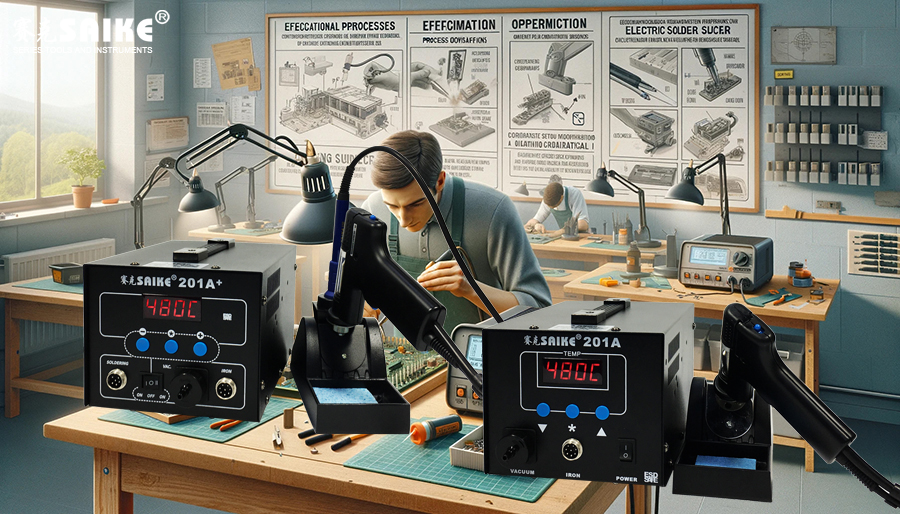
SK-YJ000DDXXQ-KP 100021
The electric solder sucker is an indispensable tool in electronic maintenance and DIY production, and its efficiency and operational quality directly affect the effectiveness and speed of soldering work. This article will introduce in detail how to enhance the efficiency of the electric solder sucker through techniques and process optimization.
I. Understanding the Basic Structure and Working Principle of the Electric Solder Sucker
1.Components of the Electric Solder Sucker:
– Heating Element: Usually a built-in heating core responsible for heating the soldering iron tip.
– Solder Sucking Pump: An electric pump that generates negative pressure to suck up melted solder.
– Control System: Includes power switch, temperature regulation, and suction force control.
2.Brief Description of Working Principle:
– When the electric solder sucker heats up to a certain temperature and the solder melts, the excess molten solder is quickly sucked up by activating the solder sucking pump.
II. Optimization of Operational Processes
1.Preparation Stage:
– Ensure that the soldering iron tip of the solder sucker is suitable for the current soldering point size.
– Preheat the solder sucker to a suitable temperature, usually between 350°C and 400°C.
2.Inspection Before Soldering:
– Clean the soldering iron tip to ensure that no solder residue or dirt affects heat conduction.
– Check if the solder sucking pump is unobstructed and ensure there is no blockage.
3.Optimizing Solder Sucking Operation:
– Hold the gun close to the soldering point with one hand to heat it, and prepare to suck the solder with the other hand.
– After the soldering iron tip completely covers the soldering point, quickly activate the solder sucking pump to efficiently suck up the molten solder in a short time.
III. Techniques to Enhance Usage Efficiency
1.Proper Temperature Adjustment:
– Adjust the working temperature of the solder sucker according to the different materials of the solder and soldering point to avoid overheating or insufficient heating.
2.Reasonable Allocation of Solder Sucking Time:
– Control the time of each solder sucking to achieve the best soldering effect in the shortest time and reduce thermal damage.
3.Regular Maintenance of the Solder Sucker:
– Regularly clean the solder sucking pump and soldering iron tip to maintain good working condition.
– Check the power cord and solder sucking pipeline to prevent aging or damage that affects usage efficiency.
4.Proficient Operational Skills:
– Practice regularly to improve operational proficiency and efficiency.
– Learn and apply new soldering techniques and methods.
IV. Summary
Optimizing the usage processes and techniques of the electric solder sucker can significantly improve the efficiency of maintenance or production and extend the equipment’s lifespan. By reasonably adjusting operational parameters, maintaining good equipment maintenance, and continuously improving personal operational skills, the work performance of the electric solder sucker can be maximized, making it a powerful assistant in electronic work.