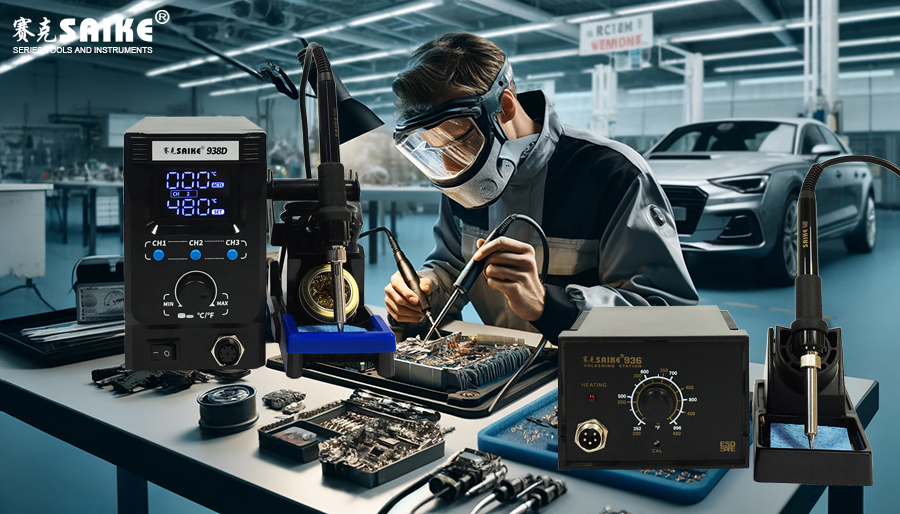
SK-YJ000HT-KP 100033
In the field of automobile manufacturing and maintenance, welding technology is one of the most common and critical processes for connecting metal components. Although soldering station welding, as a fine welding technique, is not as widespread in the automotive industry as large-scale automated welding methods such as spot welding or MIG (Metal Inert Gas) welding, it still plays an irreplaceable role in specific application scenarios. This article will explore in detail the applications, technical requirements, and key points to consider during implementation of soldering station welding in the automotive industry.
I. Applications of Soldering Station Welding in the Automotive Industry
1.Prototyping and Small Batch Production
– Prototyping: During the development stage of new vehicle models, soldering station welding is often used for the production and adjustment of prototype components, especially those complex or small batch metal parts.
– Small Batch Production: For special-purpose vehicles or customized components, soldering station welding provides a cost-effective manufacturing solution.
2.Welding of Electronic Components
– Electronic Component Welding: Many small electronic components in automotive electronic systems, such as sensors and connectors, require precise welding techniques to ensure the reliability of electrical connections.
3.Repair and Restoration
– Component Repair: In automobile maintenance, especially for the preservation of vintage cars or high-performance vehicles, soldering station welding is used to repair or replace small metal components, such as metal decorative parts and some small structural brackets.
II. Technical Requirements
1.Precise Temperature Control
– Temperature Adjustment: Automobile components are often made of various metal materials, including steel, aluminum, etc., which requires welding equipment to provide precise and adjustable temperature settings to adapt to the melting points of different materials.
2.High Strength and Durability
– Structural Integrity: The welding of automobile components needs to withstand a high-intensity usage environment, and the welding points must be extremely strong and durable to withstand vibration, impact, and corrosion.
3.Compliance with Environmental Standards
– Environmental Requirements: The automotive industry is subject to strict environmental regulations, and welding processes must use soldering materials and fluxes that comply with environmental standards such as ROHS.
III. Implementation Considerations
1.Welding Environment
– Cleanliness and Safety: Ensure that the welding environment is clean, dust-free, and grease-free, while complying with all safety regulations, such as proper ventilation and protective measures.
2.Operator Training
– Technical Proficiency: Welding operators should receive professional training to understand the welding techniques and characteristics of different metal materials, as well as how to handle various possible welding problems.
3.Quality Inspection
– Strict Quality Control: Implement strict quality inspection procedures to ensure that every welding point meets the high standards of the automotive industry. Adopt appropriate detection methods such as X-ray inspection and ultrasonic inspection to ensure that the welding points are defect-free.
IV. Conclusion
Although soldering station welding is not the most mainstream welding form in the automotive industry, it provides an irreplaceable solution in certain situations. Precise temperature control, fine operation, and the pursuit of high quality make soldering station welding occupy a place in the automotive industry, especially in prototyping, small batch production, and maintenance services. Through continuous technological improvement and strict quality management, soldering station welding will continue to contribute its unique value to automobile manufacturing and maintenance.