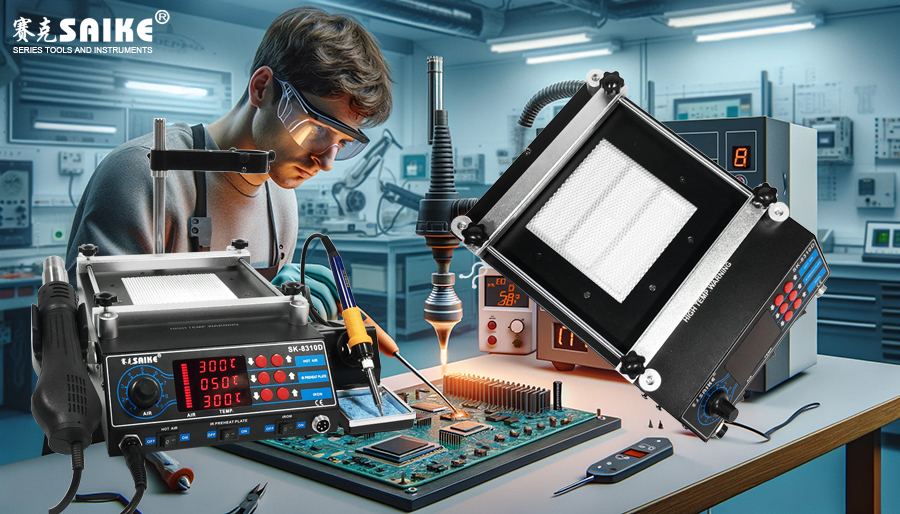
SK-YJ000YRT-KP 100017
The preheating station plays a crucial role in electronic repair, especially when it comes to circuit board repairs. Proper preheating can reduce thermal stress during soldering, prevent circuit board warping, and improve soldering quality. This article explores some key techniques for circuit board repair using a preheating station, aiming to help maintenance technicians improve repair efficiency and quality.
I. Understanding the Importance of Preheating
Before starting the repair work, it is crucial to understand the basic principles and benefits of preheating:
1.Reducing Thermal Stress: Uniform preheating helps to balance the temperature across the entire circuit board, reducing thermal stress caused by localized overheating or rapid temperature changes.
2.Improving Soldering Quality: Preheating allows the solder to reach a flow state with lower external heating, which helps reduce cold solder joints and dry joints.
3.Protecting Sensitive Components: Gradually increasing the temperature helps protect sensitive components on the circuit board, such as microprocessors and oscillators, from damage caused by instant high temperatures.
II. Choosing the Appropriate Preheating Temperature
Determining the suitable preheating temperature is key to successful circuit board repair:
1.Material Considerations: Understanding the material of the circuit board and its thermal capacity characteristics. The thermal expansion rate and temperature resistance of different materials can affect the preheating temperature setting.
2.Solder Requirements: Set the appropriate preheating temperature based on the melting point of the solder used. Typically, the preheating temperature is set to 50% to 70% of the solder’s melting point.
III. Gradual Heating Strategy
When using a preheating station, gradual heating is an effective technique:
1.Progressive Heating: Avoid exposing the circuit board directly to a high-temperature environment. Start at a lower temperature and gradually increase it to the target temperature.
2.Using Temperature Profiles: If the preheating station supports programming, set a temperature profile that allows the board to heat up evenly over a period.
IV. Monitoring and Adjustment
Continuous temperature monitoring and making necessary adjustments during the preheating process are crucial for successful repairs:
1.Using Temperature Sensors: Utilize embedded or external temperature sensors to monitor the circuit board’s temperature in real-time.
2.Adjusting Preheating Time: Adjust the preheating time appropriately based on the circuit board’s response. Thicker boards or large components may require longer preheating times.
V. Safe Operation
Following safe operating practices is crucial when using a preheating station for circuit board repairs:
1.Personal Protection: Ensure wearing appropriate protective equipment, such as heat-resistant gloves and protective glasses.
2.Equipment Safety Inspection: Check the power cord, heating elements, and control system of the preheating station before each use to ensure they are working properly.
VI. Post-processing and Testing
Proper post-processing and testing after completing the preheating and subsequent soldering repairs are essential:
1.Slow Cooling: Allow the circuit board to cool naturally after turning off the preheating station to avoid thermal stress caused by rapid cooling.
2.Functional Testing: Perform necessary functional tests after the repair to ensure the repaired area and the circuit board are working properly.
VII. Conclusion
The preheating station is an indispensable tool in the circuit board repair process. Proper use of the preheating station can not only improve the success rate of repairs but also protect the integrity of the circuit board and components. By following the above tips and strategies, technicians can effectively utilize the preheating station for circuit board repairs, ensuring that each repair meets the expected quality standards.