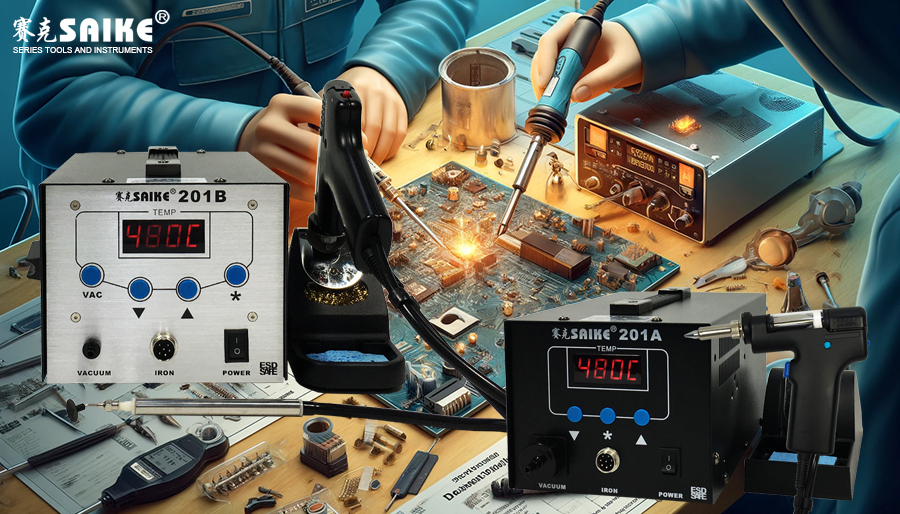
SK-YJ000DDXXQ-KP 100022
The electric solder sucker is a commonly used tool in the electronic repair and assembly industry. By analyzing successful and failed cases of desoldering operations, we can gain a deeper understanding of how to effectively use this tool and avoid potential problems.
I. Analysis of Successful Cases
1.Efficient Component Removal
Case Description: During a repair job on a multilayer circuit board, a technician used an electric solder sucker for efficient component removal. The circuit board contained tightly arranged components, requiring precise and rapid removal of faulty parts.
Operational Procedure:
– Preheating: The technician first preheated the electric solder sucker to a suitable working temperature to ensure fast melting of the solder paste.
– Precise Positioning: Used a solder sucker with a suitable tip to aim at the soldering point, ensuring no damage to adjacent components.
– Quick Operation: Immediately activated the solder sucking pump after the solder paste melted, sucking away the solder on the soldering point in one go, effectively avoiding excessive heating time.
Success Factors:
– Correct temperature control and optimized solder sucking time.
– Used suitable soldering iron tips to adapt to different sizes of soldering points.
– Skilled operational ability and quick response.
2.Component Protection
Case Description: Successfully avoided thermal damage during the removal of sensitive electronic components, ensuring the integrity and functionality of the components.
Operational Procedure:
– Appropriate Temperature Setting: Adjusted the temperature setting of the solder sucker to adapt to the characteristics of sensitive components.
– Short-time Operation: Quickly completed the solder sucking process, reducing the time the components were exposed to high temperatures.
Success Factors:
– Efficient thermal management to avoid thermal damage to sensitive components.
– The application of appropriate tools and techniques to ensure the accuracy and safety of the operation.
II. Analysis of Failed Cases
1.Component Damage
Case Description: While attempting to remove a central processing unit (CPU), the CPU was damaged due to improper temperature control and inexperienced operation.
Reasons for Failure:
– Excessively High Temperature: The temperature of the solder sucker was too high, causing overheating of the microscopic soldering points on the CPU surface and damaging the chip.
– Improper Operation: The operator was eager to suck the solder before the soldering points were completely melted, resulting in partial solder residue and damaged pins.
2.Excessive Heating
Case Description: During the repair of an old radio, prolonged and continuous use of the solder sucker led to overheating and peeling off of multiple soldering points and copper foils on the circuit board.
Reasons for Failure:
– Extended Continuous Operation: Lack of intermittent rests resulted in localized overheating of the circuit board due to continuous heating.
– Lack of Proper Heat Dissipation Measures: There were no appropriate heat dissipation measures during the desoldering process, leading to heat accumulation.
III. Conclusion
By analyzing the successful and failed cases of desoldering operations with an electric solder sucker, we can summarize several key points: correct equipment settings (such as temperature and suction power), skilled operational ability, appropriate operation time, and necessary maintenance are crucial factors for successful desoldering. Proper use and maintenance of the electric solder sucker can not only improve work efficiency but also avoid unnecessary losses and malfunctions.