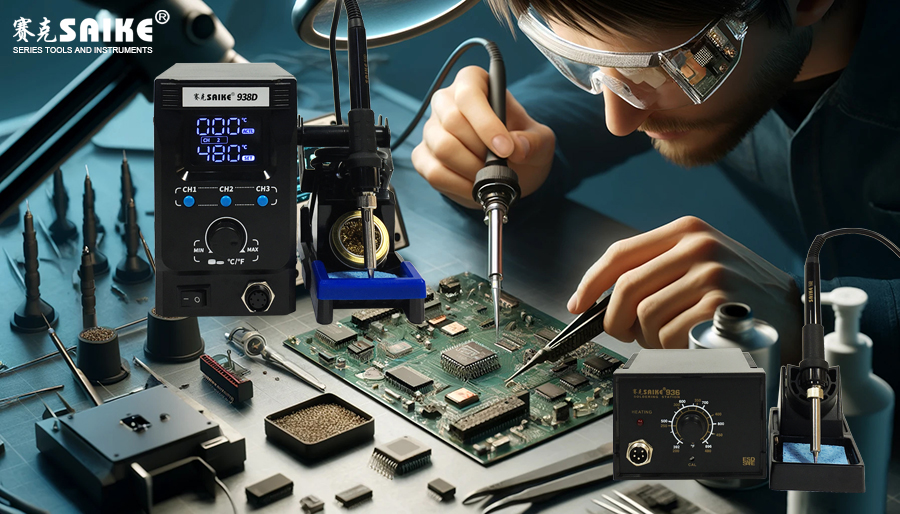
SK-YJ000HT-KP 100029
Surface-Mount Technology (SMT) plays a crucial role in modern electronics manufacturing, enabling automated machines to precisely and quickly place tiny components on circuit boards. While many SMT components are soldered during production using solder paste and reflow soldering processes, manual soldering of SMD components on a soldering station remains important in prototyping, small-batch production, or repair services. Here are some tips and suggestions for manually soldering surface mount devices.
I. Preparation
1.Understand Component Characteristics
– Before soldering, it’s essential to understand the thermal sensitivity and electrical characteristics of the components. This helps in selecting the appropriate soldering temperature and soldering strategy to prevent damage.
2.Tool and Material Selection
– Use a soldering iron with a fine tip, which aids in precise heating of pins without touching adjacent ones.
– Choose low-temperature solder, such as silver-containing lead-free solder, due to its lower melting point, reducing thermal damage to components.
– Utilize good quality flux, which aids solder flow and prevents oxidation.
3.Clean the Soldering Area
– Use a non-residue cleaner, like isopropyl alcohol, to clean the PCB pads, ensuring no dust, grease, or oxidation layers.
II. Soldering Techniques
1.Temperature Control
– Set the soldering iron to an appropriate temperature, typically between 250°C and 300°C, depending on the solder and component heat resistance.
2.Soldering Sequence
– For multi-pin SMD components like QFP or SOIC, solder two pins on the diagonal first to fix the component’s position. Then, solder the remaining pins sequentially to prevent component displacement due to excessive heat.
3.Soldering Skills
– Apply solder to the soldering iron tip first, then gently touch the junction of the pin and pad, allowing the solder to naturally flow into the joint.
– Avoid using too much solder to prevent bridging between pins.
– Use tweezers or a third-hand tool to stabilize the component.
III. Inspection and Cleanup
1.Visual Inspection
– Use a magnifying glass or microscope to inspect each solder joint for cold solders, dry joints, or solder bridges.
– Ensure good solder joint shape, with solder wetting the pad and slightly rising onto the pin, forming a “mountain” or “pillow” shape.
2.Cleaning
– After soldering, remove any remaining flux, especially if an active flux was used, with a non-residue cleaner.
IV. Safety and Maintenance
1.Soldering Iron Maintenance
– Regularly clean the soldering iron tip to keep it shiny and contaminant-free.
– Check if the soldering iron tip needs replacement to ensure optimal heat transfer efficiency and soldering accuracy.
2.Personal Safety
– Ensure good ventilation to avoid inhaling harmful soldering fumes.
– Use appropriate protective eyewear and gloves, especially when handling active fluxes and high-temperature equipment.
V. Conclusion
Although soldering SMD components on a soldering station may be more challenging than traditional through-hole components, using the right tools, materials, and techniques can effectively accomplish these tasks, ensuring high-quality soldering results. Experience accumulation and meticulous operation are key to improving soldering quality, while also focusing on safety and health protections.