: Specifically designed for handling Ball Grid Array (BGA) packaged chips.
– Combined Advantages: After precise positioning and initial heating are completed at the BGA rework station, the hot air rework station is used for final soldering adjustments and repairs to ensure the integrity of the solder joints.
II. Operational Suggestions for Combined Use
1.Thermal Management
– Reasonable management of operating temperature is crucial when combining different soldering techniques. For example, when using a hot air rework station immediately after infrared soldering preheating, the hot air temperature should be adjusted appropriately to prevent overheating.
2.Precise Control
– When used in combination, precise control of various equipment operating parameters (such as temperature, time, air speed, etc.) is the basis for ensuring soldering quality. Using advanced control systems and sensors can improve the accuracy and repeatability of this process.
3.Soldering Sequence
– When performing maintenance on complex components, the correct soldering sequence is very important. It is generally recommended to use the hot air rework station to remove or reposition key components first, and then use a soldering iron for detailed repairs.
4.Safe Operation
– When combining multiple soldering techniques, safe operation is particularly important. Ensure that all equipment is properly grounded, and operators should use necessary personal protective equipment, such as anti-static gloves and protective glasses.
III. Practical Application Examples
1.Rework of Multilayer Circuit Boards
– When processing multilayer circuit boards, first use infrared soldering technology for overall preheating, and then use a hot air rework station to precisely remove or solder specific high-density integrated circuits.
2.Maintenance of Complex Communication Equipment
– When repairing complex communication equipment containing multiple connection technologies, the combination of a hot air rework station and a soldering iron can effectively handle different components from large connectors to tiny resistors.
IV. Summary
The combined use of hot air rework stations and other soldering techniques provides more flexibility and efficiency for electronic repairs. By rationally allocating soldering resources, it can effectively improve the ability to process complex electronic equipment, reduce repair risks, and increase the success rate of repairs. Maintenance technicians should select appropriate soldering technology combinations according to the needs of specific tasks to ensure soldering quality and equipment safety.