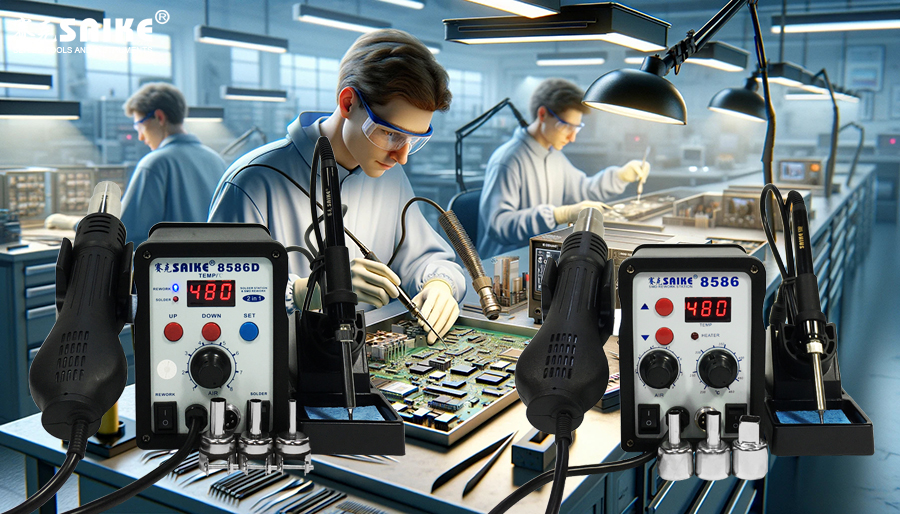
SK-YJ000RFCHT-KP 100020
The hot air rework station plays a crucial role in the electronic repair industry, especially when performing delicate tasks such as mobile phone cable desoldering and laptop chip replacement. This article demonstrates the application of the hot air rework station through two specific case studies, exploring how to effectively utilize this tool to complete complex repair tasks.
I. Case Study 1: Mobile Phone Cable Desoldering
Background: In mobile phone repair, cable desoldering is a common but high-precision operation. Cables are typically used to connect different functional modules of the phone, such as the screen, camera, and motherboard. The connection points of the cables are extremely small and fragile, and any excessive heat or force can cause damage.
Operational Steps:
1.Preparation:
– Clean the area to be desoldered and confirm the cable model and connection method.
– Set the temperature and air speed of the hot air rework station. The temperature is usually set between 180°C and 200°C, and the air speed is set to low or medium to prevent hot air from directly blowing away or damaging the fragile cables.
2.Heating and Desoldering:
– Use a small nozzle to aim at the soldering points of the cable and heat evenly. Slowly move from one end to the other, ensuring that each soldering point is properly heated.
– Use fine tweezers to gently lift the melted soldering points and carefully separate the cable from the connection board.
3.Inspection and Cleanup:
– Check the cable and motherboard soldering points to ensure there is no residual solder or damage.
– Use a residue-free cleaner to clean the desoldering area in preparation for subsequent soldering or assembly work.
Precautions:
– Avoid overheating, as cables are very sensitive and can be easily damaged by high temperatures.
– Ensure that the workstation is anti-static during the operation to avoid electrostatic damage to electronic components.
II. Case Study 2: Laptop Chip Replacement
Background: In laptop repair, chip replacement (such as CPU or GPU) is a technically demanding task. These chips are typically soldered to the motherboard through BGA packaging, requiring precise control of heat distribution during desoldering.
Operational Steps:
1.Preparation and Setup:
– Clean the chip and surrounding areas, especially removing dust and stains.
– Adjust the hot air rework station according to the packaging and material characteristics of the chip. The temperature is generally set between 220°C and 240°C, with a medium air speed.
2.Heating and Removal:
– Use a nozzle suitable for BGA packaging to evenly heat the area around the chip. Use a circular or spiral heating pattern to ensure uniform heat distribution.
– Monitor the temperature to avoid localized overheating. Once the solder melts, carefully lift the chip using a BGA extraction tool.
3.Cleanup and Inspection:
– Use solder wick to remove excess solder from the motherboard, keeping the soldering pads clean.
– Check if the motherboard soldering pads are flat and undamaged, preparing for the installation of a new chip.
Precautions:
– Avoid heating the chip directly for too long to prevent damage to its internal structure.
– Maintain a balanced heating and cooling process to prevent the motherboard from bending or cracking due to excessive temperature differences.
III. Conclusion:
The hot air rework station is an ideal tool for handling complex tasks such as mobile phone cable desoldering and laptop chip replacement. Through the above case studies, we can see that precise control of temperature, air speed, and proper operating techniques are the keys to successful desoldering. For electronic repair professionals, mastering these skills and knowledge is the foundation for improving work quality and efficiency.