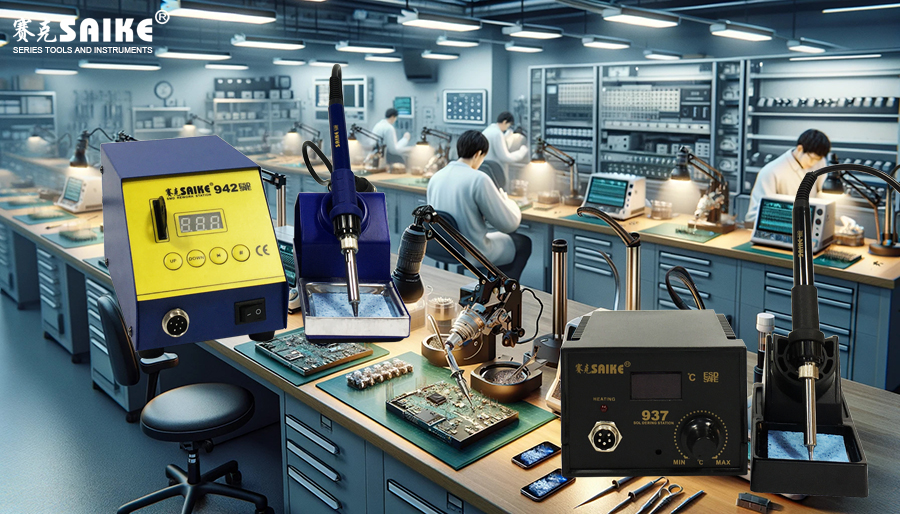
SK-YJ000HT-KP 100041
In the modern electronics manufacturing industry, precision welding of micro components is a crucial technique that ensures the high performance and reliability of complex electronic products such as smartphones, computers, and medical equipment. The welding process of micro components requires extremely high precision and control to cope with the continuous shrinkage of component sizes and the increasing complexity of designs. This article will delve into the key techniques, equipment selection, operational skills, and strategies for overcoming challenges in precision welding of micro components on a soldering station.
I. Key Techniques for Welding Micro Components
1.Selection of Soldering Station and Soldering Iron
– High-precision temperature-controlled soldering station: Choosing a soldering station with precise temperature control is crucial, as excessively high or low temperatures can damage micro components or result in weak solder joints.
– Micro soldering iron tips: Using fine-tipped or specially designed micro soldering iron tips can help operators accomplish precise welding tasks without damaging adjacent components.
2.Selection of Solder and Flux
– Low-temperature solder: Using solder with a lower melting point, such as SnAgCu (SAC) alloy, can reduce thermal stress on sensitive components.
– No-clean flux: Choosing a no-clean flux can avoid potential damage to micro components during the cleaning process after welding.
3.Optical Auxiliary Equipment
– Microscope or magnifying glass: Using a microscope or magnifying glass ensures clear visibility of the welding points, which is essential for precise placement of solder and assessing welding quality.
II. Welding Operation Skills
1.Precise Solder Position Control
– Solder wire and dispenser: Using thin solder wire or an automatic solder dispenser to precisely control the amount and position of solder prevents excess solder from causing short circuits or cold solder joints.
2.Heat Management
– Rapid heating and cooling: Quickly heating to a sufficient temperature to complete the welding and then rapidly cooling reduces the residence time of heat on the micro components.
3.Refined Welding Techniques
– ‘Drag soldering’ technique: This technique is very effective for micro components with denser pins. It involves gently dragging the soldering iron tip with solder on it across the pins, quickly forming uniform solder joints.
III. Strategies for Overcoming Challenges
1.Avoiding Electrostatic Damage
– Electrostatic discharge (ESD) protection: Using ESD protective measures such as anti-static mats and anti-static wristbands in the welding work area prevents electrostatic damage to microelectronic components.
2.Quality Control
– Welding inspection: Using X-ray inspection machines or optical inspection equipment (AOI) to check the quality of solder joints after welding ensures there are no issues such as short circuits, cold solder joints, or false solder joints.
3.Training and Skill Improvement
– Continuous training: Regularly training welding technicians, especially when new technologies or materials are introduced, ensures they master the latest welding techniques and best practices.
IV. Conclusion
Precision welding of micro components on a soldering station requires a high level of technical expertise and precise operation. By selecting appropriate tools, adopting correct welding materials and techniques, and implementing strict quality control procedures, welding quality can be effectively improved, extending the service life of electronic products. As electronic devices move towards smaller and more complex designs, the importance of precision welding technology will further increase, and the requirements for operational skills will continue to rise.