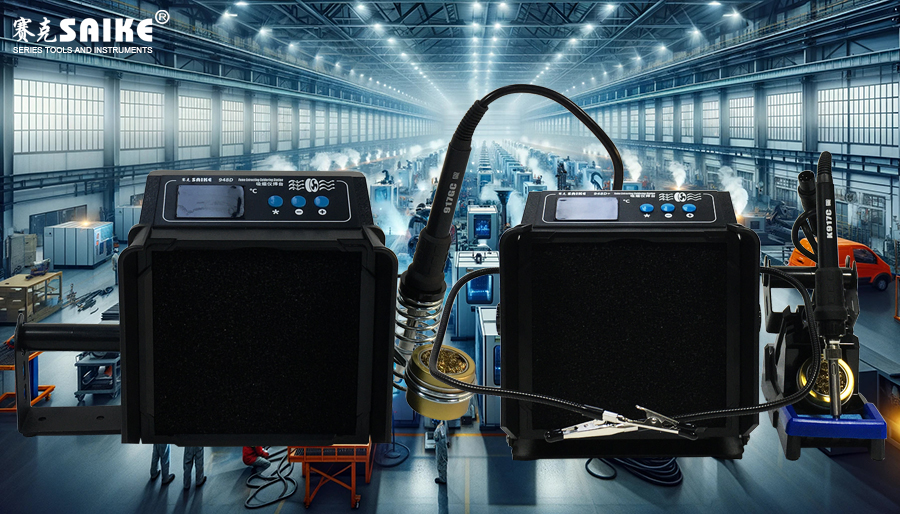
SK-YJ000XYY-KP 100022
Deploying fume extractors is an important measure to improve the quality of the welding work environment, protect employee health, and comply with environmental protection regulations. Successful cases can provide practical experience and insights for other companies. This article will analyze two cases of successful fume extractor deployment, exploring their deployment strategies, challenges faced, solutions implemented, and achieved results.
Case 1: Large Automobile Manufacturing Enterprise
Background:
The enterprise has multiple production bases worldwide, involving a lot of welding operations. To improve production efficiency while ensuring compliance with strict environmental regulations, the company decided to deploy efficient fume extractors at all welding workstations.
Challenges:
– Widespread welding operations: Diverse welding processes and materials lead to a variety of fumes, requiring a versatile and efficient solution.
– Regulatory compliance: Environmental regulations vary across different countries and regions, necessitating compliance with local laws for all equipment.
Solutions:
– Selection of high-standard fume extractors: Purchase fume extractors with HEPA and activated carbon filtration technology to capture multiple harmful substances.
– Customized deployment: Design specific fume extractor deployment plans according to the needs of different workstations, including the combined use of mobile and stationary fume extractors.
– Employee training and advocacy: Conduct comprehensive employee training, emphasizing the importance of fume extractors and teaching correct usage and maintenance methods.
Results:
– Significant improvement in air quality: The air quality within the welding area has been significantly improved, enhancing employees’ health status.
– Compliance with regulatory requirements: Successfully passed environmental inspections, avoiding fines due to non-compliance.
Case 2: Medium-sized Electronic Component Manufacturing Enterprise
Background:
This enterprise specializes in the production of high-precision electronic products, where welding processes demand an extremely clean environment. To ensure product quality and employee health, the company decided to deploy fume extractors in critical production areas.
Challenges:
– Space limitations: The production workshop has limited space, requiring fume extractor deployment without affecting operations.
– High precision requirements: Products are extremely sensitive to environmental dust and pollution, demanding fume extractors with very high filtration efficiency.
Solutions:
– Use of small, efficient fume extractors: Choose compact, high-efficiency fume extractors that save space while providing the necessary cleaning effect.
– Integration into the production line: Integrate fume extractors with production line equipment to control the release of fumes and particles at the source.
– Regular maintenance and performance monitoring: Establish a regular maintenance plan and use sensors to monitor air quality, ensuring continuous performance.
Results:
– Improved product quality: Significantly reduced pollution in the production environment, improving product qualification rates.
– Increased job satisfaction: Enhanced the working environment, boosting employee satisfaction and retention rates.
In conclusion, these two cases demonstrate successful practices in fume extractor deployment, emphasizing the importance of strategic selection, adaptive deployment, and strict maintenance management. Through these practices, companies not only improve the quality of the work environment but also comply with regulatory requirements, enhancing their social responsibility and market competitiveness. For any enterprise involved in welding operations, reasonable deployment and use of fume extractors are effective ways to achieve health, safety, and environmental goals.