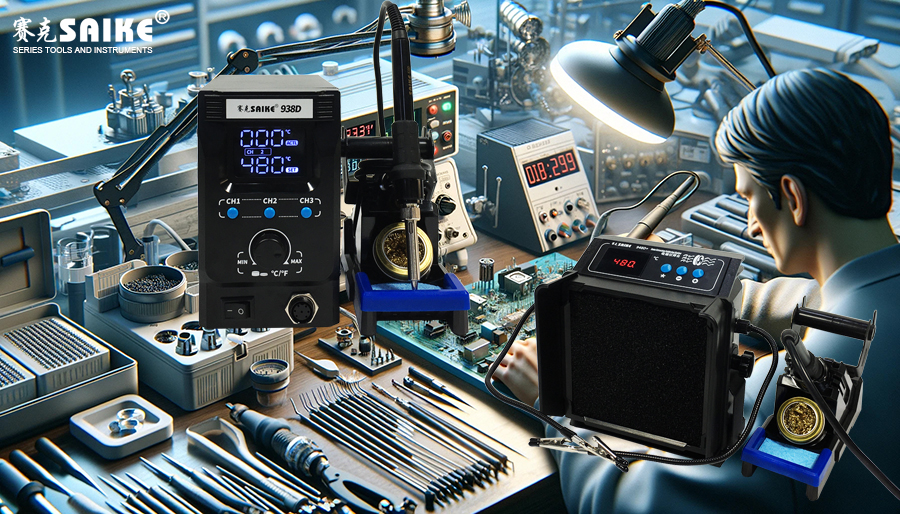
SK-YJ000HT-KP 100028
Soldering station welding of electronic components is a core aspect of electronic manufacturing and repair, involving various techniques and intricacies to ensure reliable connections and component functionality. This article delves into the specifics of soldering station welding for electronic components, covering crucial considerations during the welding process, soldering techniques for different components, and methods for achieving high-quality welds.
I. Key Factors in Soldering Electronic Components
1.Thermal Management
Electronic components, particularly semiconductor devices, are thermally sensitive, and excessive heating can cause damage. Therefore, soldering stations require precise temperature control, often utilizing stations with highly accurate temperature regulation to prevent exceeding the maximum temperature tolerance of the components.
2.Soldering Material Selection
Choosing the right solder and flux is crucial for soldering quality. Lead-free solders are increasingly popular due to their environmental friendliness, but they typically have a higher melting point than traditional tin-lead solders, necessitating a soldering station capable of reaching higher temperatures.
3.Precision and Delicacy
Electronic component solder joints are often very small, demanding precision tools. Soldering stations are typically equipped with fine soldering tips suitable for delicate work, and the station’s stability and operator precision directly impact soldering quality.
II. Soldering Characteristics of Different Electronic Components
1.Surface Mount Technology (SMT) Components
– Soldering Temperature: SMT components, due to their small size and thin walls, often require lower soldering temperatures and quick soldering processes.
– Soldering Technique: This involves the use of fine-tipped soldering irons and precise temperature control. Quick-touch methods are commonly used to minimize heat exposure to the components.
2.Plated Through-Hole (PTH) Components
– Soldering Temperature: Since PTH component leads need to be soldered on the other side of the board after passing through holes, higher temperatures are required to ensure the solder completely fills the holes.
– Soldering Technique: Thicker soldering tips provide more heat, and the soldering time is longer compared to SMT components, ensuring the solder flows and fills completely.
III. Soldering Quality Assessment
The assessment of welding quality mainly relies on visual inspection and functional testing:
– Visual Inspection: Checking for smooth solder joints without cold solder joints or solder balls. The solder joints should have a typical conical or pad-like shape, with the solder evenly covering the pad and component leads.
– Functional Testing: Performing electrical performance tests on the soldered circuit board to verify that all connections meet the design requirements electrically.
IV. Methods for Achieving High-Quality Soldering
1.Clean Operating Environment
Maintaining a clean soldering environment prevents dust, grease, and other contaminants from affecting soldering quality. Components and pads should be cleaned before soldering to eliminate oxides or impurities.
2.Using Appropriate Soldering Aids
Tools like solder suckers, third-hand tools, and magnifying glasses assist operators in soldering more precisely, especially when handling tiny or complex components.
3.Continuous Training and Practice
Soldering skills require ongoing practice and updating, particularly when new techniques and materials are introduced into the production process. Regular training helps soldering operators maintain technological advancement and efficiency.
V. Conclusion
Soldering station welding for electronic components demands precise control and high skill, involving multiple technical aspects and considerations. By optimizing soldering parameters, selecting suitable tools and materials, and ensuring a suitable operating environment, soldering quality can be significantly improved, guaranteeing the performance and reliability of electronic products. Ongoing skill training and quality assessments are crucial for maintaining high soldering standards.