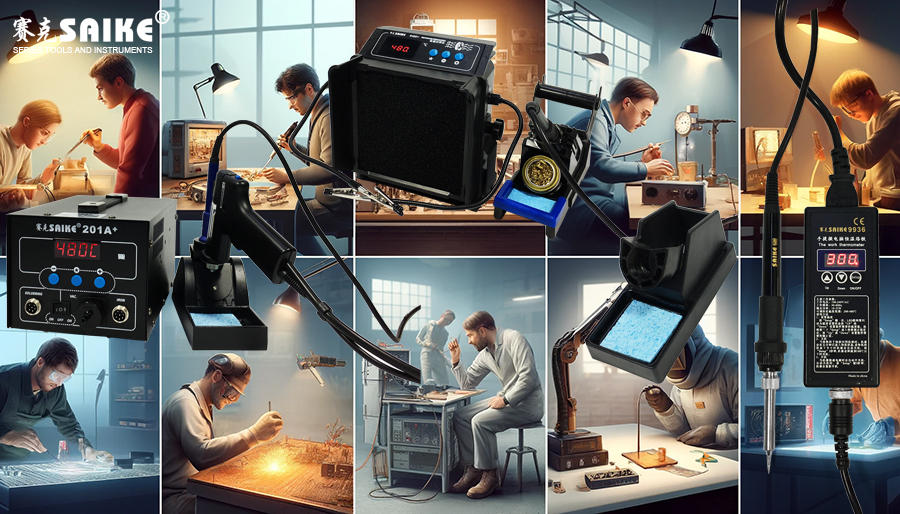
SK-YJ000DLT-KP 100006
The soldering iron, as an essential tool for electronic production and maintenance, comes in various types and functions. Choosing the right soldering iron for different application scenarios is crucial as it not only improves work efficiency but also ensures the quality of the work. In this article, we will delve into how to select the appropriate soldering iron based on different scenarios.
I. Home maintenance and DIY production
For home maintenance and DIY projects, a soldering iron with moderate power and simple operation is generally sufficient. These soldering irons are often compact, portable, and affordable. Internal heating soldering irons are ideal for household use due to their high thermal efficiency and fast heating time. Additionally, some soldering irons with temperature adjustment functions allow users to adjust the temperature according to welding needs, meeting the welding requirements of different materials while preventing damage to components caused by excessive temperature.
II. Professional electronic production and maintenance
For professional electronic production and maintenance personnel, the choice of soldering iron becomes more sophisticated. This type of work often requires high-precision and high-stability soldering irons. A constant temperature soldering iron is a good choice as it maintains a stable welding temperature, avoiding temperature fluctuations that can affect welding quality. Meanwhile, although professional-grade external heating soldering irons have relatively low thermal efficiency, they have a long service life and are suitable for long-term, high-intensity use.
III. Industrial production and manufacturing
In industrial production and manufacturing, more factors need to be considered when choosing a soldering iron. Industrial-grade soldering irons typically have higher power and a larger heating area to accommodate large-scale, high-efficiency production needs. Additionally, industrial soldering irons should possess good durability and stability to ensure normal operation in harsh working environments. For specific production requirements, specially designed soldering irons can be selected, such as those with unique tip shapes or materials, to adapt to different welding materials and process requirements.
IV. Scientific research and education
In the field of scientific research and education, the choice of soldering iron focuses more on precision and controllability. For example, when researching new materials or performing precision welding, a soldering iron with high-precision temperature control is necessary. These soldering irons are usually equipped with advanced temperature control systems that can monitor and adjust the temperature of the soldering iron tip in real-time, ensuring the accuracy and reproducibility of the welding process. At the same time, for teaching demonstrations and student practices, soldering irons that are compact and easy to operate can be selected.
V. Special application scenarios
In some special application scenarios, such as high temperature, high humidity, and corrosive environments, the choice of soldering iron requires extra caution. In these environments, soldering irons with good weather resistance and anticorrosion properties should be selected. For instance, soldering iron tips made of special materials can resist high-temperature oxidation and corrosion, while waterproof soldering irons can operate normally in high-humidity environments. Additionally, soldering irons with special functions, such as solder-sucking soldering irons, can be chosen to meet specific needs.
VI. Summary
In summary, when selecting a soldering iron, we should make comprehensive considerations based on specific application scenarios and needs. Different types of soldering irons have their unique characteristics and scope of application. Only by choosing the appropriate soldering iron can we ensure the smooth progress of welding work and achieve the desired results.