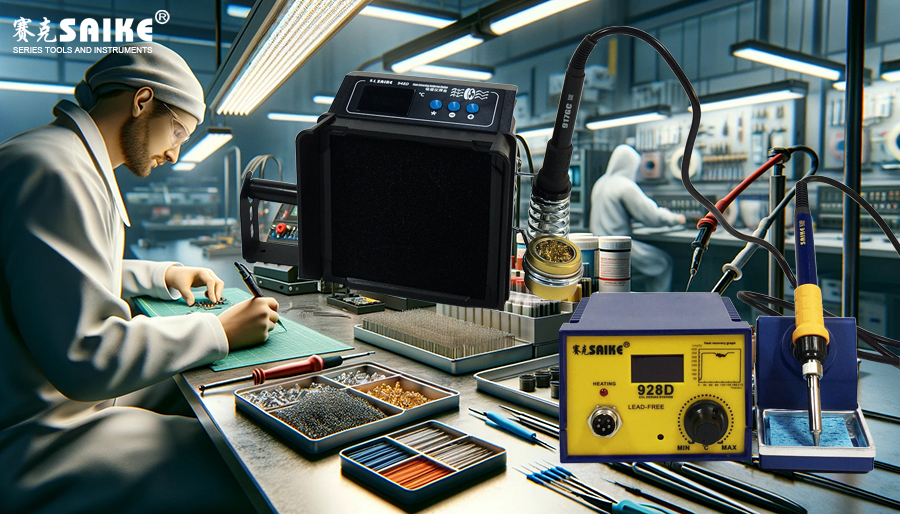
SK-YJ000HT-KP 100021
Soldering at a soldering station is an important technique in electronic manufacturing and repair work. To ensure soldering quality and efficiency, it is crucial to choose suitable soldering materials. This article will delve into the preparation and selection of soldering materials for soldering stations, including selection criteria and preparation processes for key components such as solder, flux, and soldering iron tips.
I. Selection and Preparation of Solder
Solder is one of the most critical materials in the soldering process and must be chosen based on the specific needs of the soldering task.
1.Selection Criteria:
– Melting point: Choose solder with a suitable melting point to ensure it can melt and solidify without damaging electronic components.
– Composition: Consider environmental requirements and select lead-free solder, such as Sn-Ag-Cu (tin-silver-copper) alloy, or traditional Sn-Pb (tin-lead) solder based on the application environment and regulatory requirements.
– Diameter: Select the appropriate diameter of solder wire based on the soldering precision required. Fine electronic soldering often uses thinner solder wire.
2.Preparation Process:
– Storage: Solder should be stored in a dry, clean environment to prevent oxidation and contamination.
– Inspection: Before use, check that the solder is clean and free from oxidation or other visible damage.
II. Selection and Use of Flux
Flux helps the solder flow and removes oxides from metal surfaces, improving soldering quality.
1.Selection Criteria:
– Activity: Choose a flux with suitable activity for the solder and operating temperature, ensuring it can effectively remove oxide layers without damaging components.
– Residues: Consider the impact of flux residues on the circuit, and you may need to select a flux that is easy to clean or leaves minimal residues.
2.Preparation Process:
– Quantity: Apply an appropriate amount of flux. Too much can contaminate the circuit board, while too little may result in unstable solder joints.
– Method: Use a brush, syringe, or specialized flux pen to evenly apply the flux.
III. Selection and Preparation of Soldering Iron Tips
The shape and size of the soldering iron tip significantly impact soldering accuracy and efficiency.
1.Selection Criteria:
– Shape: Select a soldering iron tip shape suitable for the soldering task. For example, a pointed tip is suitable for precision soldering, while a beveled tip is suitable for larger solder joints.
– Material: Choose a high-temperature resistant and thermally conductive soldering iron tip, commonly made of copper and possibly plated with nickel or chromium for durability.
2.Preparation Process:
– Cleaning: Clean the soldering iron tip before and after use to remove oxide layers and solder residues.
– Preheating: The soldering iron tip needs to be preheated to a suitable temperature for solder melting.
IV. Safety and Environmental Considerations
When selecting and preparing soldering materials, safety and environmental factors must also be considered.
1.Safety Measures:
– Ventilation: Ensure good ventilation in the soldering area to reduce harmful fumes from flux and solder that can affect health.
– Protective equipment: Operators should wear necessary protective equipment, such as safety glasses and antistatic gloves.
2.Environmental Impact:
– Waste disposal: Properly dispose of waste generated during the soldering process, including used flux containers and residual solder.
V. Conclusion
Selecting and preparing the correct soldering materials is crucial for successful soldering work. Operators need to carefully choose and prepare solder, flux, and soldering iron tips based on the specific requirements of the soldering task. Additionally, emphasis should be placed on safety and environmental protection to ensure soldering work is not only efficient but also safe. By following these detailed guidelines, soldering quality can be significantly improved, extending equipment lifespan and protecting the operator’s health.