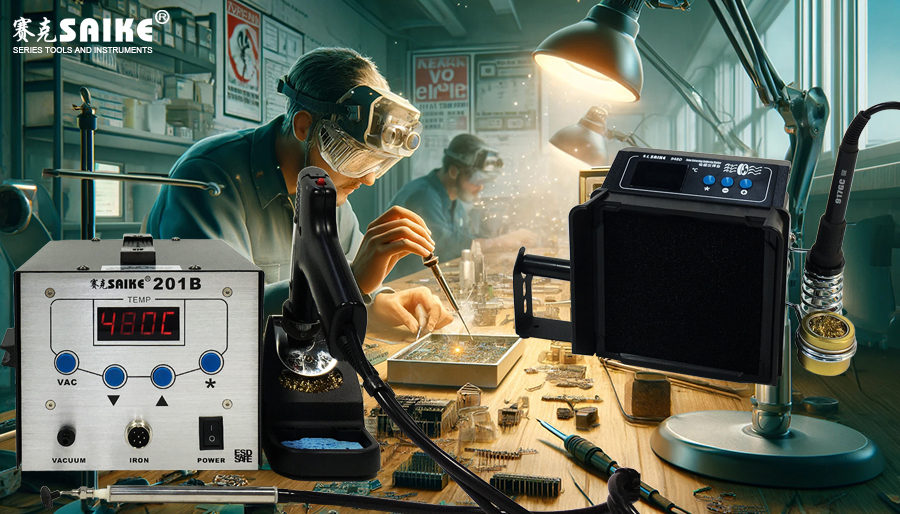
SK-YJ000DLT-KP 100022
The electric soldering iron is an indispensable tool for electronic engineers and enthusiasts in electronic production and maintenance. However, various problems may arise during soldering with an electric soldering iron. This article aims to analyze these common problems in detail and provide corresponding solutions to help users master soldering technology more proficiently.
I. Weak Solder Joints
Weak solder joints are a common problem during the soldering process, which may lead to loose or broken solder joints. To solve this problem, the following measures can be taken:
1.Clean the soldering area: Ensure that the surface of the soldering area is clean and free of oil, oxides, or other impurities.
2.Choose suitable solder: Use high-quality solder to ensure good wettability and conductivity.
3.Control soldering time and temperature: The soldering time should not be too long, and the temperature should not be too high to avoid thermal damage to the soldering area.
II. Overheating during Soldering
Overheating during soldering may damage the soldering area and even burn electronic components. To avoid this problem, the following measures can be taken:
1.Adjust the temperature of the soldering iron beforehand: Adjust the temperature of the soldering iron according to the soldering requirements before soldering to avoid excessive temperature.
2.Control soldering time: The soldering time should not be too long to reduce thermal damage to the soldering area.
3.Use thermal resistance materials: During soldering, thermal resistance materials can be used to protect surrounding electronic components and reduce heat transfer.
III. Small Soldering Area
Some electronic components have small soldering areas, and improper operation may lead to inaccurate solder joints. To solve this problem, the following measures can be taken:
1.Choose a suitable soldering iron tip: Use an appropriately sized soldering iron tip to ensure accurate alignment with the soldering area.
2.Positioning before soldering: Perform accurate positioning before soldering to ensure close contact between the soldering iron tip and the soldering area.
3.Maintain a stable gesture: Maintain a stable gesture during soldering to avoid inaccurate solder joints caused by shaking of the soldering iron tip.
IV. Large Solder Joints or Large Soldering Area
Large solder joints or soldering areas not only affect the appearance but also the performance and stability of the circuit. Excessively large solder joints may lead to unnecessary electrical connections or short circuits, while an excessively large soldering area may waste materials and increase unnecessary thermal stress. To solve this problem, the following measures can be taken:
1.Precise control of solder amount: During soldering, the amount of solder should be precisely controlled to avoid using too much solder. The ideal solder joint size can be achieved by adding solder in small amounts multiple times.
2.Choosing the right soldering iron tip: The size and shape of the soldering iron tip directly affect the size of the solder joint. Choosing an appropriately sized soldering iron tip can better control the flow and distribution of solder, resulting in ideal solder joints.
3.Improving soldering skills: Learning and practicing soldering skills, mastering appropriate soldering time and temperature, as well as the moving speed and direction of the soldering iron tip, can help form small and uniform solder joints.
4.Using flux: An appropriate amount of flux can help the solder flow and wet the soldering area better, thereby reducing the amount of solder used and forming smaller solder joints.
5.Follow-up processing: If the solder joint is already formed and too large, appropriate tools (such as a solder sucker) can be used to remove excess solder, and then re-solder to reduce the size of the solder joint.
6.Prevention-oriented approach: Before soldering, plan the soldering area and solder joint size to avoid random soldering, which may lead to excessively large solder joints or soldering areas.
Large solder joints or soldering areas are common problems during soldering, but they can be effectively solved through precise control of solder amount, selection of appropriate soldering iron tips, improvement of soldering skills, use of flux, and follow-up processing. When soldering, a prevention-oriented approach should be taken to plan the soldering area and solder joint size in advance to achieve a more aesthetic and stable soldering effect. Continuous learning and practice are the keys to improving soldering skills.
V. Large Solder Joints or Surrounding Metal Parts Causing Difficulties in Soldering
When solder joints are too large or surrounded by metal parts, soldering can indeed become challenging. Large solder joints, due to their mass and high heat capacity, are difficult to rapidly heat to a sufficient temperature for good soldering, while surrounding metal parts may draw away significant heat, leading to insufficient soldering temperature. To address these issues, the following measures can be taken:
1.Increase soldering iron power or use a more efficient soldering iron tip: Utilize a soldering iron with higher wattage or replace the tip with one that has better heat conductivity to provide more heat to the soldering area.
2.Preheat metal parts: If possible, preheat the surrounding metal parts. This reduces their ability to absorb heat from the soldering iron during the soldering process.
3.Use flux: Applying an appropriate amount of flux can enhance the fluidity of solder, making it easier to penetrate the soldering joint.
4.Segmented soldering: For exceptionally large solder joints, segmented soldering can be attempted, where one part is soldered first and then the other, reducing the amount of metal that needs to be heated at once.
5.Use a hot air gun or preheating station: Preheat the soldering area with a hot air gun before soldering, or use a preheating station to evenly heat the entire circuit board, making soldering easier.
6.Remove oxides: Ensure the soldering area is oxide-free, as oxides can hinder solder flow. Use sandpaper or specialized oxide removers for cleaning.
7.Utilize other heat sources: If a soldering iron is insufficient, consider using alternative heat sources like a small torch (with caution) or professional soldering equipment.
When encountering large solder joints or metal parts around the soldering area that make soldering difficult with a soldering iron, increasing soldering iron power, preheating metal parts, using flux, segmented soldering, employing a hot air gun or preheating station, removing oxides, and utilizing other heat sources are viable solutions. Safety should always be a top priority during these operations, avoiding risks like burns or electric shocks. If difficulties arise or uncertainty persists, seeking professional assistance is advisable.
VI. Uneven Soldering
Uneven soldering can compromise soldering quality, affecting circuit stability and conductivity. To address this, consider the following measures:
1.Master soldering techniques: Acquire proficient soldering skills through learning and practice, ensuring even solder coating in the soldering area.
2.Maintain hand stability: Steady hands during soldering prevent iron tip movement, ensuring even solder distribution.
3.Utilize flux: Applying an adequate amount of flux before soldering aids in solder flow and wetting of the soldering area.
VII. Cold Solder Joints
Cold solder joints occur when solder fails to fully melt or establish a good electrical connection with the soldering area. To resolve this:
1.Adjust soldering iron temperature: Ensure the soldering iron is set to a high enough temperature for complete solder melting.
2.Clean soldering iron tip: Regularly clean the tip to eliminate oxides and impurities, improving heat conduction.
3.Manage soldering time and pressure: Adequate soldering duration and pressure facilitate a solid connection between solder and the soldering area.
VIII. Other Common Issues and Solutions
1.Electric shock and burn hazards: Always ensure proper grounding to prevent electric shocks and be mindful of hot iron tips to avoid burns.
2.Worn or damaged soldering iron tips: Regularly inspect tip condition and replace promptly if worn or damaged.
3.Choosing suitable solder and flux: Select the right solder and flux based on soldering requirements and material characteristics for optimal soldering quality.
IX. Conclusion
In conclusion, various issues may arise during soldering with an electric soldering iron. However, by acquiring proper soldering techniques, using suitable materials and tools, and prioritizing safety, these challenges can be effectively tackled, enhancing soldering quality. This article aims to provide valuable insights and assistance to electronic engineers and enthusiasts alike.