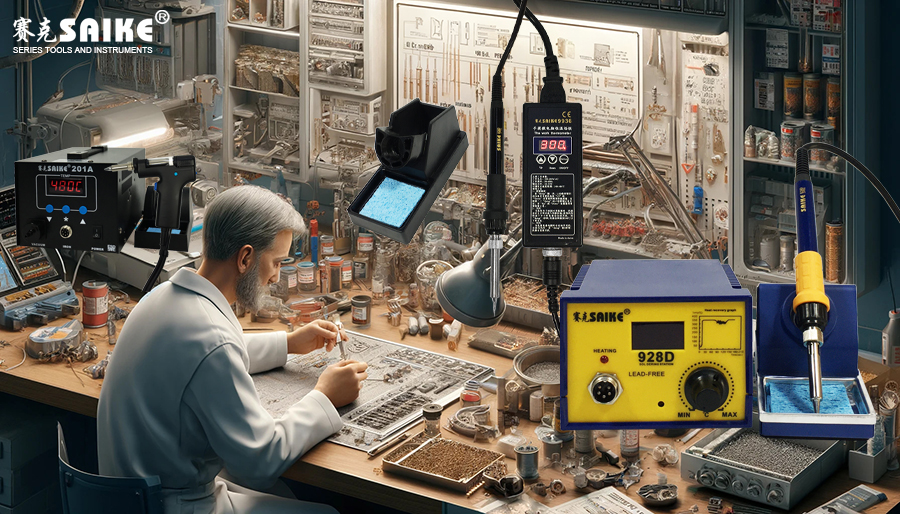
SK-YJ000DLT-KP 100018
Soldering iron welding is an indispensable skill in electronic production and maintenance, and the selection and use of welding materials is a key part of this skill. Proper material selection can not only improve welding quality but also ensure the stability and safety of the circuit. The following will introduce the selection and use of soldering iron welding materials in detail.
I. Selection of soldering wire
1.Alloy composition: Solder wire is usually made of tin (Sn) and lead (Pb) alloys, but for environmental and health considerations, lead-free solder such as tin, silver, copper alloy (SAC) is increasingly used nowadays. The melting point and fluidity of lead-free solder may differ from that of lead-containing solder, so it is necessary to understand its characteristics before use.
2.Diameter specification: The diameter of the soldering wire has a great influence on the soldering effect. Thin soldering wire is suitable for fine soldering, while thicker soldering wire is suitable for soldering large areas or occasions that require more soldering. The appropriate diameter should be selected according to specific needs.
3.Flux type: Solder wire usually contains flux to improve soldering wettability and fluidity. Different types of fluxes are suitable for different soldering conditions and requirements, so selection should be based on actual conditions.
II. Selection of flux
1.Rosin flux: Rosin is a commonly used flux with good soldering effect and is easy to clean after soldering. Rosin flux is suitable for most soldering iron welding occasions.
2.Active flux: Active flux contains stronger chemically active ingredients, suitable for soldering materials or surfaces that are difficult to wet. However, more thorough cleaning is required after use.
3.Lead-free flux: For soldering with lead-free solder, a matching lead-free flux should be selected to ensure soldering quality and environmental requirements.
III. Selection and maintenance of soldering iron tip
1.Soldering iron tip shape: The shape of the soldering iron tip should be selected according to the specific soldering requirements. For example, a pointed tip is suitable for fine soldering, while a blade tip is suitable for soldering large areas. Ensuring that the soldering iron tip matches the soldering task can improve soldering efficiency and quality.
2.Soldering iron tip material: The soldering iron tip is usually made of copper or other metals with good thermal conductivity. Choosing a good quality soldering iron tip can ensure uniform heat transfer and a longer service life.
3.Maintenance of soldering iron tip: Regularly clean the oxide and residual solder on the soldering iron tip to maintain its good thermal conductivity. Special soldering iron tip cleaner or fine sandpaper can be used for cleaning. At the same time, avoid prolonged high-temperature heating to extend the service life of the soldering iron tip.
IV. Precautions for use
1.Temperature control: Reasonably set the temperature of the soldering iron according to the requirements of the soldering material and components. Too high or too low temperature may affect the soldering quality and component performance.
2.Soldering time: Control the soldering time to avoid damage to components or solder pad fall off caused by excessive heating. At the same time, ensure that the solder is fully melted and wets the soldering point.
3.Soldering environment: Perform soldering in a well-ventilated environment to avoid inhaling harmful fumes. Keep away from flammable items to prevent fires.
4.Inspection after soldering: After soldering is completed, check whether the soldering joints are smooth, full, and free of defects such as cold soldering or incomplete soldering. If necessary, a magnifying glass or microscope can be used for detailed inspection.
V. Conclusion
By reasonably selecting and using soldering iron welding materials, we can improve welding quality and work efficiency, while ensuring the stability and safety of the circuit. Continuously sum up experience in practical operations and improve one’s welding skill level.