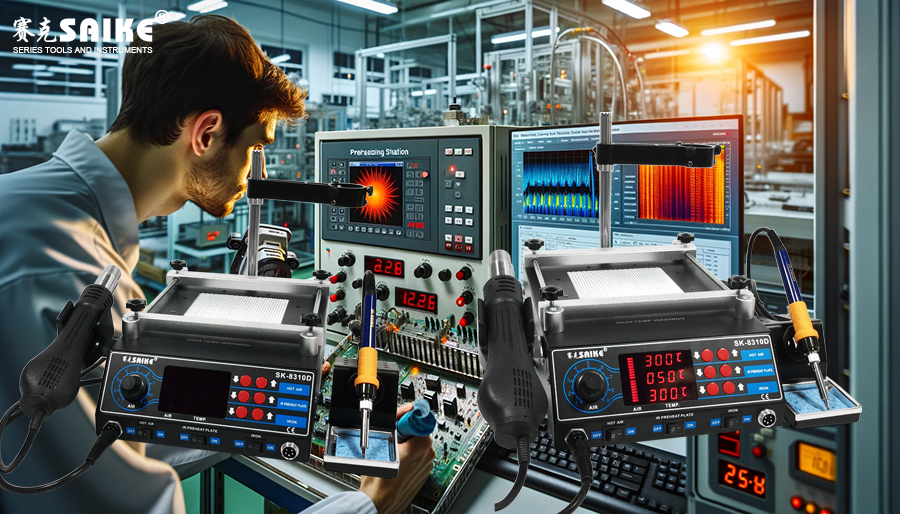
SK-YJ000YRT-KP 100011
The preheating station is a crucial equipment in the manufacturing and maintenance of electronic components, used to preheat circuit boards in advance to optimize the soldering process. Proper temperature control and effective temperature monitoring are essential to ensure soldering quality and prevent component damage caused by thermal stress. This article explores the best practices for temperature control and monitoring on preheating stations to assist technicians in improving operational efficiency and product quality.
I. Setting Appropriate Temperatures
1.Understanding Material Requirements:
– Determine the characteristics of the circuit board material and solder, including melting point and heat capacity. This information guides temperature settings, ensuring that the solder’s melting point is not exceeded while allowing the solder to quickly reach a flow state during soldering.
2.Adjusting Temperature Based on Component Size:
– Consider the size and thickness of the circuit board. Thicker or larger circuit boards require higher preheating temperatures or longer preheating times to ensure uniform heat distribution.
3.Adopting a Gradual Heating Strategy:
– To avoid thermal shock, a gradual heating strategy is employed, slowly increasing the temperature until the desired preheating temperature is reached. This approach helps to balance thermal stresses within the material, reducing the risk of warping and interlayer separation.
II. Implementing Efficient Temperature Control Systems
1.Using Precise Temperature Controllers:
– Choose temperature controllers with PID (Proportional-Integral-Derivative) adjustment capabilities. These controllers can adjust heating power in real-time, maintaining small temperature fluctuations within the set range and ensuring precise temperature control.
2.Configuring Multi-point Temperature Sensors:
– Install multi-point temperature sensors on the preheating station, especially for large or complex-shaped circuit boards. This helps monitor the temperature in different areas of the circuit board, ensuring uniform heating across the entire board.
3.Implementing Automated Temperature Adjustment:
– Utilize automated software and hardware tools to adjust temperature settings based on real-time data, responding to temperature changes and process requirements.
III. Achieving Effective Temperature Monitoring
1.Regularly Calibrating Temperature Equipment:
– Ensure that all temperature measurement equipment and sensors are regularly calibrated to maintain measurement accuracy. Inaccurate temperature readings can lead to out-of-specification products.
2.Utilizing Data Logging Capabilities:
– Use a temperature control system with data logging capabilities to record temperature data throughout the heating process. This data can be used for subsequent quality control analysis and process improvement.
3.Real-time Temperature Monitoring and Feedback:
– Employ a real-time monitoring system to observe temperature changes and visually monitor heating effects through visualization tools (such as thermal imaging cameras). Adjust operating parameters in response to any abnormalities.
IV. Training and Education
1.Operator Training:
– Regularly train operators on preheating station operations and temperature control to ensure they understand the equipment’s functionality and operating principles. This enables them to take appropriate actions when issues are identified.
2.Sharing Best Practices:
– Facilitate knowledge updates and skill enhancement by sharing industry best practices and the latest temperature control techniques through workshops and training sessions.
V. Conclusion
Proper temperature control and effective temperature monitoring are crucial when using preheating stations. Implementing precise temperature settings, adopting advanced temperature control systems, and achieving real-time temperature monitoring significantly improve the performance of the preheating station, ensuring the quality and safety of the soldering process. Additionally, investing in personnel training and technological updates is an essential aspect of continuously improving preheating station operations.