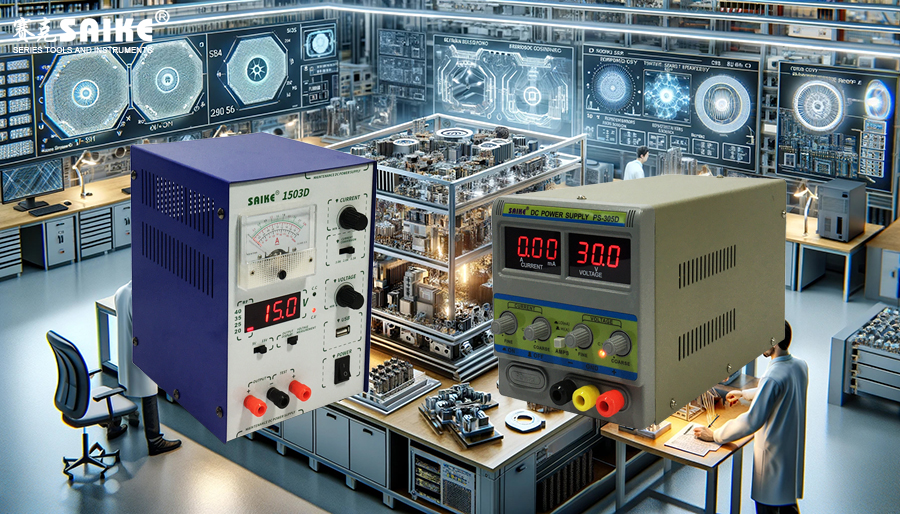
SK-YJ000DDXXQ-KP 100044
With the increasing demand for energy efficiency in electronic devices, power supply design is constantly innovating, involving the use of new materials and processes. These innovations aim not only to improve the efficiency of the power supply but also to reduce its size, extend its lifespan, and enhance its performance. This article explores some of the new materials and processes currently used in high-efficiency power supply design.
I. Application of New Materials
1.Wide Bandgap Semiconductors
– Silicon carbide (SiC) and gallium nitride (GaN) are currently the hottest wide bandgap semiconductor materials. These materials have the characteristics of high thermal conductivity, high electric field strength, and high switching frequency, allowing power equipment to operate at higher temperatures and voltages while maintaining a smaller size.
– The use of SiC and GaN can significantly improve the efficiency of the power supply, especially in high-voltage and high-frequency applications such as electric vehicle chargers and server power supplies.
2.Advanced Magnetic Materials
– Amorphous and nanocrystalline soft magnetic materials show superiority in improving the efficiency of power conversion. These materials have lower hysteresis loss and excellent high-frequency performance, making them suitable for the production of small and efficient inductors and transformers.
3.High Conductivity Materials
– High conductivity copper alloys and treated copper materials are used to reduce electrical resistance and enhance current transmission efficiency. These materials help reduce losses and improve the performance of the overall power supply design.
II. Development of New Processes
1.3D Integration Technology
– By stacking electronic components such as transistors, capacitors, and inductors using 3D integration technology, the size of the power module can be significantly reduced, and the power density can be increased. This technology also helps reduce connection lengths and parasitic parameters, thereby improving efficiency.
2.Optimization of Surface Mount Technology (SMT)
– High-speed automated SMT makes the production process more accurate and faster. Continuous optimization of SMT processes, such as more precise component placement and more efficient thermal management, further improves the quality and performance of power components.
3.Laser Direct Manufacturing (LDM) Technology
– The use of LDM technology in power packaging can create very precise and complex metal structures. This technology supports more complex cooling channel designs, effectively improving heat dissipation and contributing to the overall efficiency and reliability of the power module.
III. Conclusion
With the continuous development of new materials and processes, power supply design is becoming more efficient, smaller, and more reliable. The application of wide bandgap semiconductors is revolutionizing high-voltage and high-frequency power solutions, while advanced manufacturing technologies such as 3D integration and laser direct manufacturing are pushing the physical boundaries of power technology. In the future, as these materials and processes mature and become more widespread, we can expect power products to become more efficient, environmentally friendly, and have higher performance, meeting the stringent requirements of modern electronic devices for power supplies.