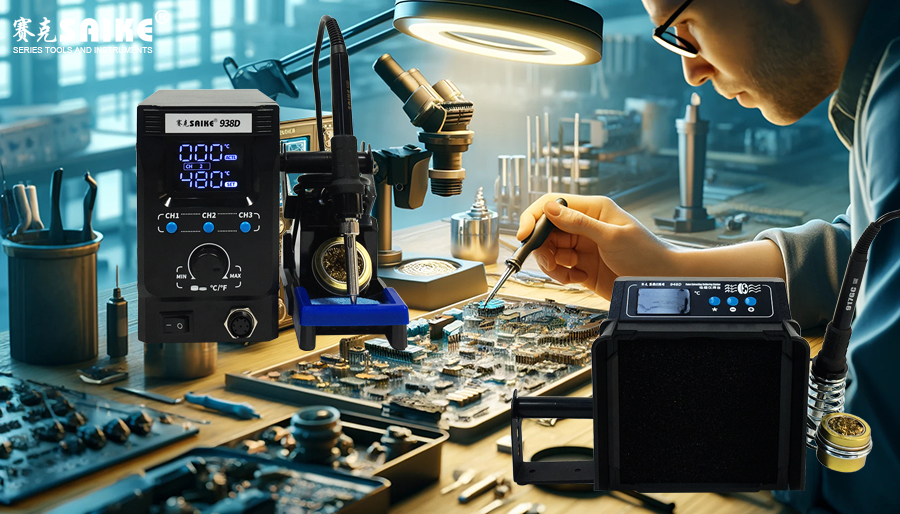
SK-YJ000HT-KP 100025
The inspection of soldering appearance quality is a crucial step to ensure the reliability and functionality of electronic products. Rigorous evaluation of soldering quality can prevent potential failures and improve product lifespan. This article will introduce the inspection process, evaluation criteria, and identification methods for common problems related to soldering appearance quality on the soldering station.
I. The Importance of Soldering Appearance Quality
The soldering appearance quality directly reflects the correctness of the soldering process and the reliability of solder joints. A good soldering appearance usually indicates that soldering parameters (such as temperature, time, solder, and flux usage) have been properly controlled. Additionally, excellent soldering appearance ensures the stability and long-term durability of electronic products during operation.
II. Basic Steps for Inspecting Soldering Appearance Quality
1.Visual Inspection
– Tools and Equipment: Use a magnifying glass, microscope, or Automatic Optical Inspection (AOI) equipment to enlarge and observe solder joints.
– Inspection Content: Check if solder joints are smooth, crack-free, and have sufficient and uniform solder covering the pads and pins. The solder joints should have a mountainous or pad-like shape, with no gaps between the solder and the soldering pad.
2.Structural Integrity
– No Cold Solder Joints: Cold solder joints occur when the solder has not completely melted and solidified, often manifesting as loose or powdery solder joints.
– No Weak Solder Joints: Weak solder joints typically manifest as poor contact between the solder joint and soldering pad, which can be checked by slightly shaking the component to see if the solder joint is firm.
3.Solder Distribution
– No Solder Overflow: Check for solder overflow around the solder joints, especially the risk of short circuits between adjacent solder joints.
– No Solder Bridges: Solder bridges occur when two or more solder joints are connected due to excess solder, which may cause circuit short-circuiting.
III. Evaluation Criteria for Soldering Appearance Quality
1.IPC Standards
Use standards from the International Electronics Manufacturing Initiative (IPC) to evaluate soldering quality. For example, IPC-A-610 is a commonly used standard for evaluating soldering quality in electronic assembly, which describes various soldering defects and acceptable conditions in detail.
2.Internal Standards
Many companies have developed more stringent internal soldering quality standards based on their product characteristics and application areas.
IV. Common Soldering Defects and Solutions
1.Cold Solder Joints and Weak Solder Joints
– Cause: Low soldering temperature or insufficient soldering time.
– Solution: Adjust the soldering station temperature setting, ensure sufficient soldering time, and use an appropriate amount of flux.
2.Solder Overflow and Solder Bridges
– Cause: Excessive solder usage or improper soldering technique.
– Solution: Control the amount of solder used, improve soldering skills, such as adjusting the soldering iron angle and contact time appropriately.
V. Conclusion
Inspecting soldering appearance quality on the soldering station is a fundamental aspect of ensuring electronic product quality. Through careful visual inspection, structural integrity assessment, and observation of solder distribution, problems during the soldering process can be effectively identified and corrected. Additionally, following industry standards and continuously optimizing soldering processes are essential for improving soldering quality. These methods significantly enhance product reliability and performance, reducing maintenance costs in the later stages.