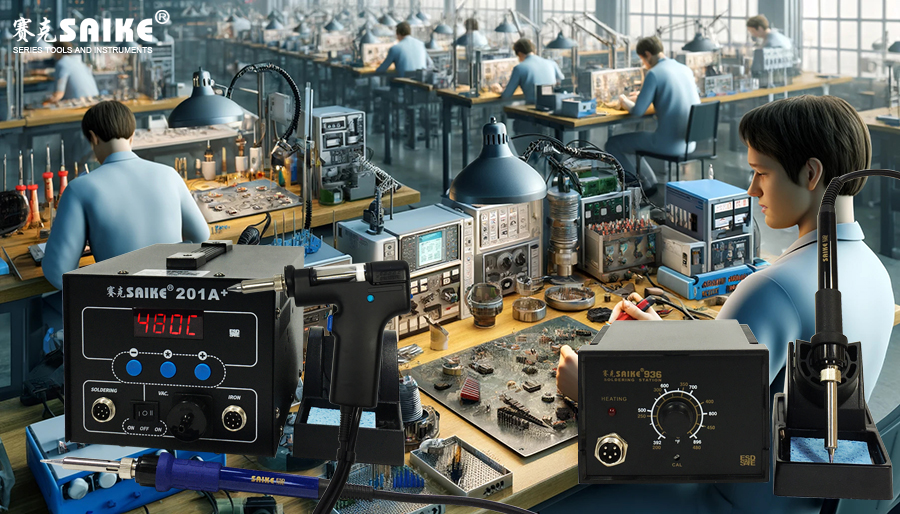
SK-YJ000HT-KP 100014
The welding joint is one of the core components of a welding station, and its design and selection are crucial to ensuring welding quality and efficiency. In the electronic manufacturing and repair industry, choosing the right welding joint suitable for specific applications can not only improve production efficiency but also significantly enhance product reliability and durability. This article delves into the design and selection of welding joints for welding stations, helping users understand how to choose the most suitable joint based on different welding requirements.
I. Basic Types of Welding Joints
The types of welding joints are primarily determined by their shapes and sizes, with different designs suitable for different welding tasks:
1.Conical Tip
– Applicable Scenarios: Fine welding, suitable for hard-to-reach small spaces or precision components.
– Characteristics: Provides a precise hot spot, ideal for small-scale precise welding.
2.Bevel Tip
– Applicable Scenarios: Larger welding points, such as the welding of surface mount components like SOIC.
– Characteristics: The bevel design increases the contact area with the solder, facilitating rapid heating of the solder joint.
3.Knife Tip
– Applicable Scenarios: Drag soldering technique, suitable for multi-pin components such as PLCC and QFP.
– Characteristics: The wider joint design allows for simultaneous heating of multiple pins, improving welding efficiency.
4.Hollow Tip
– Applicable Scenarios: Heavy welding operations requiring a larger heat reserve.
– Characteristics: The concave design can store more solder, suitable for a large number of repeated welding operations.
II. Material Selection for Welding Joints
The material of the welding joint is also a crucial factor affecting its performance. Common materials include copper, silver-plated copper, and iron-plated copper:
– Copper Joints: Good thermal conductivity, fast heating, but prone to oxidation, requiring regular maintenance and replacement.
– Silver-Plated Copper Joints: Good oxidation resistance, high wear resistance, but relatively high cost.
– Iron-Plated Copper Joints: High temperature resistance, wear resistance, suitable for long-term high-temperature operations, and a common choice for industrial applications.
III. Thermal Performance Analysis of Welding Joints
When selecting welding joints, thermal performance should also be considered, including heat capacity, thermal conductivity, and thermal stability. Joints with large heat capacity can provide more stable heat output, suitable for a large number of continuous welds, while joints with good thermal conductivity have fast heating speeds and short response times, suitable for rapid welding.
IV. Considerations for Selecting Welding Joints
When selecting welding joints, the following factors should be considered:
– Nature of the Welding Task: Select the corresponding joint type based on the precision of the welding task and the required heat distribution. Fine electronic work may require a conical tip, while large-area welding may be more suitable for a bevel or knife tip.
– Thermal Conductivity of the Material: The thermal conductivity of the welded material also needs to be considered when selecting joints. Materials with high thermal conductivity, such as copper or aluminum, require joints with high temperature and rapid heat recovery capabilities.
– Durability and Maintenance of Joints: Although high-quality joints may have a higher initial investment, they are more durable and economical in the long run. Choosing joints that are easy to clean and maintain will also reduce maintenance costs.
V. How to Choose the Right Welding Joint
When selecting a suitable welding joint, consider the following aspects:
– Type of Welding Task: Select the joint shape based on the complexity and precision of the welding task.
– Material Durability: Choose materials that match the working environment and welding frequency.
– Thermal Performance Requirements: Select joints based on welding speed and temperature stability requirements.
– Budget and Cost-Effectiveness: Consider the cost-effectiveness and choose the most suitable joint based on overall demand.
VI. Conclusion
Choosing the right welding joint is crucial to improving welding quality and efficiency. Understanding the characteristics and applicable scenarios of different types of joints, combined with actual welding requirements and budgets, can help select the most suitable welding joint, thereby improving the overall performance and efficiency of welding operations.